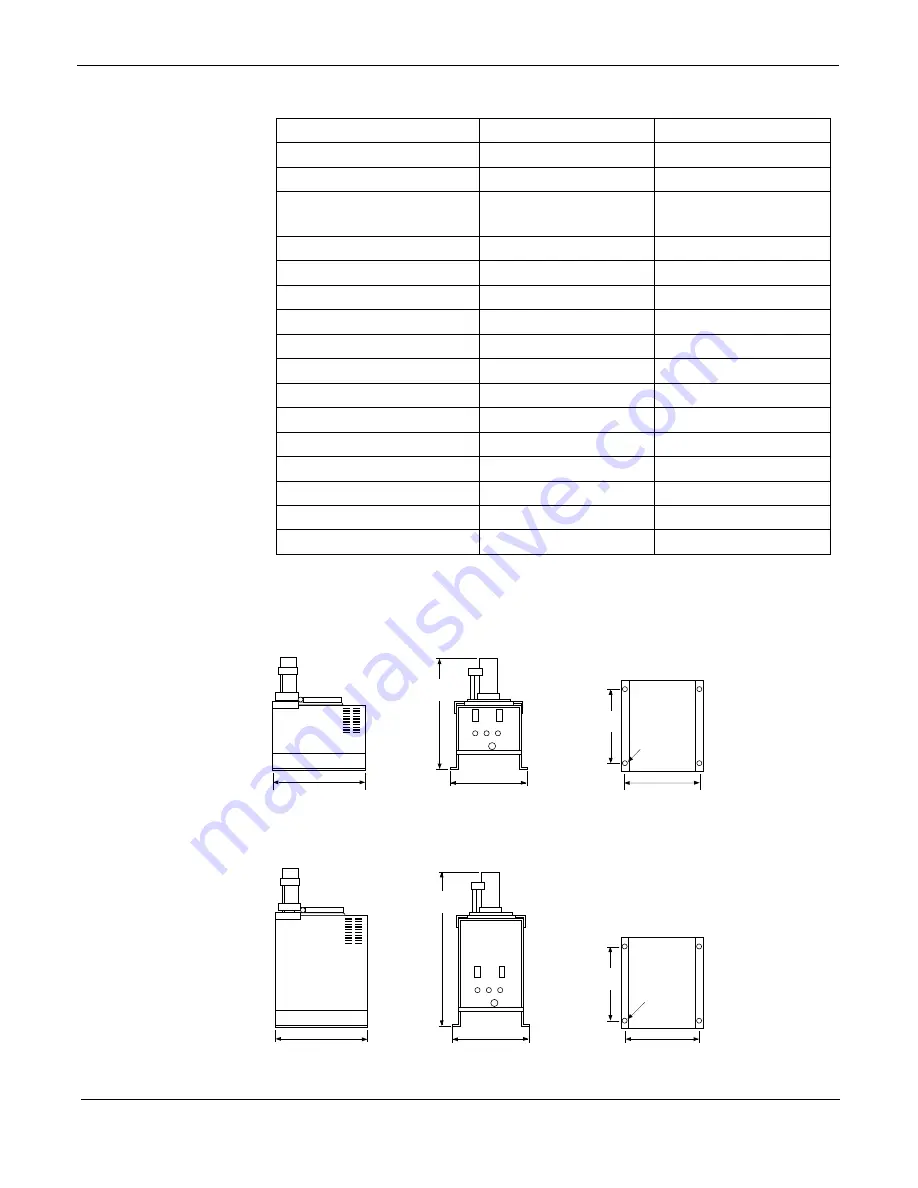
3.5 Motor Speed, Adhesive Pressure, and Flow Rate
Recommended Adhesive
Pressure Range*
Maximum Flow Rate*
V1-675 Pump
25 kg/hr
21 kg/hr
*Based on standard, packaging grade hot melts at 1000 cps. Varies with
adhesive and tank temperature. Consult factory representative for non-
standard requirements.
3.6 Dimensions
317.5 mm (12.5 in.)
355.6 mm (14 in.)
342.9 mm (13.5 in.)
508 mm
(20 in.)
269.7 mm
(10.62 in.)
6.3 mm
(0.25 in.) dia.
0960149a
LS10 Hot Melt Unit
355.6 mm 14 in.)
342.9 mm 13.5 in.)
698.5 mm
(27.5 in.)
269.7 mm
(10.62 in.)
317.5 mm (12.5 in.)
6.3 mm
(0.25 in.) dia.
0970014
LS20 Hot Melt Unit
Frequency
50-60 Hz
Motor Speed
44/min (rpm)
100–300 psi
689.48–2,068.43 kPa
V4-675 Pump
6.89–20.68 bar
55 lb/hr
45 lb/hr
© Copyright 2010 Astro Packaging
LS10 and LS20 19600-121
7
Содержание LS10 Series
Страница 1: ...LS10 and LS20 Series Hot Melt Units Manual Number 19600 121 Revision E 800 401 1441 800 401 1441 ...
Страница 2: ... 800 401 1441 ...
Страница 4: ... Copyright 2010 Astro Packaging 800 401 1441 ...
Страница 37: ...14 13 10 6 1 4 3 2 5 7 8 11 12 9 4 0950178 Copyright 2010 Astro Packaging LS10 and LS20 19600 121 31 ...
Страница 43: ... Copyright 2010 Astro Packaging LS10 and LS20 19600 121 37 ...