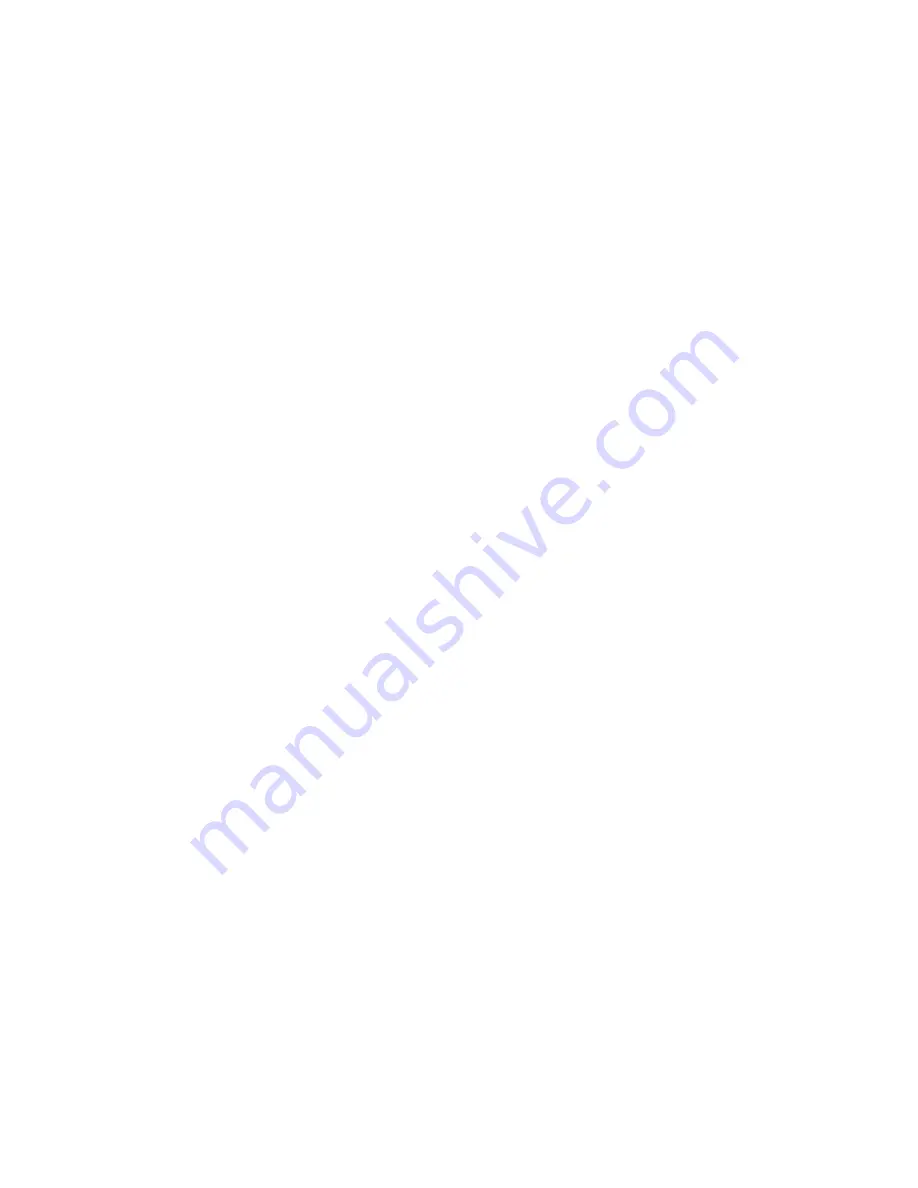
Solution:
Although it is good practice to cap the pipe to reduce contamination and windflow, it may cause
the bead to disappear especially in short sections of pipe (less than 4 feet). Since the UF2000/2 creates a
tremendous amount of heat, the air in the pipe is heated and expanded. If the air is not allowed to flow out
the pipe end, it will flush back through the heating element and out through the openings in the clamp,
cooling the joint as it rushes by the molten material. To avoid this, remove caps or use caps that are
perforated. Perforation needs to be several holes that are 1” in diameter. When utilizing caps, it is
necessary to inspect the bead formation. If the bead disappears, more holes are required in the caps. Also,
when welding fittings (90’s), it is better to turn them so that there is not an upward opening that may create
a “chimney” like affect. This is most common in larger diameters (6”). If it is not possible to turn the
fitting on its side, then caps with perforation should be utilized.
Common Concern #4
Burnt Joint:
If a joint appears discolored under light, it may be slightly burned. The burning is normally
caused by insufficient planing or incorrect welding temperature.
Solution:
Each time a joint is conducted, the pipe end must be planed to the mechanical stop on the planer.
Insufficient planing will cause the pipe to be closer to the heating element and cause the material
to “burn” rather than melt. Always double check your planing and also check the security of the
pins and mechanical stops on the planer.
If “burning” of joints persists, it may be due to the incorrect calibration of the heating element.
The heating element can be recalibrated in the field, contact Asahi/America for assistance. It is
important to note that heating elements cannot be switched from one tool to another without
requiring calibration. Each tool has two specific heating elements (6” and 10”) that are calibrated
at the factory prior to shipment, for that particular unit only.
Asahi/America, Inc.
UF 2000/1
Page 10 of 1
8