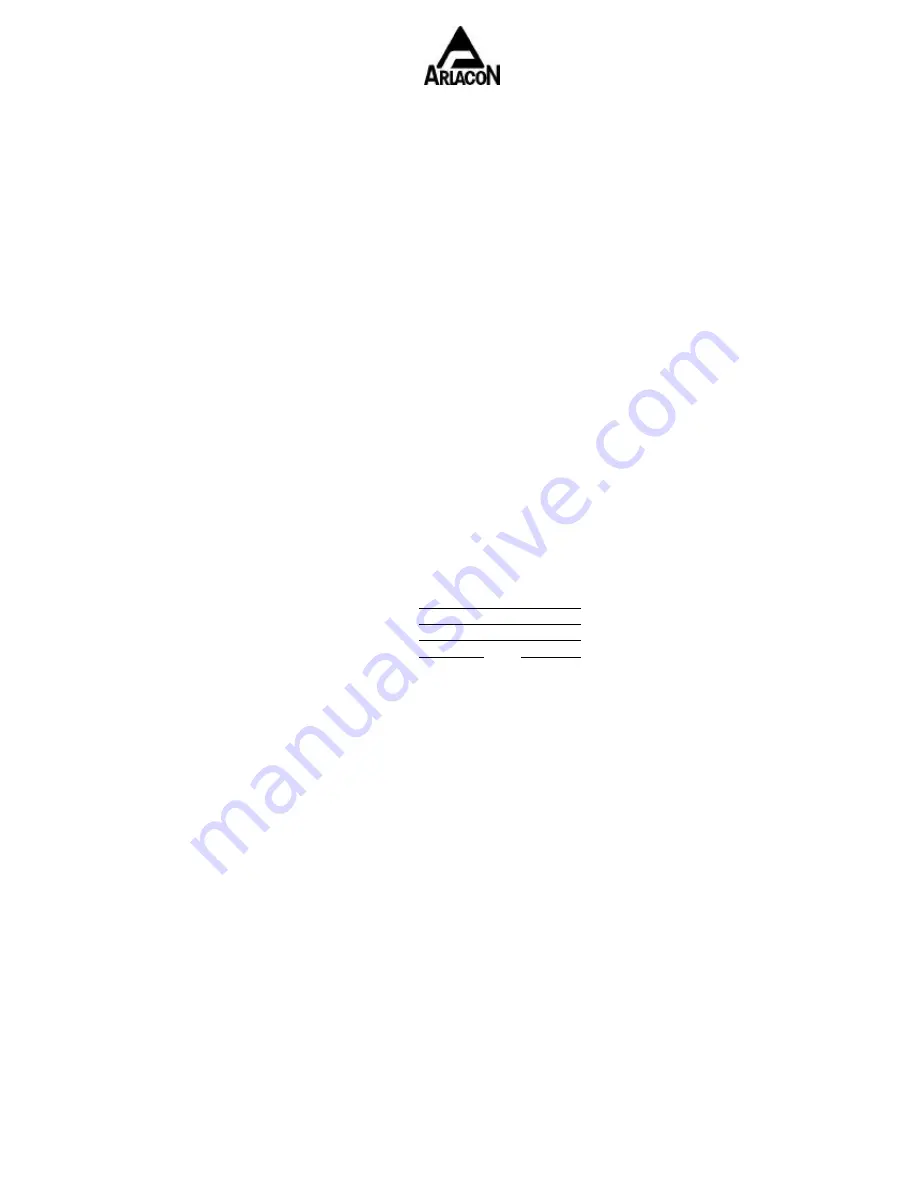
ARLACON MC300
MC300MAE
Control system
User's manual
18
Product code 1003418
2.4 MCWAY I/O MODULES
McWay i/o modules provide a method for building complete control systems using the
ARLACON MC300 series control unit. Modules are available for connecting position feedback
controlled axes with either incremental or absolute encoders, digital and analog inputs and
outputs. Up to 504 output bits and 504 input bits can be connected to the MC300 McWay loop
with a refresh period of down to 1ms.
Since the refresh rate of the McWay I/O loop coincides with the McBasic PIDFREQ setting,
value >1000 will limit the number of input and output bits available. With PIDFREQ=2000 the
refresh period is 0,5ms and the max. number of input and output bits is 240.
To use McWay modules with MC300 each module must be selected to operate at 1,25Mbaud.
Further instructions about different McWay modules are available in the ARLACON McWay
I/O system user’s manual.
2.5 CONNECTING TO A TERMINAL OR PC
To program the MC300 it is necessary to connect a display terminal, a PC or ARLACON
program development system to the :CN serial communications channel of the control unit.
To communicate, the MC300 only needs three wires connected:
signal
MC300
MC300 w.
ARLACON
PC
PC
at MC300
DPI-S1
encl. D-15
D-25
D-25
D-9
female
male
male
pin
pin
pin
pin
pin
signal
RS232 in (RxD)
1
2 3
2
3
TxD
RS232 out (TxD)
2
3 2
3
2
RxD
signal ground
3
7 7
7
5
gnd
chassis ground
chassis
1 shield
For interference protection use shielded cable and connect shield to system ground (chassis)
at MC300. Some PC computer programs also require pins 5,6 and 20 (D-25) or 8,6 and 4 (D-9)
to be connected to each other to bypass hardware handshake.
For communications, please use a terminal program with xon/xoff handshake such as
PROCOMM, PCPLUS, WINDOWS TERMINAL etc. Set the communication to 9600 baud, 8
bit, no parity, xon/xoff handshake.
With display terminals with connector pinouts different from above, please connect according
to RS232 signal names.
2.6 EMC considerations
Electromagnetic compatibility (EMC) is an important design factor in industrial automation as
well as in other electrical installations. The purpose of EMC is to ensure that electrical
equipment emit electromagnetic energy (interference) less than can cause malfunction of
other equipment. The difference between the level of emissions and the level of susceptibility
is called the EMC margin.
There are different standards and regulations specifying the test and measuring techniques
and acceptable levels for conducted and radiated emissions and immunity.