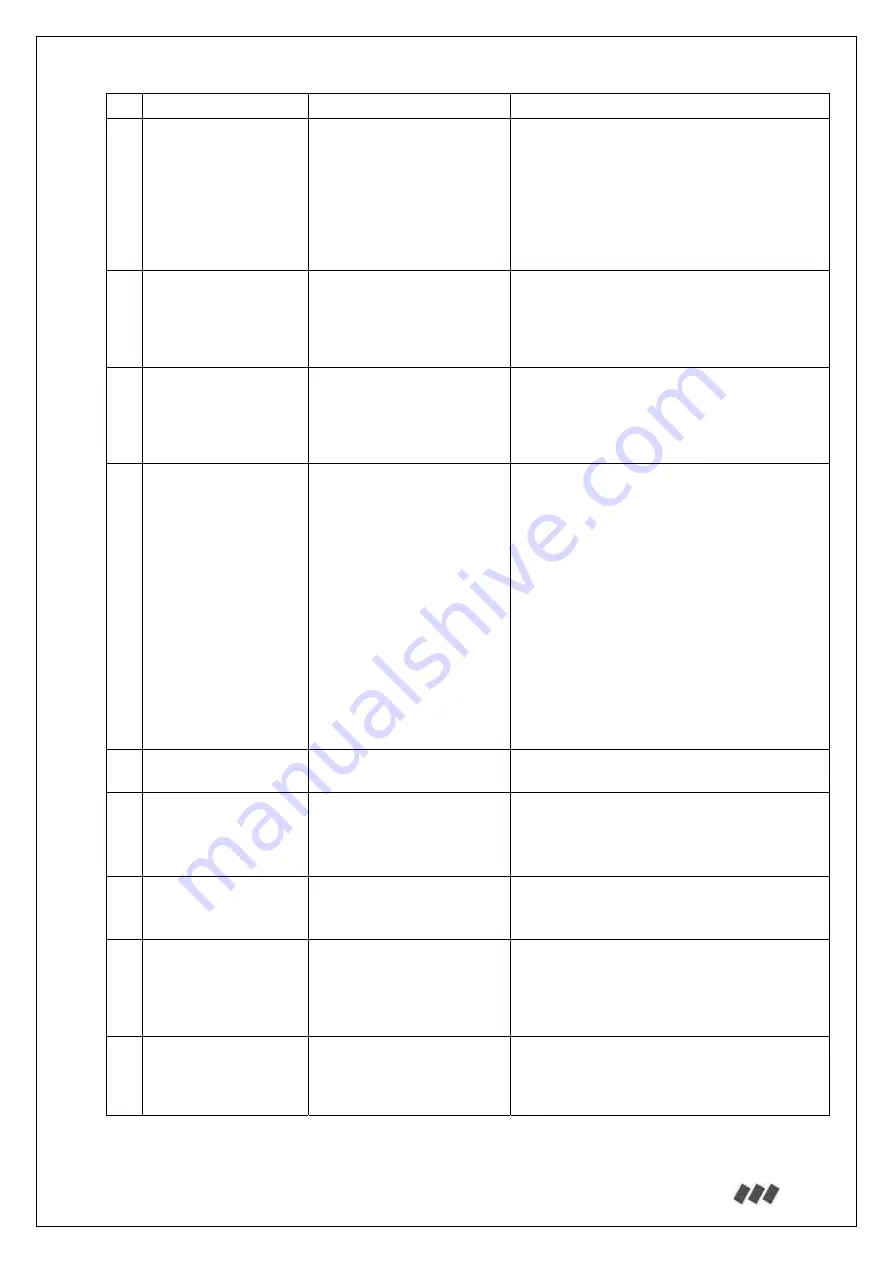
ARKEL Elektrik Elektronik Ltd.
Ş
ti. www.arkel.com.tr
08.2012
ADrive
75
No
Trip Meaning
Probable Causes / Corrective Actions
07 POWER
FAILURE
The main supply voltage L1,
L2, L3 oscillates unusually.
1- The main supply voltage is too low.
2- An open-phase error occurred at the input
power supply.
3- A momentary power loss occurred.
4- The wiring terminals for the input power
supply are loose.
5- The voltage fluctuations in the input power
supply are too large.
08
AUTO TUNE FAILS
A fault occurred during
autotuning in open loop mode.
Autotune operation cannot be
completed.
1- Check motor connection. Motor connection
may not be done properly.
2- Motor contactor may not be switching. Be sure
that the motor contactor closes when inverter is
running.
09 OVER
SPEED
The speed read from encoder
is too high.
1- Motor speed may be higher than the reference
speed. Check motor setup in the menu.
2- Compare the pulse number setting in the menu
“Motor Setup - Encoder Resolution” with the
encoder pulses and correct if necessary.
10 BAD
ENCODER
SGNL
The encoder signals oscillates
unusually.
1- Check encoder connection and encoder
voltage.
2- Check the connection between encoder and
motor.
3- If the encoder cable is not shielded, use a
shielded cable.
4- If the motor cable is not shielded, use a
shielded cable.
5- Encoder cable may be placed too close to
motor cable. Motor cable and encoder cable
channels should be separate. Minimum distance
between cables should be at least 10cm.
6- Encoder may be grounded at both the motor
side and inverter side. If the encoder is grounded
at motor side, disconnect the grounding at inverter
side.
12 CONTACTOR
DROPPED
The main contactor(s) dropped
out while driver is running.
Check the supply circuit of the main contactors’
coils.
13 NO
CONTACTOR
SGN
No contactor picked up signal
is detected in 5 seconds after a
speed signal and direction
signal are detected.
Check the auxiliary contacts of the main
contactors in drive enable (EN) signal circuit.
14
LOW MOT.
CURRENT
No current can be delivered to
motor coils.
1- Motor wiring may not be connected properly.
Check broken or disconnected wiring.
2- Check the connection of main contactors.
15 WRONG
DIRECTION
Lift is not running in required
direction. Running direction
read from encoder is different
from the direction inverter
commands.
1- U, V, W phases of motor reversed. Check
motor connection.
2- Phase of encoder reversed.
16 UNBALLANCED
CUR.
Unballanced current at U, V,
W motor outputs. Over-
current at one or two of motor
outputs.
1- Contacts of main contactor may not conduct.
Check the connection of main contactors.
2- A faulty motor windings.