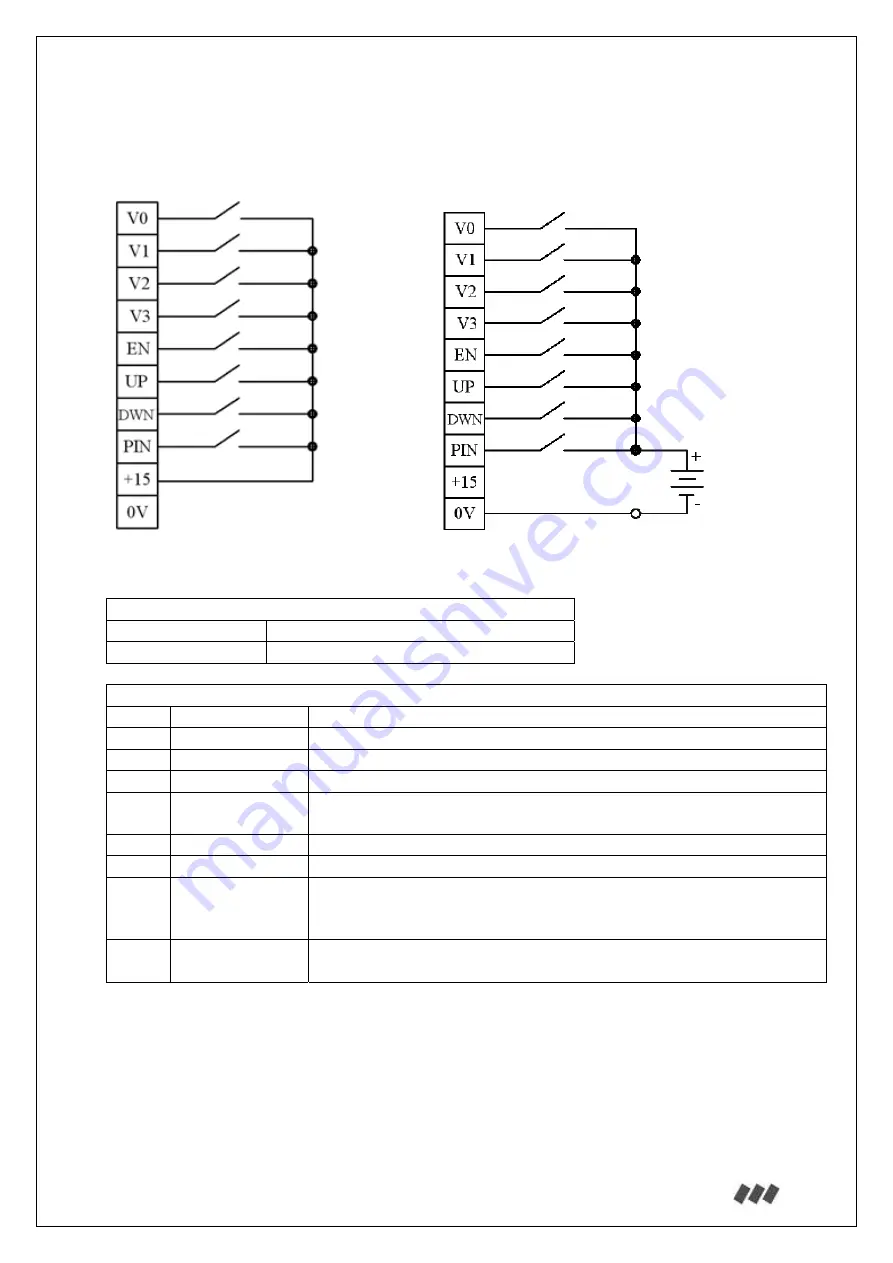
ARKEL Elektrik Elektronik Ltd.
Ş
ti. www.arkel.com.tr
08.2012
ADrive
22
13.2. CONTROL TERMINAL CONNECTIONS
13.2.1. Drive command inputs:
Digital input specifications:
Max. voltage
26Vdc
Clamping range
Maks. 2,5 mm
2
Drive command input terminals:
V0 Speed-0
Low
speed
V1 Speed-1
Inspection
speed
V2
Speed 2
Intermediate speed
V3 Speed-3
High
speed
EN
ENABLE
Drive enable (Must be switched by the open contacts of KPA and
KPB main contactors)
UP
UP
Travel direction up
DWN DOWN
Travel direction down
PIN Programmable
input
Programmable digital input.
Can be assigned as “Error Reset”, “Check Fout<Flim”, “ApRe
monitoring input” or “Brake monitoring input” in the menu.
+15 +15V
reference
voltage
Reference voltage for digital inputs (Imax: 100 mA)
In a case of more than one speed inputs applied the higher one is activated.
If the speed control inputs are driven by relay contacts, high speed and low speed signal should
be applied together. Otherwise, because of the relay contact delay, wrong speed inputs may be
perceived at speed changes especially for distance controlled stops it is important that there
must be no delays at speed transitions.
Re-levelling speed (VL) is active when V1 and V2 inputs are ON at the same time. V0 is don't
care (X). V3 shall be OFF.
a) Connection with internal power supply
b) Connection with external power
15Vdc, max. 100mA
internal supply
12-24Vdc,
min. 100mA
external supply