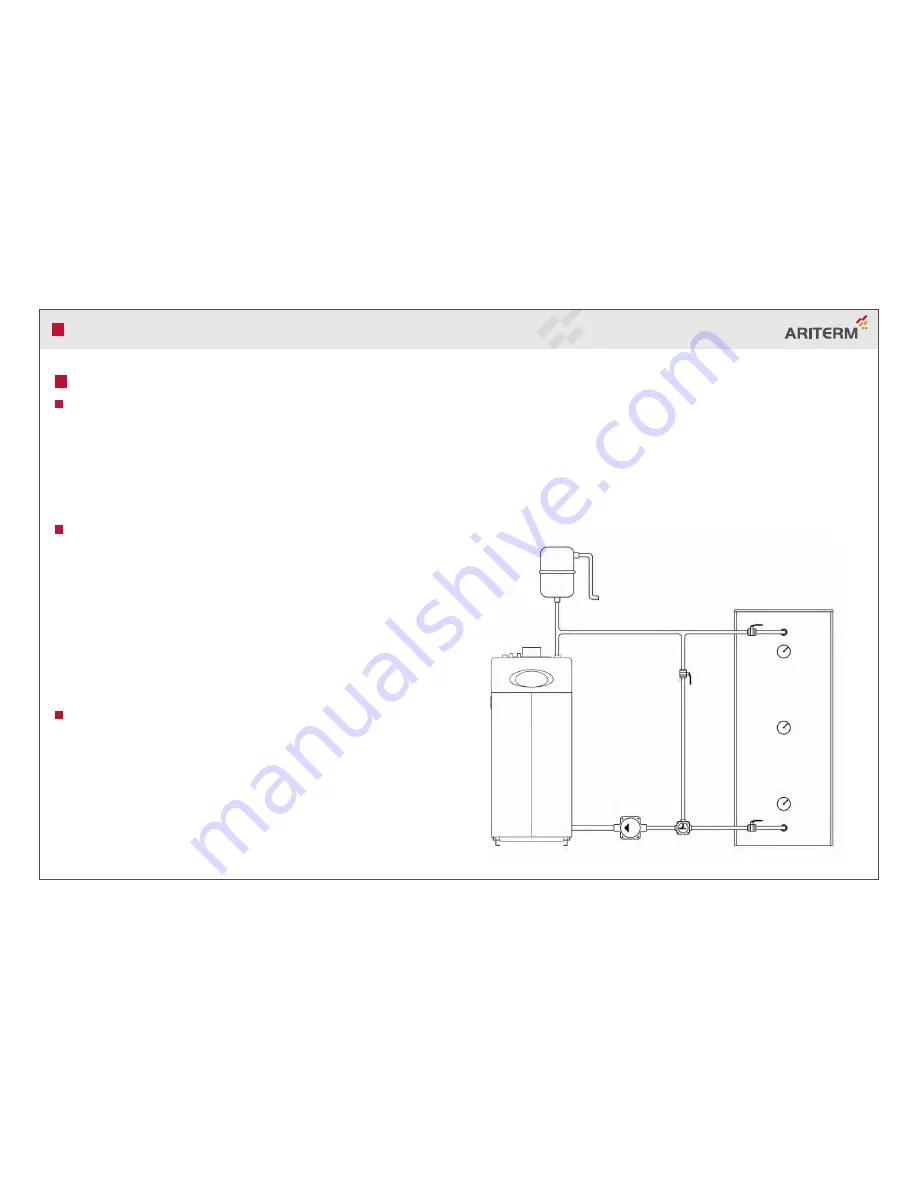
PELLET BOILER UNO
ARITERM SWEDEN AB
Installation Instructions -
2008.05.21 - 16/28
ACCUMULATOR
Heating to an accumulator tank
It might be advantageous to connect an accumulator tank to the boiler as this often
prolongs the burner’s operational times and improves the annual average efficiency.
With an UNO boiler it will not be economical to install a new accumulator tank as
the profit will probably not pay the investment thanks to the boiler’s extremely high
efficiency. An accumulator tank is, however, needed if the boiler is to be combined
with a solar energy system.
Installation of boiler with accumulator tank
If water heater or shunt valve is placed in the boiler, the burner will always be
controlled by the boiler temperature. The temperature sensor that is mounted in the
boiler will then be used. If the boiler and the accumulator tank have direct circula-
tion (the boiler heats the tank, which delivers hot water and warm tap water), the
boiler temperature should not be below 60˚C when the burner starts to avoid con-
densation and corrosion in the boiler. A thermostat controlled loading circuit should
therefore always be included in the system, see sketch below.
When water heater and shunt valve are placed in the accumualtor tank, the temper-
ature sensor can alternatively be placed on the tank to achieve longer operational
time as there will be less stops and starts.
Tank-mounted temperature sensor
If the burner’s temperature sensor will be placed on the tank there must be a load-
ing circuit with sufficient capacity to cool down the boiler. The boiler temperature
may not exceed 95˚C before the tank has reached the set temperature
(80˚C is recommended) and the burner is switched off.
The temperature sensor may not be placed to low on the tank as it then will be
more difficult for the loading circuit to cool down the boiler sufficiently.
If there is some doubt, mount the temperature sensor on the tank and test as
follows: heat the boiler and the tank until the boiler temperature reaches 95˚C,
check the temperature in the tank. This simple test will give an idea of where the
sensor should be placed and of the suitability to place it on the tank.
A specific accumulator control device is available as option.
Содержание KMP Uno
Страница 1: ...INSTALLATION and MAINTENANCE UNO ...
Страница 22: ...PELLET BOILER UNO ARITERM SWEDEN AB Installation Instructions 2008 05 21 22 28 ...
Страница 24: ...PELLET BOILER UNO ARITERM SWEDEN AB Installation Instructions 2008 05 21 24 28 ...
Страница 26: ...PELLET BOILER UNO ARITERM SWEDEN AB Installation Instructions 2008 05 21 26 28 ...
Страница 27: ...PELLET BOILER UNO ARITERM SWEDEN AB Installation Instructions 2008 05 21 27 28 ...