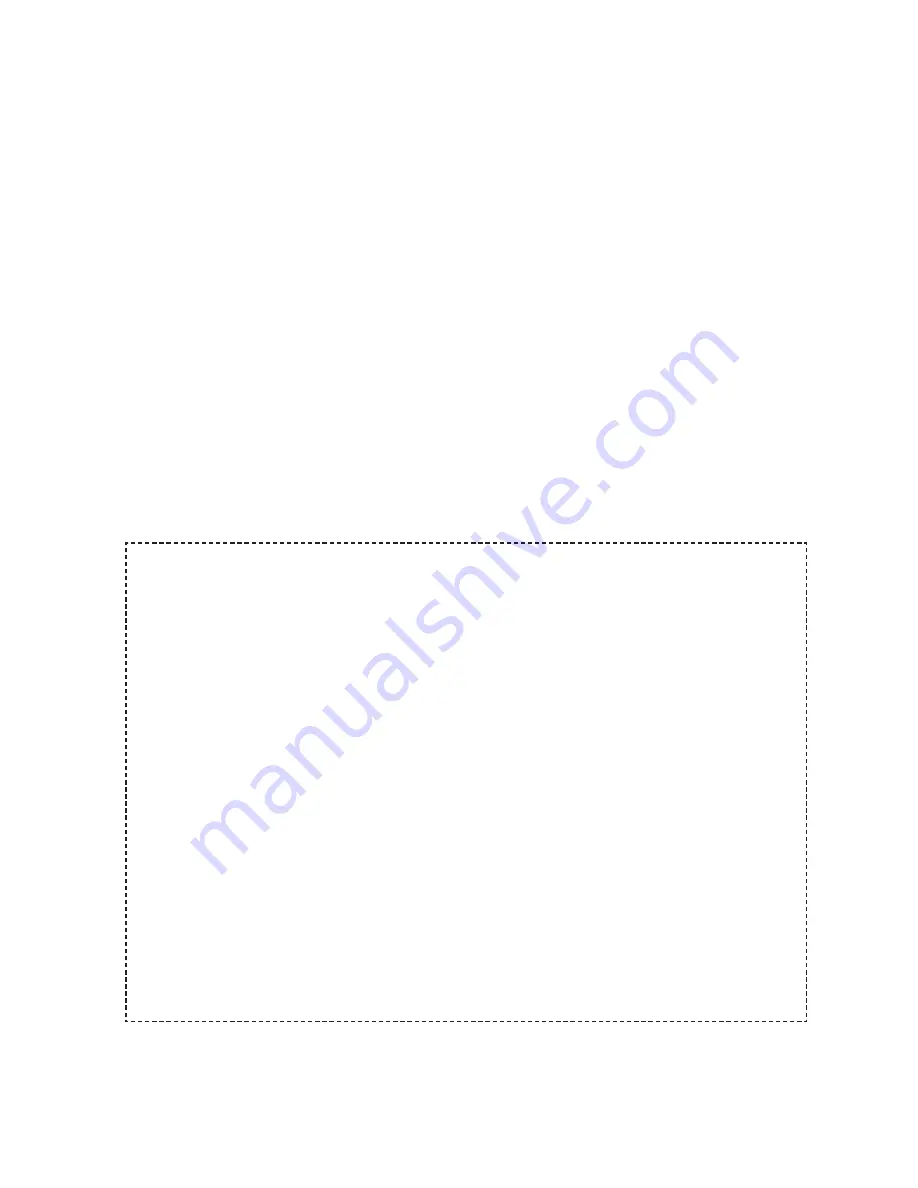
63
Please read these terms and conditions which are in
addition to any terms and conditions detailed in this book
or any registration card supplied with your appliance.
A charge will be made to the owner of the appliance if:
∑
The reason for any service visit is as a direct result
of a failure to install the appliance in accordance
with the manufacturer’s instructions.
∑
Your installer does not complete the necessary
commissioning process and procedure as detailed in
the Installation and Operating Instructions.
∑
Your appliance is not serviced on or before the 12
month anniversary of installation - this only applies to
appliances with a 2 and 5 year guarantee.
∑
Our service engineer calls as requested and the
failure is a non-manufacturing defect.
Failure to pay an invoice for any such occurence will be
assumed by MTS that you accept that your appliance
has not been installed correctly and understand that any
manufacturer’s guarantee has been withdrawn.
On the 12 month anniversary of the appliance
installation, you must have it serviced to continue any
guarantee offered into the following year. Failure to do
so will invalidate your guarantee and should an MTS
engineer be required to attend and no proof of service
documentation is made available, then MTS will charge.
As part of the commissioning process, it is a legal
requirement to register all boiler installations or
replacements with CORGI. Upon registration a
“Certification Number” will be issued followed by a
“Declaration of Safety” Certificate. MTS (GB) Ltd cannot
be called upon to carry out any work under the
manufacturer’s guarantee without proof of registration.
The registration number must be quoted when
requesting a service visit, and the “Declaration of Safety”
Certficate subsequently shown to the service engineer.
If the certificate is not made available, the engineer will
not work on the appliance and a wasted call charge will
be made.
T
ERMS AND
C
ONDITIONS OF
G
UARANTEE
If you have a problem with commissioning on installation, please contact our
Technical Department on 0870 241 8180
Plea
se r
emo
ve t
he c
omp
lete
d bo
iler
com
miss
ionin
g ch
eckl
ist s
tick
er f
rom
the
fron
t of
the
boi
ler
and
plac
e in
thi
s bo
x
for
cust
ome
r re
fere
nce
Содержание Benchmark System A 24 RFF
Страница 18: ...18 1 2 A A Fig 13 Fig 15 Fig 12 11 Installing the Boiler continued Fig 14 P P ...
Страница 21: ...21 Fig 20 Fig 21 Fig 22 162 ...
Страница 30: ...30 WIRING DIAGRAM FOR CONNECTION TO AN OPEN VENTED CYLINDER DIAGRAM B ...
Страница 31: ...31 WIRING DIAGRAM FOR CONNECTION TO AN MTS UNVENTED CYLINDER DIAGRAM A ...
Страница 60: ...60 ...