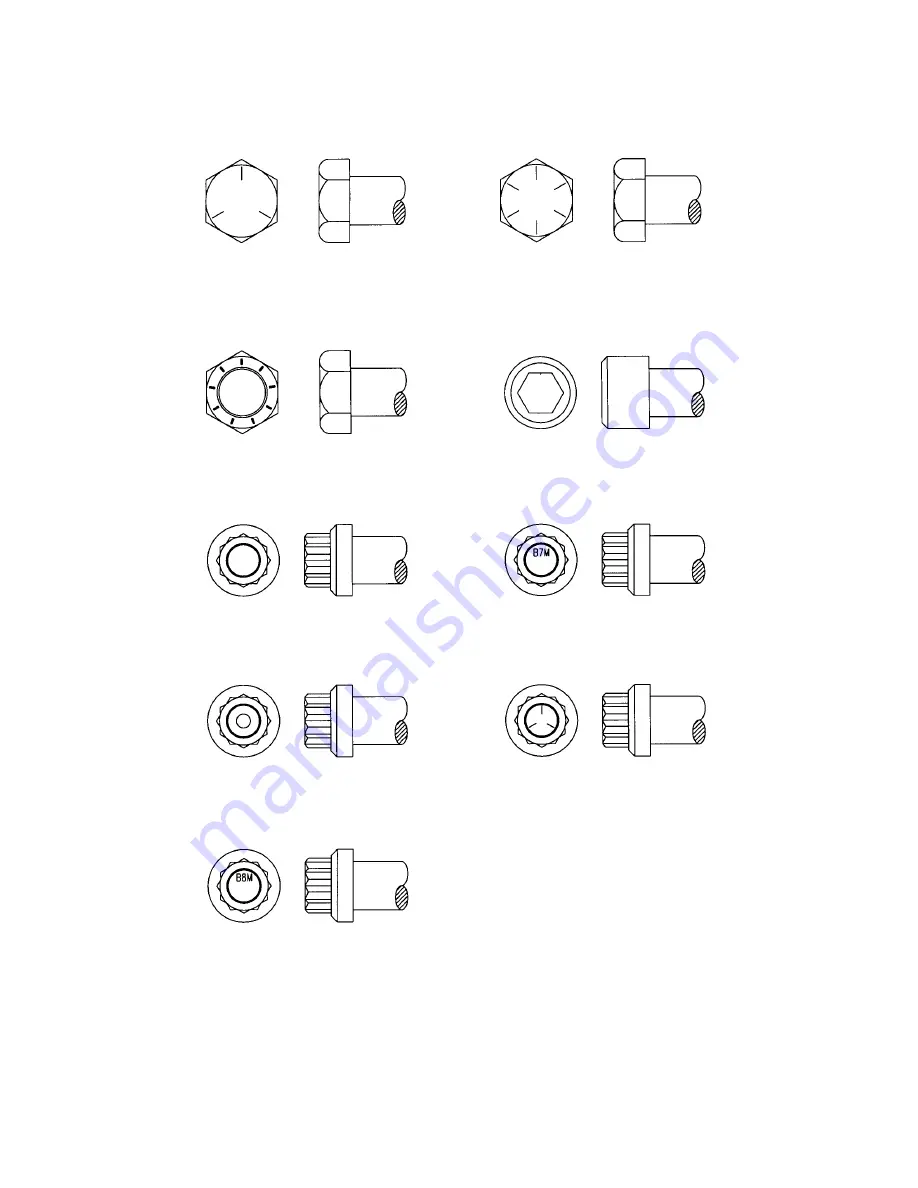
F
OR
M
ODELS
: JGW, JGR
AND
JGJ
S
ECTION
1 - D
ESIGN
S
PECIFICATIONS
& D
ATA
PAGE 1 - 22
1/01
F
IGURE
1-13: B
OLT
I
DENTIFICATION
Hex Socket Head Grade 8
Hex head Grade 8
Hex head Grade 9
Hex head Grade 5
12 Point Grade 8
12 Point Grade B7M (NACE)
12 Point Interim
Grade 5
12 Point Grade 5
12 Point Stainless
Steel Grade B8M
Содержание JGJ Series
Страница 23: ...FOR MODELS JGW JGR AND JGJ SECTION 1 DESIGN SPECIFICATIONS DATA 1 01 PAGE 1 17 FIGURE 1 8 DOG POINT STUDS STUD ...
Страница 30: ...FOR MODELS JGW JGR AND JGJ SECTION 1 DESIGN SPECIFICATIONS DATA PAGE 1 24 1 01 NOTES ...
Страница 34: ...FOR MODELS JGW JGR AND JGJ SECTION 2 INSTALLATION PAGE 2 4 1 01 NOTES ...
Страница 44: ...FOR MODELS JGW JGR AND JGJ SECTION 3 START UP PAGE 3 10 1 01 NOTES ...
Страница 114: ...FOR MODELS JGW JGR AND JGJ SECTION 5 MAINTENANCE PAGE 5 42 1 01 NOTES ...
Страница 120: ...FOR MODELS JGW JGR AND JGJ SECTION 6 TECHNICAL ASSISTANCE PAGE 6 6 1 01 NOTES ...
Страница 130: ...FOR MODELS JGW JGR AND JGJ SECTION 7 APPENDICES PAGE 7 10 1 01 NOTES ...
Страница 135: ......
Страница 136: ......
Страница 137: ......
Страница 138: ......
Страница 139: ......
Страница 140: ......
Страница 141: ......