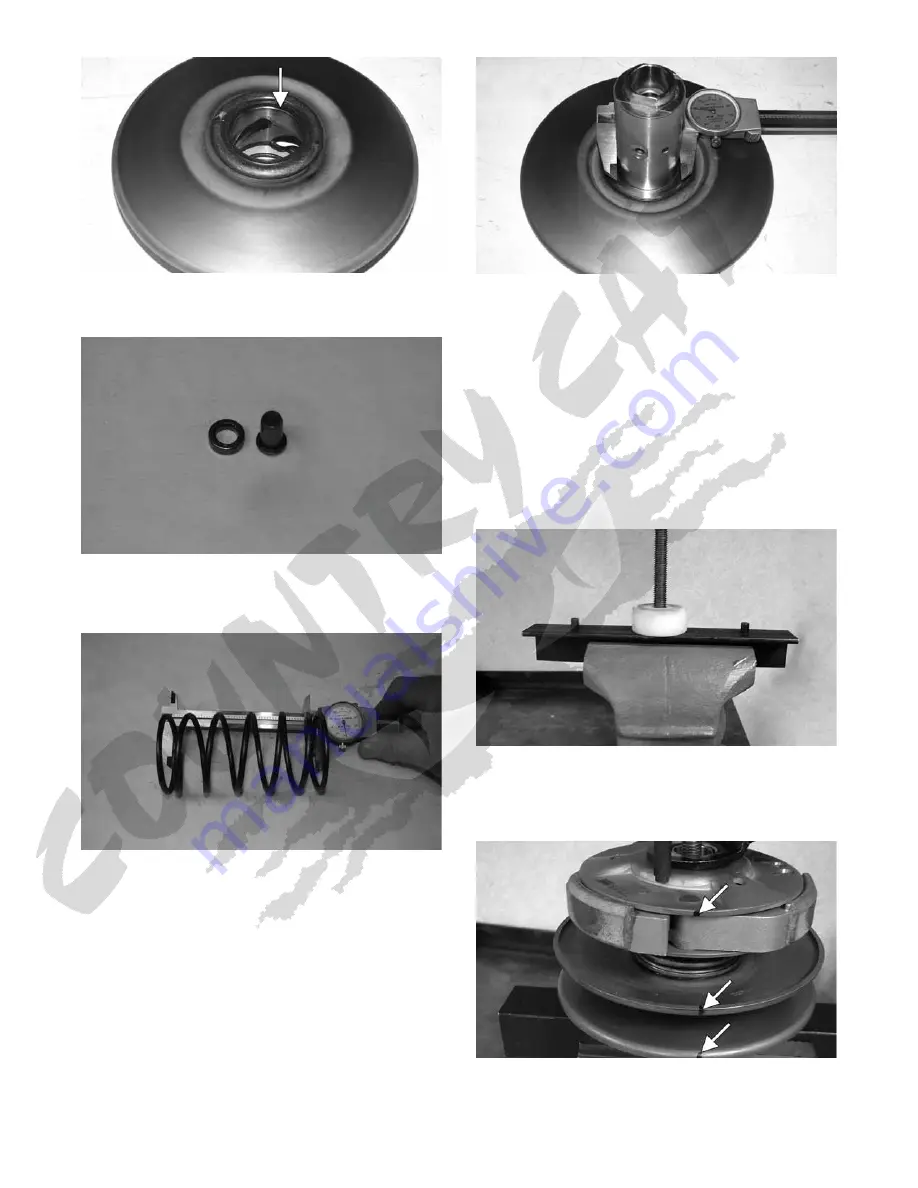
49
KM382A
4. Inspect the pins and bushings for wear, flat spots,
looseness, or cracking.
KM379
5. Measure the driven face spring free length. If the free
length is less than 131 mm, the spring must be
replaced.
KM376
6. Measure the driven fixed face hub using a calipers.
The minimum service limit is 39.93 mm.
KM378
7. Measure the thickness of the centrifugal clutch shoe
lining. The minimum service limit for the lining is
0.5 mm.
NOTE: If any shoe lining is below the service limit,
the complete set must be replaced.
Assembling
1. Place the fixed face of the driven pulley on the pulley
compressor base.
NOTE: Make sure the spacer is on the base or dam-
age to the fixed face will occur when the spring is
compressed.
KX571
2. Apply multi-purpose grease to the O-rings and
grease seals on the movable face; then install on the
fixed face making sure the alignment marks are
properly aligned.
KM374A
3. Install the pins and spacers into the fixed face hub;
then pack the cam slots in the movable face with
multi-purpose grease.
Содержание 300 Utility
Страница 1: ...300 UTILITY DVX 300 ATV SERVICE MANUAL 2014 ...
Страница 3: ......
Страница 118: ...Printed in U S A Trademarks of Arctic Cat Inc Thief River Falls MN 56701 p n 2259 825 ...