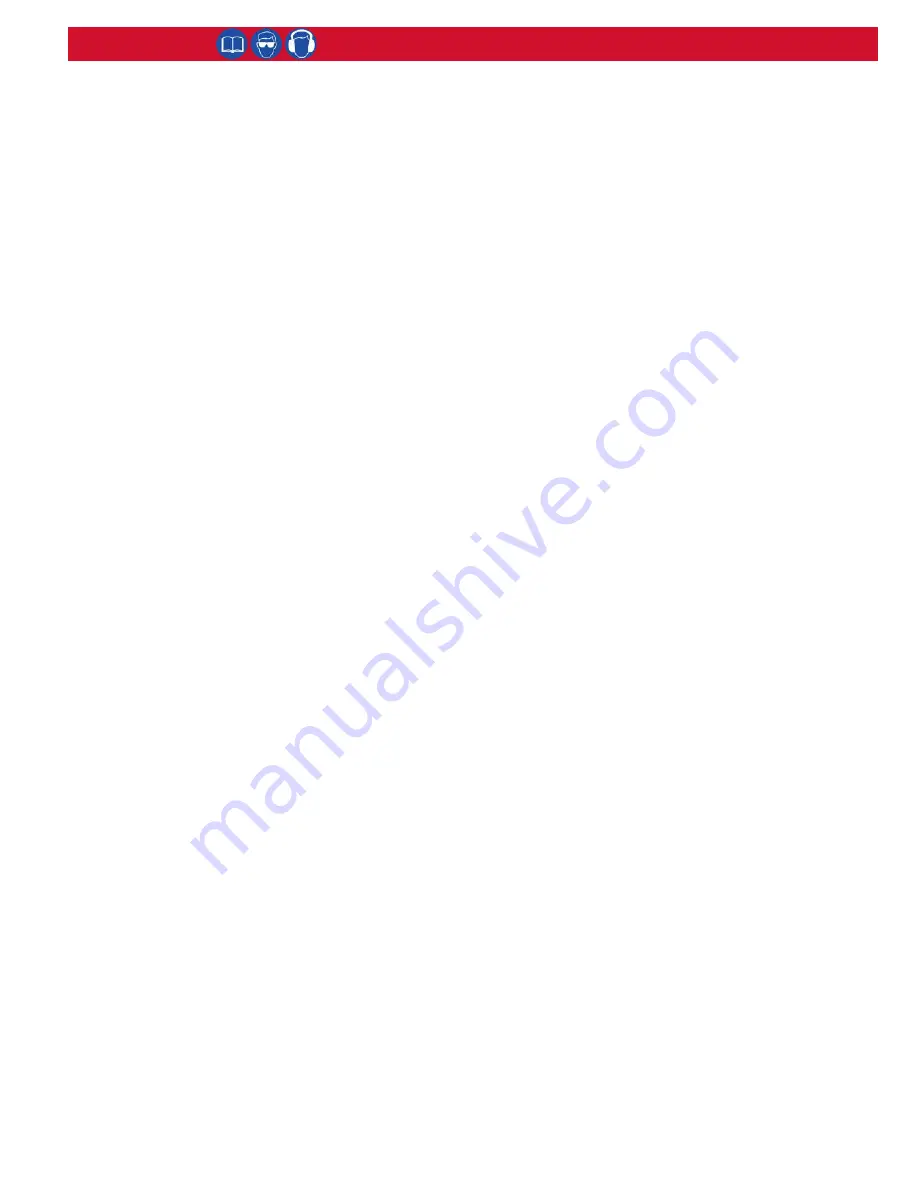
11
940 Powerig®
(HK496)
Troubleshooting
1. Motor fails when tool switch is depressed:
(a) Loose or defective control cord or connectors.
(b) Power source not properly fused.
(c) Defective tool switch.
(d) Loose wire(s).
(e) Defective relay.
(f) Incorrect power source.
(g) Defective motor contactor.
(h) Defective transformer
2. Motor runs, but tool will not reciprocate:
(a) Hoses not coupled properly.
(b) Hydraulic fluid viscosity not proper or level is low.
(c) Defective pilot valve solenoid or coil.
(d) Unloading valve missing in tool.
(e) Bind in tool or nose assembly.
(f) Defective directional valve.
(g) Pump to motor coupling damaged.
3. Pintail of fastener fails to break off:
(a) PULL pressure set too low.
(b) Worn or defective hose couplers.
(c) Hydraulic fluid viscosity not proper or level is low.
(d) Hydraulic fluid overheated.
(e) Worn or defective directional valve.
(f) Internal relief valve set too low or defective.
(g) Worn or defective pump.
4. Tool will not return when switch is released. (Tool will
not push nose assembly off swaged fastener.):
(a) RETURN pressure set too low.
(b) Hoses not coupled properly.
(c) Worn or defective solenoid.
(d) Worn or defective pilot valve.
5. Motor fails to shut-off when installation cycle is
completed:
(a) RETURN pressure switch set too high.
(b) Hydraulic fluid viscosity not proper or level is low.
(c) Hydraulic fluid overheated.
(d) Defective limit switch in pressure switch assembly.
6. Pump making noise throughout entire cycle:
(a) Pump is cavitating-fluid level may be low or fluid
viscosity too heavy.
(b) Strainer is dirty and clogged.
7. Tool operation slow; Entire cycle does occur:
(a) Pump is cavitating-fluid level may be low or fluid
viscosity is too heavy.
(b) Strainer is dirty and clogged.
(c) Worn or defective directional valve.
(d) Worn or damaged pump.
(e) Worn or defective hydraulic couplers.
Always check the simplest possible cause of malfunction first. For example, blown fuse, tripped circuit breaker,
defective switch or control cord. Eliminate each possible cause until the defective circuit or part is located. Where
possible, substitute known good parts for suspected bad parts. A qualified electrician should check out the
electrical system. Use this section as an aid in locating trouble and correcting it.
OPTIONS
940T-1
(Special Version of 940)
The 940T-1 is part of Huck’s revised aftermarket Truck
Kits, which contain different pressure installation tools.
This hydraulic unit will be shipped from the factory with
output pressures set as follows:
PULL: 5700-5800 psi
RETURN: 4400-4600 psi
ACCESSORIES:
Auxiliary Switch and Control Cord 113056
An auxiliary switch is available for use when checking and
adjusting pressures and when troubleshooting.
Gauge T-124833CE
A “T” gauge is available for use when checking and
adjusting pressures, and troubleshooting.
Hose and Control Cord Kits
of various lengths
Please contact your HUCK representative.
Directional Valve Kit 129437
Includes seals necessary to service Directional Valve
103596.
Rig Transport Dolly 129703
Heavy duty steel dolly for easy movement of powerig
throughout the work area.
Motor 111346
Motor and Pump Assembly 111345
Motor Service Kit 115770
includes:
Motor Brushes Set 111415
115V Armature
115764
Upper Bearing
115766
Lower Bearing
115767
115V Motor Field
115768
Brush Holder
115784
Brush Holder Cap 115785
Gasket
115786
Options & Accessories