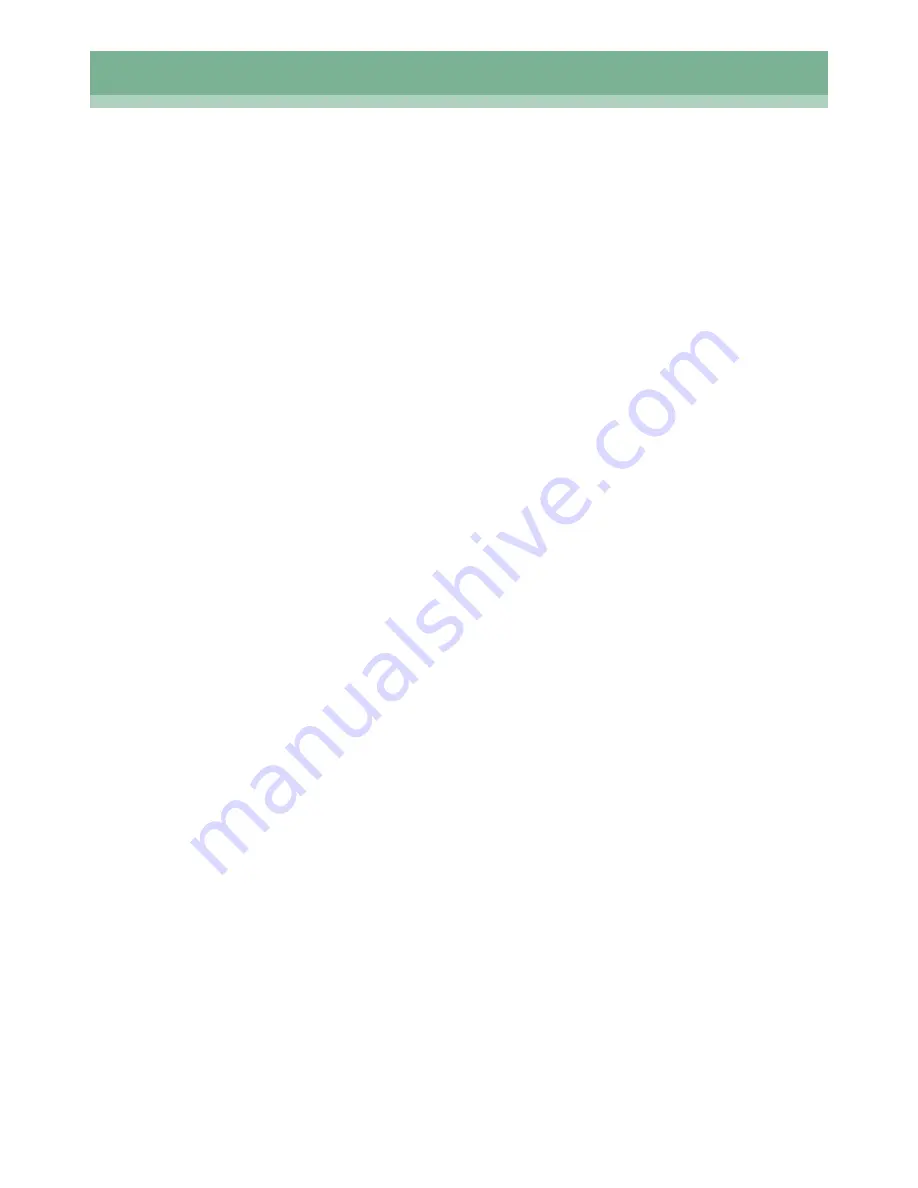
Page 5
INSTALLATION & FITTING
COMMERCIAL STEAM GENERATORS
BJ6-12AkW & BJ18-24AkW
BJ6-12BkW & BJ18-24BkW
NOTE: -
Before the installation of this machine, please make sure you read these instructions thoroughly Failure
to install this machine in accordance with the manufacturers recommendations might invalidate the warranty.
Should you have any queries or require technical advice, contact your distributor who will put you in contact
with our technical department. The electricity supply must only be connected to the unit by a suitably qualified
person in accordance with local regulations.
STAGE ONE: - Sighting and Fixing the Generator.
A minimum space of 1100mm for width and 1000mm for height should be allowed, with proper access for
servicing the generator and the descaling cap. (See detail 5 Fig 2) Determine a clean dry place where the steam
generator is to be fixed (emphasis on the surface being secure and the unit being properly supported). The unit
is not suitable for installation in a damp or wet area. Screw the generator to the wall, through screw holes (see
dimensions on Fig 2) Make sure the generator is both vertical and horizontally level. Allow 300mm minimum
height from the floor, to leave space for drainage of solids into a container. A minimum space of 400mm from
the cleaning access cap(s) (see Fig 2) from the unit should be permitted for cleaning with the brush provided.
Once the generator has been fixed, the anchor screw must be fitted to prevent the generator from being
accidentally moved. Should the generator be boxed in, an access door or panel must be fitted to allow for easy
access and maintenance of the generator unit without damaging the decoration, you should also make an
allowance for ventilation minimum 100mm x 100mm.
STAGE TWO: - Water Supply
Generally the water supplied from any regional water authority is of sufficient quality to use with the Aqua-
Steam generator. Greater care is perhaps required if water is from a well or bore hole particularly if the
iron content is high. Such water should be avoided. If requested the water authority will advise on the scale
content (hardness) of the water supplied. In situation where the water hardness is greater than 100 ppm it is
recommended that a monospheric water softener be incorporated to supply the generator especially if the
unit is to be in frequent use. Alternately inspect the unit for scale after every 100 hours of use and de-scale as
necessary – see descaling instructions. We recommend that a washing machine hose is fitted to the 3/4” BSP
male thread of the solenoid valve (detail 1 Fig 2) and connect the other end of the hose to a servicing valve so
the water supply can be isolated. The hose is also useful for flushing the tank and pipe work during maintenance
etc. A minimum water pressure of 0.5 bar and maximum 10.0 bar must be provided for the correct operation of
this machine.
STAGE THREE: - Fitting Steam Outlet
The maximum pipe run must not exceed 20 Mtrs length and must be of 22mm diameter. The pipe work should
be installed in such a way as not to create air locks. Long radius bends should be used or pulled bends to reduce
restriction of steam. The pipe must be adequately lagged to avoid heat loss and condensation of steam. The BJ
18-24 generator has two independent steam outlets; each must be fitted as above but totally independent from
each other. When pipe is increased over 10 Metres a higher power setting may be necessary. It is bad practice
and a frequent source of failure to inject essence into the steam pipe(s). Even in very large diameter pipes the
fillers and plasticisers used in the essence quickly block the pipe and also back up into the generator.
STAGE FOUR: - Auto-flushing
Connection to the discharge solenoid valve is 1/2” BSP thread and the drain line must be a minimum of 15mm
diameter heat resistant pipe and must have a minimum fall of 1.5 degrees to an open drain, washing machine
trap or similar. Keep the pipe run short with as few bends as possible as it will otherwise fill with scale.
STAGE Five: - In the Cubicle
Fit either the BKW temperature sensor or the AKW cubicle control. The BKW sensor should be fitted
approximately 2Mtrs above the floor away from the steam outlet in a safe position. The AKW cubicle control if
fitted should be approx l.8mtrs above the floor away from the steam outlet. We recommend that shower type
silicone sealant be used around the stainless steel trim and box assembly of the cubicle control to fix the unit to
the wall. Connect plug on lower right hand of attendant control box.