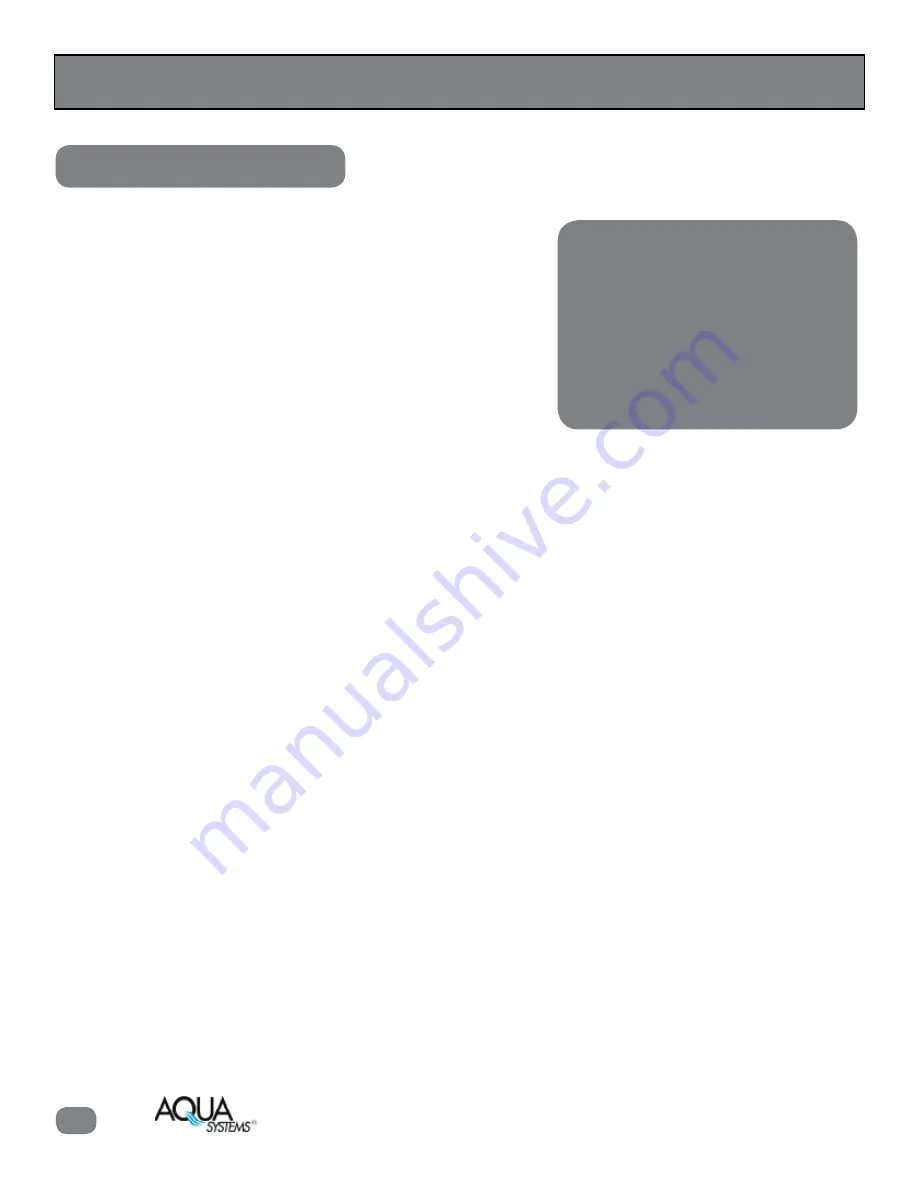
© 2014 New Aqua LLC dba Aqua Systems • 7785 East US Hwy 36 • Avon, IN 46123
30
Eradicator II AIF Systems
Installation, Operation,and
Maintenance Manual
Excessive force can break the notches molded into the drive back plate.
Make certain that the main drive gear still turns freely. The exact position
of the piston is not important as long as the main drive gear turns freely.
Reattach the drive assembly to the control valve and connect all plugs.
After completing any valve maintenance, press and hold NEXT and REGEN buttons for 3 seconds or unplug power
source jack (black wire) and plug back in. This resets the electronics and establishes the service piston position. The
display should flash all wording, then flash the soft ware version (e.g. 154) and then reset the valve to the service posi
-
tion.
Service Guide
Excessive force can break the
notches molded into the drive
back plate. Make certain that
the main drive gear still turns
freely. The exact position of the
piston is not important as long as
the main drive gear turns freely.
Tip:
Reattach the main piston to the drive cap assembly. Reattach the regen
-
erant piston (if needed) to the main piston. Do not lubricate the piston
rod, main piston or regenerant piston. Lubricant will adversely affect
the red or clear lip seals. Reinsert the drive cap assembly and piston
into the spacer stack assembly and hand tighten the drive cap assem-
bly. Continue to tighten the drive cap assembly using a screwdriver as a
ratchet until the black o-ring on the spacer stack assembly is no longer
visible through the drain port.
Spacer Stack Assembly
To access the spacer stack assembly remove the drive assembly, drive cap assembly and piston. The spacer stack as
-
sembly can be removed easily without tools by using thumb and forefinger. Inspect the black o-rings and red or clear lip
seals for wear or damage. Replace the entire stack if necessary. The spacer stack assembly has been 100% tested at
the factory to insure proper orientation of one way seals. Do not disassemble the stack.
The spacer stack assembly may be chemically cleaned (dilute sodium bisulfite or vinegar) or wiped with a soft cloth.
The spacer stack assembly can be pushed in to the control valve body bore by hand. Since the spacer stack assembly
can be compressed it is easier to use a blunt object (5/8” to 1-1/8” in diameter) to push the center of the assembly into
the control valve body. The assembly is properly seated when at least four threads are exposed (approximately 5/8”).
Do not force the spacer stack assembly in. The control valve body bore interior can be lubricated with silicone to allow
for easy insertion of the entire stack. Do not use silicone or any other type of lubricant on the red or clear lip seals or the
piston.
Reattach the drive cap assembly and piston(s) and the drive assembly.
After completing any valve maintenance, press and hold NEXT and REGEN buttons for 3 seconds or unplug power
source jack (black wire) and plug back in. This resets the electronics and establishes the service piston position. The
display should flash all wording, then flash the soft ware version (e.g. 154) and then reset the valve to the service posi
-
tion.
Содержание Eradicator II AIF
Страница 40: ...2014 New Aqua LLC 2 2014 Rev 1...