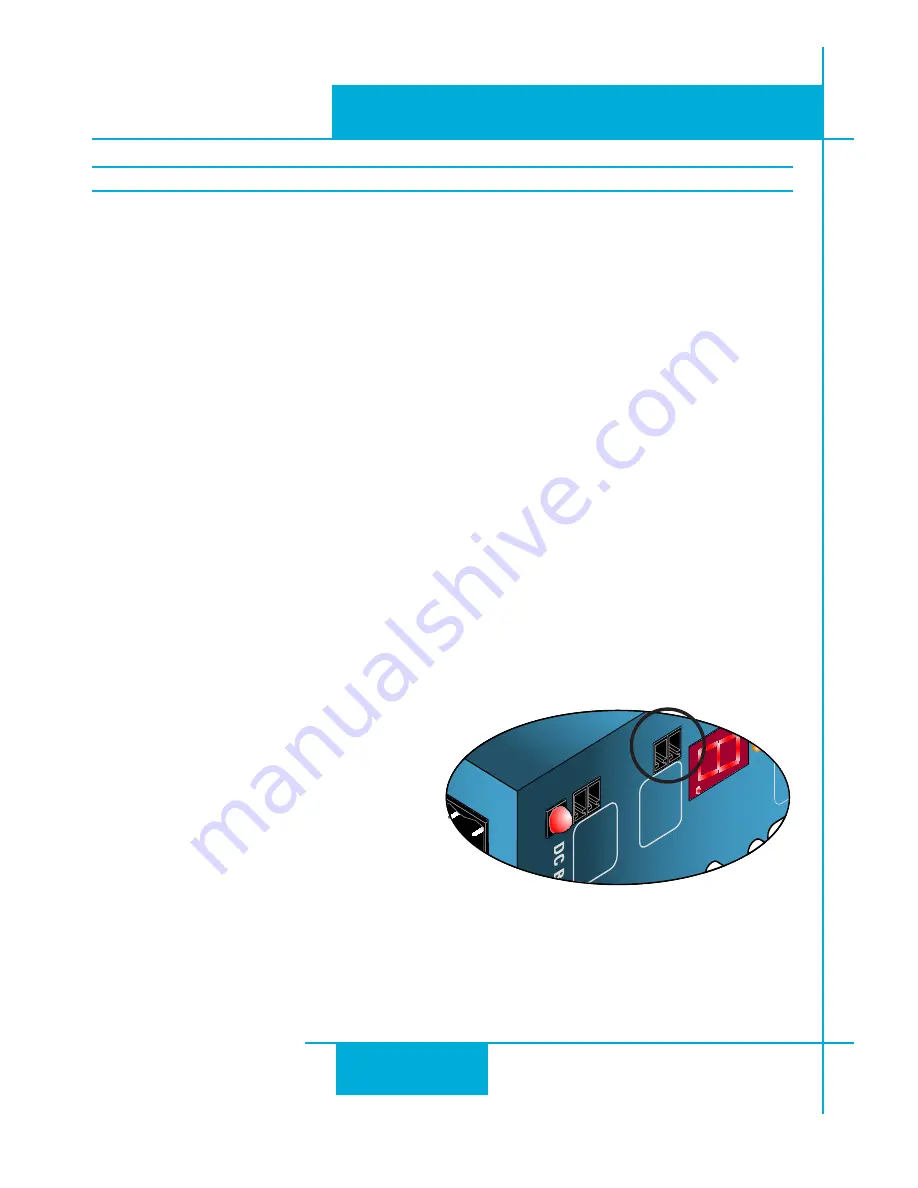
14
BLuAC5 S/Q Hardware manual
920-0049 Rev. C
12/8/2014
Connecting the AC Power Input
The AC supply to the drive can range for 90VAC RMS to 260VAC RMS, 50 to 60 Hz, single or
three phase.
The AC input voltage is the most significant attribute of the AC input to affect the power that is
available from the drive. At lower AC inputs the DC bus voltage is reduced and therefore will
limit performance of higher voltage AC servo motors. As a general rule AC inputs of 120VAC
will permit continuous operation of 500 Watt servo motors wile AC inputs of 240VAC will oper-
ated 1K Watt servo motors. It is wise to match as closely as possible the AC input and the
Servo Motor voltage rating.
AMP has a number of servo motors designed to operate at both 120 and 240VAC input (See
Recommended Motors
later in this manual.)
When available three phase input is recommended for it’s lower ripple on the DC bus voltage.
This saves wear and tear on the DC bus capacitors and spreads out the current on the AC
input rectifiers.
WARNING: Exceeding the DC Bus voltage of 367VDC may cause the internal regenera-
tion circuitry to activate. This may result in a drive fault or some cases can result in
drive failure.
24 Volt Controller Input (Keep Alive)
The BLUAC5 servo drives offer a 24 volt
input that will supply “Keep Alive” power to
the controller section of the drive. AC power
can be removed without shutting down the
servo controller. This function can be used to
maintain motor position information. When AC
power is restored to the drive the servo motor
can be re-enable and the original position
reestablished.
When 24 volt input is present and the AC
input is removed the drive will display a “U”
error code.
Status
Regen
GND
+24VDC
Input
User Out
+24VDC
GND