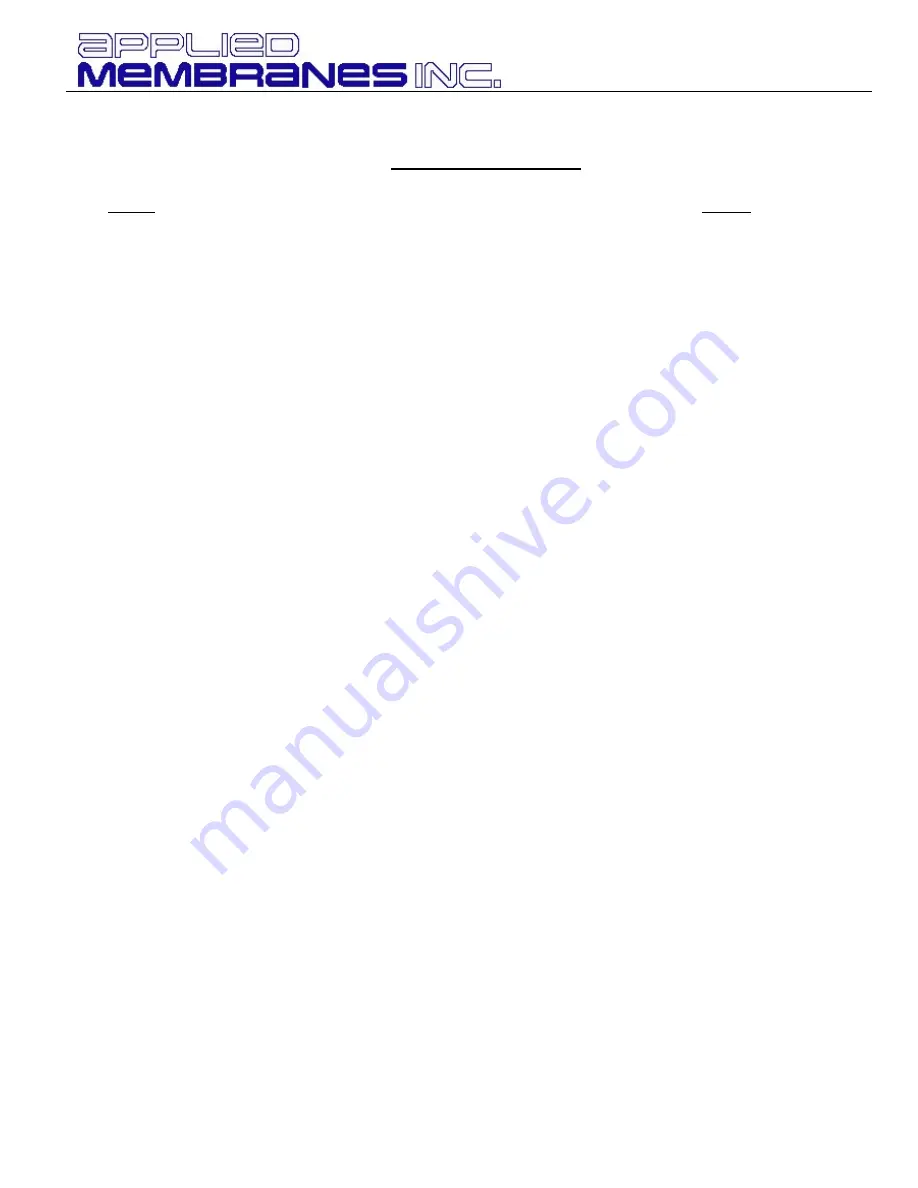
AA System Operation Manual
Page
1
of 27
© 2007
TABLE OF CONTENTS
ITEM
PAGE
Record
Sheet
. . . . . . 2
General
Information
and
Safety
. . . . . . 3
System
Specifications . . . . . . 4
System
Operating
Conditions . . . . . . 5
System
Flow
Schematic
. . . . . . 6
Component
Identification
. . . . . . 7
System
Installation
. . . . . . 8-9
Initial
System
Start-Up
. . . . . . 10
Shut
Down
. . . . . . 11
Adjustment
of
Pressure
Switches
. . . . . . 12
Maintenance
Tips
. . . . . . 13
Cleaning
.
.
.
.
. .
14-18
Replacing
Membranes . . . . . . 19
Replacing
Pre-filters
. . . . . . 20
Temperature
Correction
. . . . . . 21
Operating
Do’s
and
Don’ts
. . . . . . 22
System
Operating
Log . . . . . . 23
Troubleshooting
. . . . . . 24
Electrical
Drawing
. . . . . . 25
Component
Identification
. . . . . . 26
Warranty
. . . . . . 27
Содержание AA Series
Страница 7: ...AA System Operation Manual Page 6 of 27 2007 ...
Страница 26: ...AA System Operation Manual Page 25 of 27 2007 ...