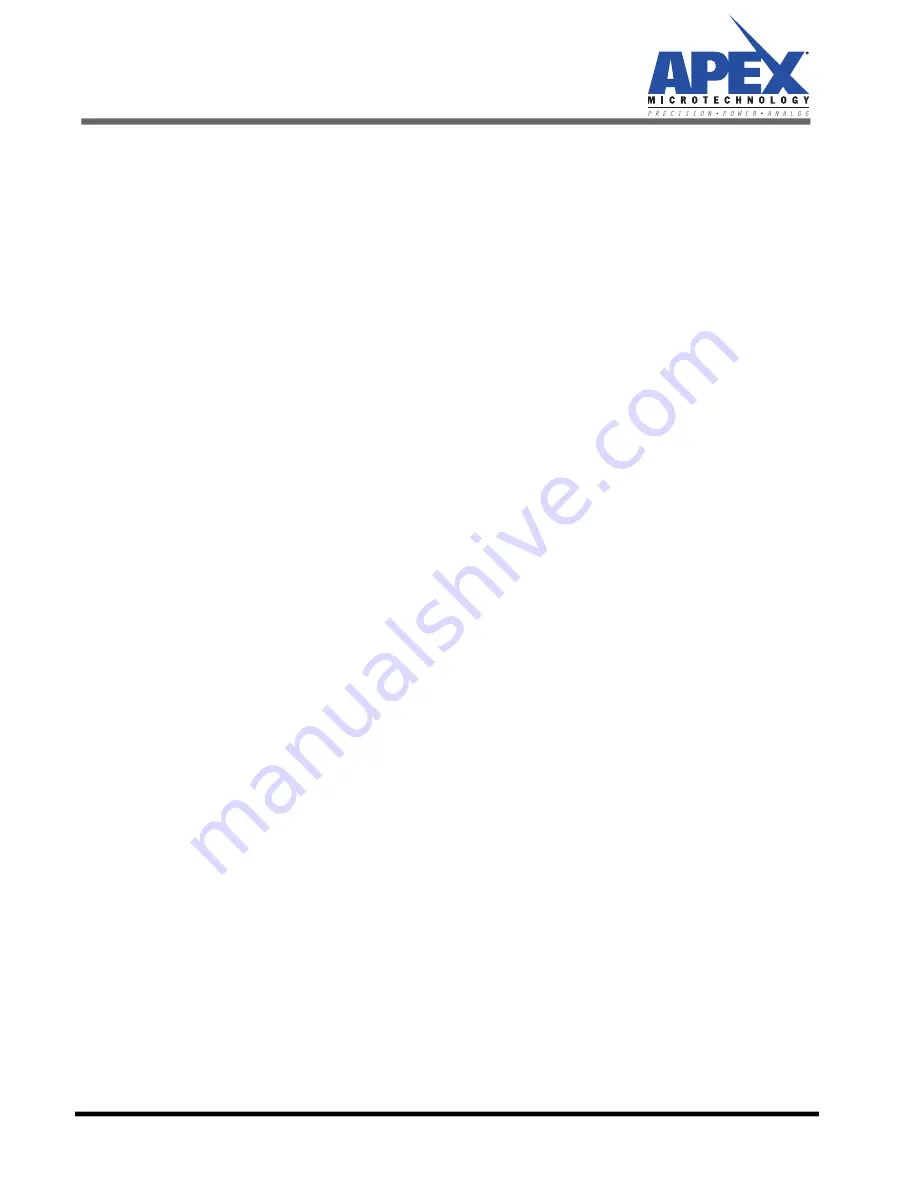
EK76
6
EK76U Rev A
14. Make sure all leads protruding out the DUT side are clipped to under 1/8 inch (3mm).
15. When installing the DUT-HS, start by temporarily fastening the central 2 holes to the board. Pass the #6-
32 x ¾" screws through the heatsink and place a nylon spacer on each. Carefully pass this assembly
through the matching holes on the PCB and fasten with #6-32 nuts on the component side.
16. Now, make a similar assembly at each corner of the heatsink. Pass the #6-32 x 5/8" screws through the
heatsink while holding a nylon spacer between the board and heatsink (pliers would be helpful). Fasten
with #6-32 nuts on the component side and tighten.
17. Undo the first two screws and nuts, but leave the nylon spacers sandwiched between the heatsink and
board.
18. Cut the Teflon tubing into ¼ inch (6mm) pieces and slide the pieces onto the pins of the DUT. This is an
added precaution to prevent the heatsink or thermal washer from shorting against the pins. One sleeve
on each of 4 corners of the DUT is sufficient. Do not cut Teflon longer than the recommended length, as
this will prevent proper seating of the DUT on the heatsink.
19. Place a single TW22 thermal washer over the heatsink area where the DUT will go. Place the DUT in this
space, so its pins pass through the TW22 and the heatsink slots. Rest the pins over the pin receptacles
from step 2. Engaging all 16 receptacles requires much force. Rather than applying this force by hand,
reinstall the #6-32 x ¾" screws and nuts, this time passing through the DUT tabs and TW22. With the #6-
32 nut on the component side, tighten the screws in small increments, switching frequently between the
two screws. Make sure the TW22 is loose and centered up until the final tightening, or else the metallic
foil can short out the DUT's pins.
20. Use the #8-32 x ¼" screws to mount a 2-inch standoff on each corner of the PCB.
HEATSINK GUIDELINES
Determining heatsink size for SA310 depends on several factors. Refer to SA310 datasheet for more infor
-
mation on calculating power dissipation, thermal resistance, and finding thermal ratings.
MOTOR CONTROL
P2 is designed to match the “remote amplifier” connector on Precision Motion Device's DK78113 devel
-
oper kit for the Juno Velocity & Torque Control IC. Follow the instructions in the DK78113 User Manual to
connect a remote amplifier. Applications requiring torque control will require the Current Sense gain and off
-
set circuit described below. Use default values when pairing with the Juno device.
Other motor control ICs may be used with EK76, but these may require different wiring and/or current
sense circuits.
Содержание EK76
Страница 8: ...EK76 8 EK76U Rev A Figure 2 Top View ...
Страница 9: ...EK76 EK76U Rev A 9 Figure 3 Bottom View ...