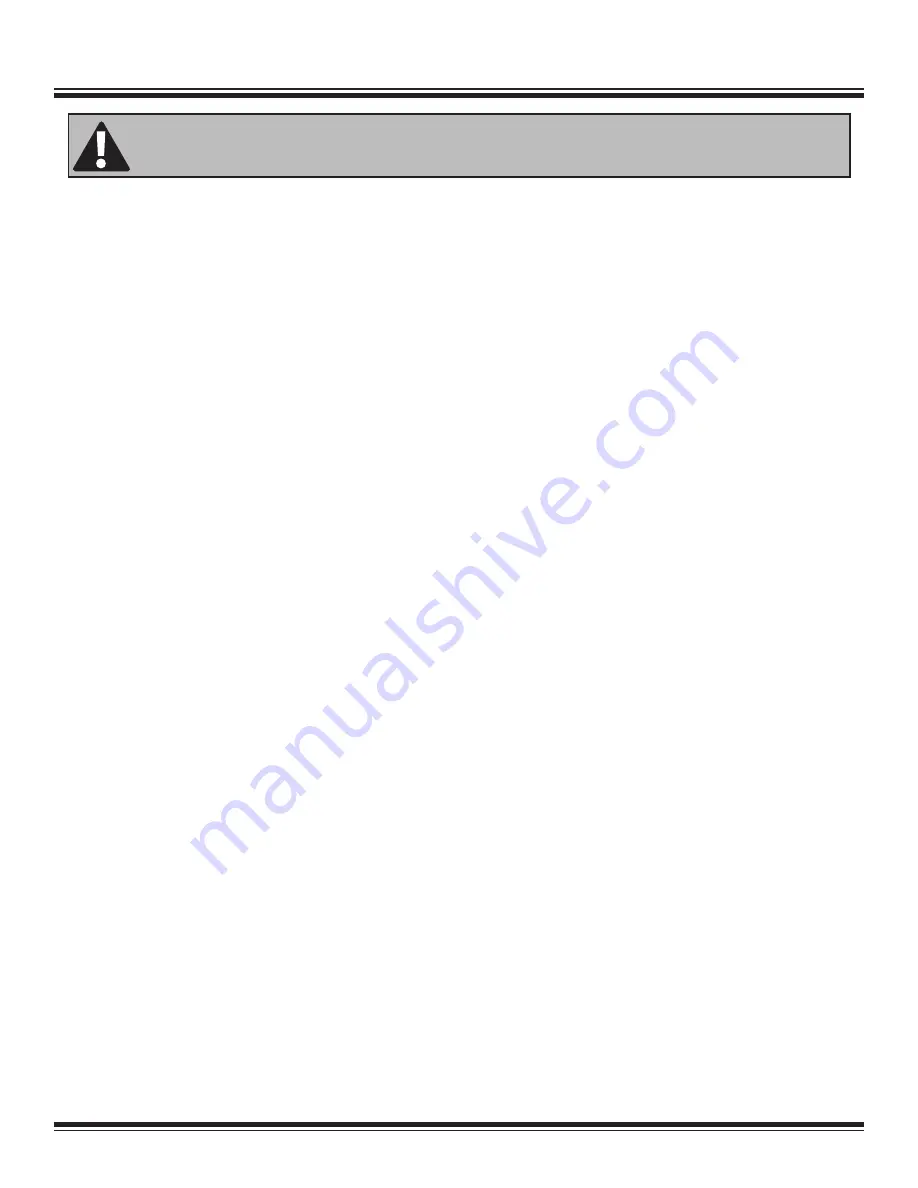
402306_A95_RevH
REMOVING THE BLAST WHEEL (FIGURE 1-2)
1. Remove feed spout (1) by pulling it out of the housing.
2. Loosen the control cage clamps (2).
3. Remove the control cage (3).
4. Remove the nuts (4) of the front plate (5) and remove the plate.
5. Fix the blast wheel (7) from rotating by pressing the shaft-locking button on motor (Figure 7).
6. Remove the blast wheel nut (6).
7. Remove the blast wheel (7).
8. Remove the wheel hub (8) and inspect for wear.
9. Inspect the seal (9) for wear.
INSTALLING THE BLAST WHEEL (FIGURE 1-2)
1. Replace seal (9) if it is worn.
2. Place wheel hub (8) on motor shaft making sure it is properly aligned and fully seated.
3. Place blast wheel (7) through the housing opening and onto the wheel hub (8) aligning with the pins of the hub. Spin wheel to ensure it is
properly seated on the pins and doesn’t wobble.
4. Clean threads of motor shaft and blast wheel nut (6) removing any shot.
5. Fix the blast wheel (7) from rotating by pressing the shaft-locking button on motor (Figure 7).
6. Tighten the blast wheel nut (6) to secure the blast wheel. Spin wheel to ensure it doesn’t wobble.
7. Reattach the front plate (5) with the nuts (4). Spin blast wheel to ensure it doesn’t wobble.
8. Install the control cage (3). Spin blast wheel and listen for any grinding noises.
9. Tighten the cage clamps (2) to secure the control cage (3). Make sure the blast wheel can rotate freely.
10. Install the feed spout (1).
11.
Adjust the control cage (3) to achieve an even blast pattern.
Maintenance
28
WARNING:
BEFORE PERFORMING MAINTENANCE, ALWAYS DISCONNECT THE MACHINE FROM POWER TO PREVENT ACCIDENTAL
STARTUP.
Содержание A95
Страница 3: ...Table of Contents 3 Labels 48 Wiring Diagrams 49 Handle 49 Blast Motor 50 402306_A95_RevH ...
Страница 51: ......