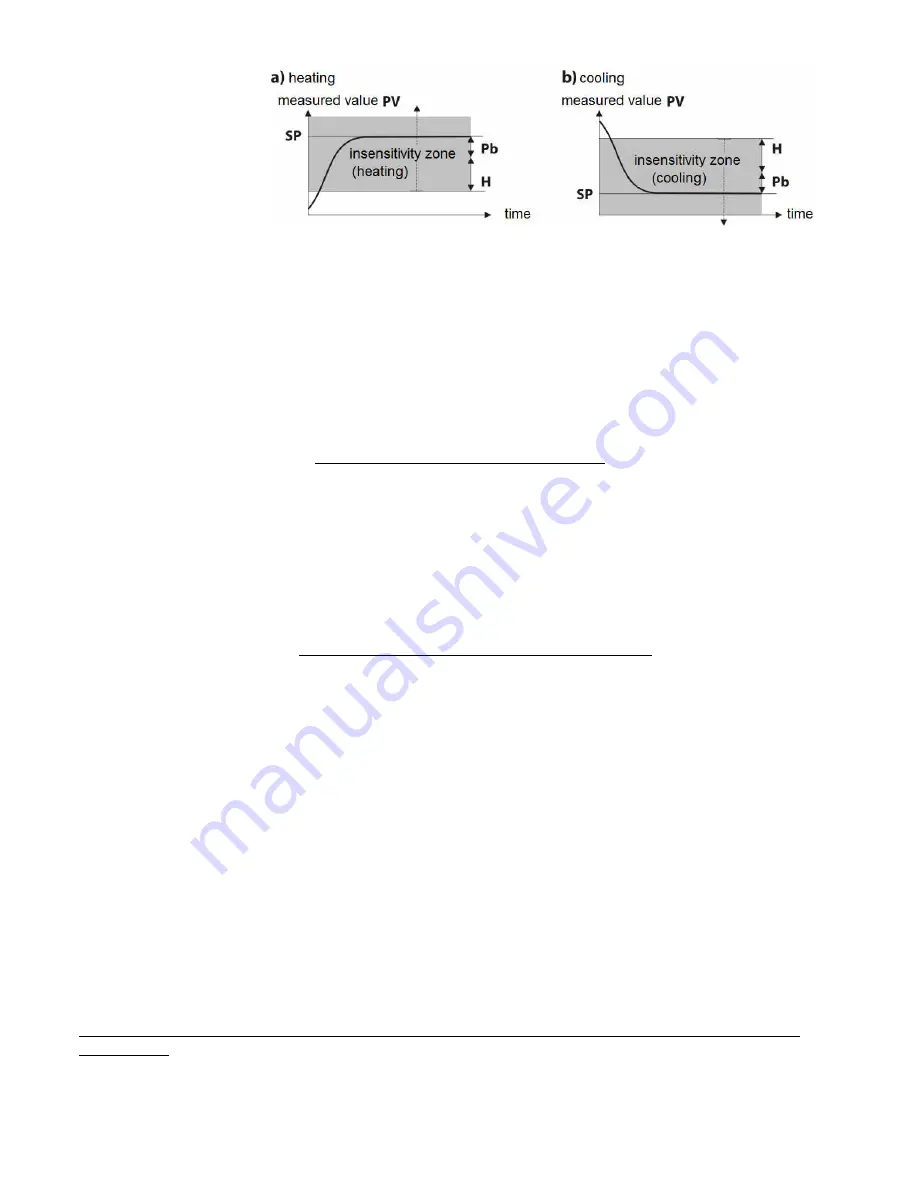
27
Pb
and the associated
Hysteresis H
(
H1
or
H2
) in relation to the
Selected setpoint value SP
, as shown in figure 12.4.2.2.
Fig. 12.4.2.2. Location of
the insensitivity zone
for the
Control type
of
heating
and
cooling
.
In order to avoid unnecessary activation of tuning, which may slow down the process, it is recommended to set
the highest possible value of the assigned
Hysteresis H
, not less than 10÷30% of the range of variability of the
process (e.g. the measured temperature). Testing of the object with temporary switchoff of the output and the
ST-PID
message in the control status also takes place in the insensitivity band if sudden changes in the
measured value
PV
or the setpoint value
SP
are detected. The choice of the parameter selection method
depends on the nature of the initial conditions. In the case of a stabilized controlled value, the
Step response
method (quick)
is selected; otherwise, the
Oscillation method (slower)
is selected.
Automatic selection
enables optimum selection of the PID parameters for the current conditions at the object,
without the user's involvement. It is recommended for variable value regulation (disturbance of the conditions
determined during the operation due to the change of, e.g. the setpoint value or the weight of the furnace batch).
b)
Step response method (quick)
- selection of parameters in the run-up phase (response to step function).
During determination of the object's characteristics, the algorithm does not cause any additional delay in
reaching the setpoint value. This method is intended specifically for objects of stabilized initial value of the
controlled value (e.g. temperature in a cold furnace). In order to avoid disturbing stabilized initial conditions,
before the automatic tuning is switched on, the power supply of the operating element (e.g. a heater) should be
switched off using an external connector or the regulation start/stop function should be used (buttons or
BIN
inputs). The power supply must be switched on immediately after the tuning is started, in the output switch-on
delay phase. If the power supply is switched on later, an erroneous analysis of the object and improper selection
of PID parameters will result.
c)
Oscillation method (slower)
- selection of parameters using the oscillation method. The algorithm consists in
measuring the amplitude and the period of oscillation on a slightly lower level (in the case of heating; higher
level - in the case of cooling) than the setpoint value, thus eliminating the risk of exceeding the target value at
the object testing stage. During determination of the object's characteristics, the algorithm causes additional
delays in reaching the setpoint value. This method is intended specifically for objects of unstable initial value of
the controlled value (e.g. temperature in a hot furnace).
The algorithms described in items
b
and
c
comprise the following steps:
- delay of output switch-on (approx. 15 s);
- time for switching on the power supply of the operating element (heating/cooling power, fan, etc.);
- determination of the object's characteristics;
- calculation and permanent saving of data (
Pb
,
Ti
,
Td
, and
Tc
, chapter 12.4.2), in a selected
Set of PID parameters
- enabling control for a selected output with new PID settings
Program interruption of autotuning
b
or
c
(with a window with information on the cause of the interruption of the
algorithm, chapter 15) may take place if the conditions for proper operation of the algorithm are not met, such as:
- the initial value
PV
is larger than the setpoint value
SP
for heating or smaller than the setpoint value for cooling;
- the maximum tuning time (4 hours) has been exceeded;
- the process value is changing too fast or too slowly.
It is recommended to restart the automatic tuning
b
or
c
after a significant change in the
SP
threshold or the
controlled object's parameters (e.g. the heating/cooling power, the batch weight, the initial temperature, etc.).
Due to its own time relationships and other operating parameters, autotuning does not work in the program
control mode.