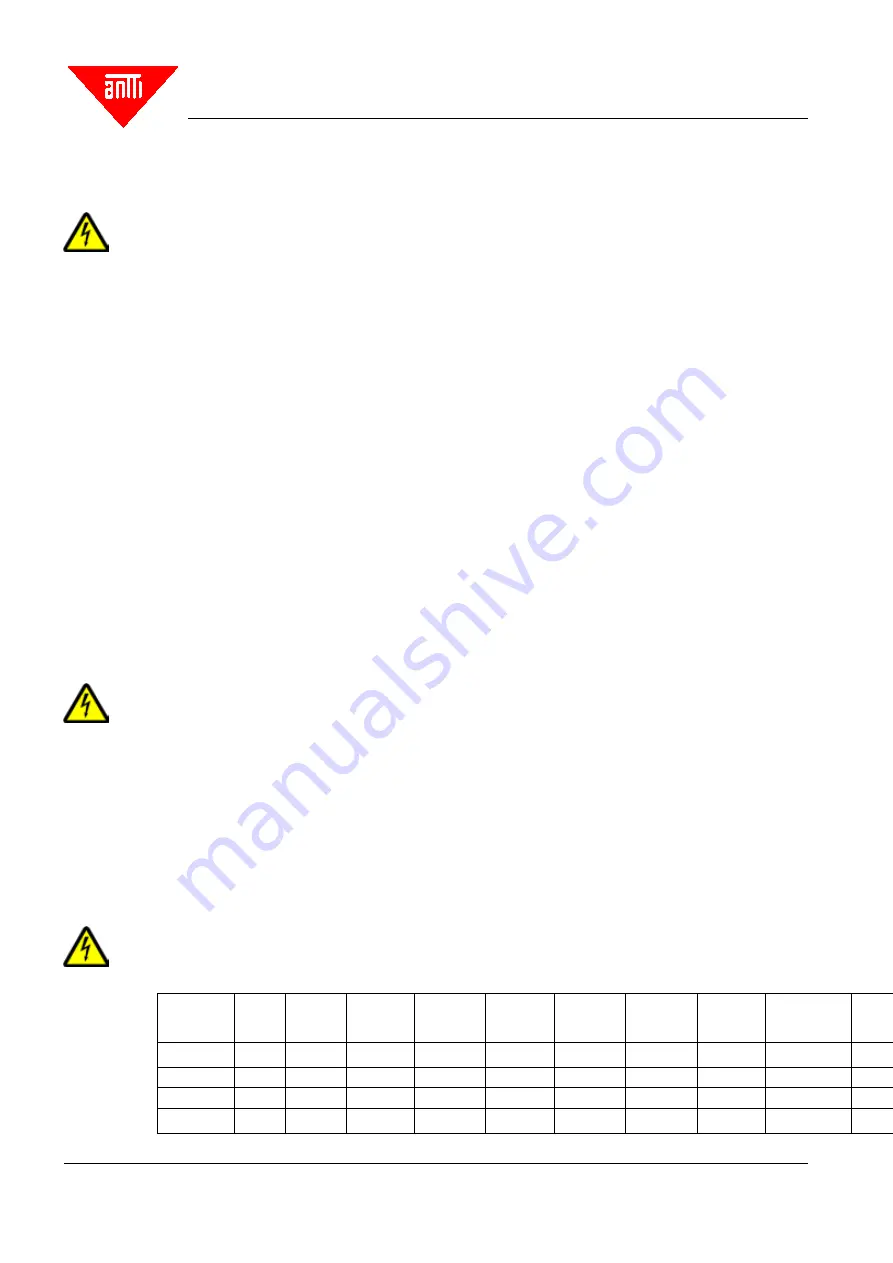
Antti-Teollisuus Oy
42
408111 03-2019
Vacboost M13
2. STARTING UP
Particular caution must be exercised during the start-up and the test run. Only an authorised electrician
is allowed to change the settings of the protective devices. Always switch off the decoupling switch of the
device or the mains switch before carrying out any tasks that require the protective covers of the devices
to be opened. Only an authorised electrician is allowed to carry out tasks that require that the electric
connections be changed or the connecting boxes be opened.
Always before testing the machinery, check visually that all the installations have been properly completed, and all
the protective covers are in place and all the cover plates are closed. Also the start-up inspection according to the
regulations for the electro-technical industry must have been performed, where applicable.
Also check before the test run that the current values for the motor protection switches and the thermo-relays match
the values given in the nameplates of the motors. The blower outlets are equipped with thermo-relays. Their current
values shall be set to 0.58 times the rated current mentioned in the motor's nameplate. The other motor outlets
have motor protection switches. Their current value shall be set to the value mentioned in the motor's nameplate.
The blower outlet is equipped with a star-delta starter. Set the time-relay of the star-delta starter as instructed in
the drawing delivered with the wiring diagrams.
The outlets of 5.5 kW and above – except for the ones for the blowers – are equipped with attenuators. Also check
the settings of the attenuated starter(s) in the drawing.
2.1 Elevator
Check the installation and connection of the underspeed guard for the elevator. If the underspeed guard is elec-
tronic, check also that the distance between the guard's sensor and the rotator plate is correct. If the elevator is
equipped with a back rotation preventer, it must be removed before the test run.
Switch the selector switch to position E. Switch the elevator switch to position 1. The elevator should now
start. Check and, as required, change the direction of rotation of the elevator. Stop the elevator by turning
the elevator switch to position 0.
Check the operation of the electronic underspeed guard by removing the connecting box of the guard's sensor.
Start the elevator by turning the elevator switch to position 1. The elevator should first start and then stop after
about 8 seconds of operation.
Check the operation of the dryer's upper limit sensor by turning the elevator's selector switch to position 2. The
elevator should start. Touch the dryer's upper limit sensor by your hand. The elevator should stop.
2.2 Pre-cleaner
Turn the selector switch to position E. Turn the pre-cleaner switch to position 1. Check and, as required,
change the direction of rotation of the pre-cleaner.
Mobile
dryer model
Heater
model
Burner
Max. oil
flow kg/h
Nozzle
pressure
bar
Nozzle 1
Nozzle 2
1-air cam
wheel III
2-air cam
wheel I
2- magn.
valve cam
wheel V
Adjust-
ment
ring
C205
200
KP-26H2 15,3
10
3 gal 80° 1 gal 80° 30°
50°
C255/C320 300
KP-26H2 27,8
12,5
4,5 gal 80° 2 gal 80° 32°
52°
40°
50 mm
C365
400
KP-50H
37,1
13
5,5 gal 80° 3 gal 80° 20°
38°
29°
5
C365
500
KP-50H
46,4
13,5
6,5 gal 80° 4 gal 80°
To reset a failure in the burner, press down the burner relay button with illuminated malfunction light at the side
of the burner.
Содержание Vacboost M13
Страница 11: ...Antti Teollisuus Oy 11 408111 03 2019 Vacboost M13 C365E A1500 kW 1x15 kW_Mitttakuva C 365E A1500 kW 1x15 kW ...
Страница 12: ...Antti Teollisuus Oy 12 408111 03 2019 Vacboost M13 C410E 700 kW 2x7 5 kW_Mitttakuva C 410E 700 kW 2x7 5 kW ...
Страница 13: ...Antti Teollisuus Oy 13 408111 03 2019 Vacboost M13 C410E 1000 kW 2x15 kW_Mitttakuva C 410E 1000 kW 2x15 kW ...
Страница 14: ...Antti Teollisuus Oy 14 408111 03 2019 Vacboost M13 C410E A1500 kW 2x15 kW_Mitttakuva C 410E A1500 kW 2x15 kW ...
Страница 17: ...Antti Teollisuus Oy 17 408111 03 2019 Vacboost M13 C 255 C 255_malli ...
Страница 18: ...Antti Teollisuus Oy 18 408111 03 2019 Vacboost M13 C 320 C 320_malli ...
Страница 19: ...Antti Teollisuus Oy 19 408111 03 2019 Vacboost M13 C 365 C 365_malli ...
Страница 20: ...Antti Teollisuus Oy 20 408111 03 2019 Vacboost M13 C365 E A1500_3D C365 E A1500 ...
Страница 21: ...Antti Teollisuus Oy 21 408111 03 2019 Vacboost M13 C 410 E 700_3D C410 E 700 ...
Страница 22: ...Antti Teollisuus Oy 22 408111 03 2019 Vacboost M13 C410 E 1000_3D C410 E 1000 ...
Страница 23: ...Antti Teollisuus Oy 23 408111 03 2019 Vacboost M13 C 410 E A1500_3D C410 E A1500 ...
Страница 25: ...Antti Teollisuus Oy 25 408111 03 2019 Vacboost M13 ...
Страница 32: ...Antti Teollisuus Oy 32 408111 03 2019 Vacboost M13 C365 uunin putket Heater pipes C365 ...
Страница 33: ...Antti Teollisuus Oy 33 408111 03 2019 Vacboost M13 D800 putket D800 pipes ...
Страница 35: ...Antti Teollisuus Oy 35 408111 03 2019 Vacboost M13 Puhallinteline asentaminen ...
Страница 64: ...Antti Teollisuus Oy 64 408111 03 2019 Vacboost M13 ...