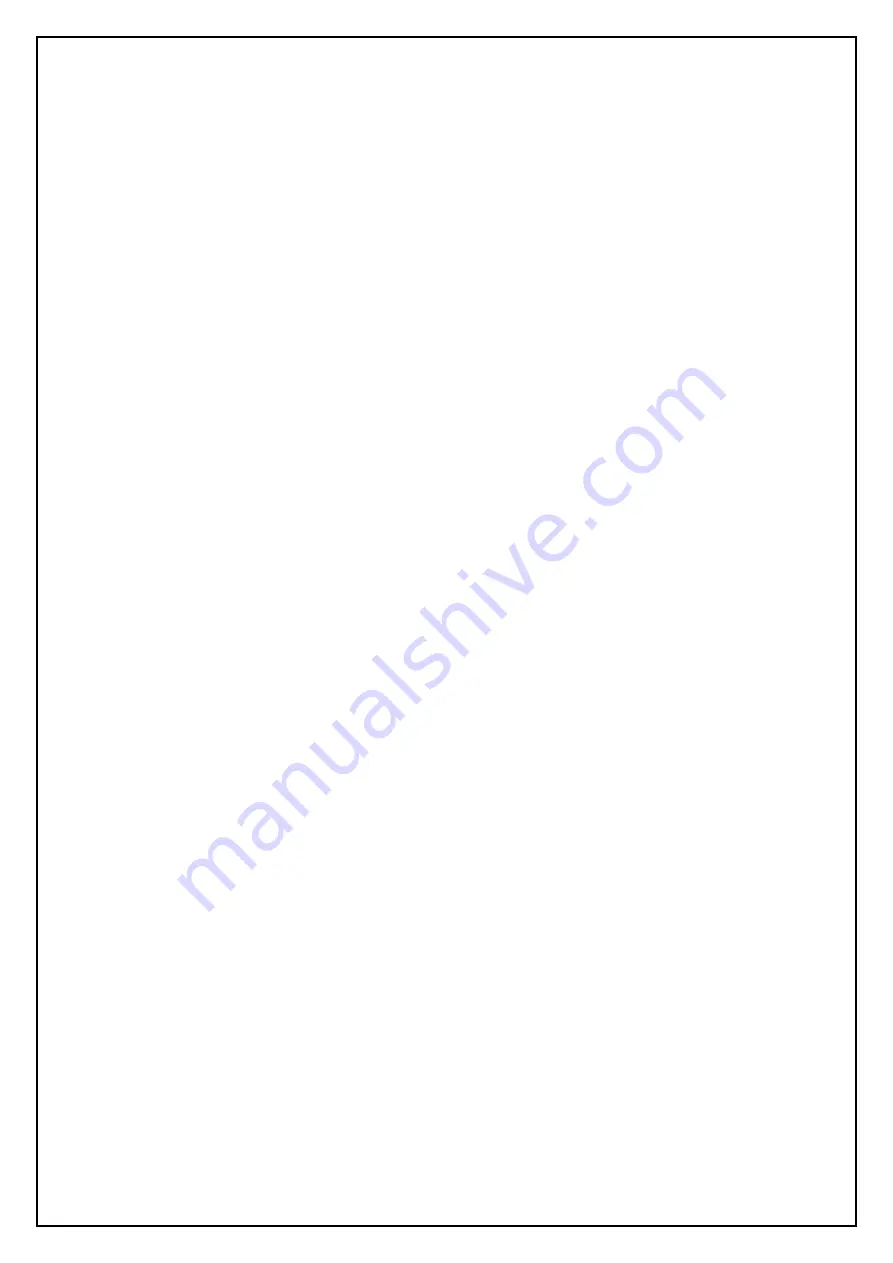
4
amiad
filtration systems
SAFETY INSTRUCTIONS
General
1. Prior to installation or any treatment given to the
filter, read carefully the installation and operation
instructions.
2. While treating the filter all conventional safety
instructions should be observed in order to avoid
danger to the workers, the public or to property
in the vicinity.
3. Please note, the filters enters into a flushing
mode automatically, without prior warning.
4. No changes or modification to the equipment are
permitted without a written notification given by
the manufacturer or by its representative, on the
manufacturer behalf.
Installation
1. Install the filter according to the installation
instructions detailed in this manual.
2. Make sure to leave enough clearance so as to
enable easy access for future treatments and
safe maintenance operations.
3. Electric wiring should be performed by an
authorized electrician only, using standardized
and approved components.
4. Install main power disconnect cut-off switch
close to the control panel.
5. If the control panel is installed far away and
there is no eye contact with the filter, a power
disconnect cut-off switch should be installed
near each filter unit.
6. Installation of the filter should be performed so
as to avoid direct water splashing on the
electrical components or on the control panel.
7. Extra safety devices should be installed on hot
water applications to avoid skin burn danger.
Operation, Control and Maintenance
1. Disconnect the filter from power supply before
maintenance or treatment.
2. Loosening or unscrewing bolts should be done
only after the pressure in the filter had been
released.
3. Avoid splashing and water leaking so as to
minimize slipping electrifying danger or damage to
the equipment caused by moisture.
4. Always open and close valves slowly and
gradually.
5. Remove grease and fat material residues in order
to avoid slipping.
6. After treatment has been completed, re-assemble
the protection covers of the drive mechanism.
7. Manual cleaning of filter element using high water
pressure or steam, should be performed in
accordance with the cleaning system instructions
and without endangering the operator or his
vicinity.
8. Manual cleaning of filter element using acid or
other chemical agents, should be performed in
accordance with the relevant material safety
instructions and without endangering the operator
or his vicinity.
Use of Lifting Equipment
1. While using lifting equipment, make sure that the
filter or the lifted part is chained securely and in a
safe manner.
2. Do not leave lifted equipment if there is no
necessity. Avoid working below lifted equipment.
3. Ware a safety helmet while using lifting equipment
Содержание 2-84
Страница 12: ...12 amiad filtration systems PARTS DRAWING Section 1 ...
Страница 13: ...13 amiad filtration systems PARTS DRAWING Section 2 ...
Страница 14: ...測試 OFF ON 電源開關 電源指示 異常指示 極限指示 排水閥 復歸 馬達指示 時間 差壓 差壓 連續 LG1 LG2 LG3 CS1 LG4 LG5 CS2 PB1 PB2 T1 CT1 14 ...
Страница 15: ...480V 110V 24V 150VA TRANSFORER R2 R1 POWER SOURCE BY CUSTOMER BY CUSTOMER OPTION 15 ...
Страница 17: ...測試 差壓信號 計時器信號 上極限 下極限 清洗馬達過載 時間 連續 異常復歸 REMOTE PAUSE REMOTE RESET 17 ...
Страница 18: ...逆洗完成 計時器 計數器 排水閥 逆洗 過濾 清洗馬達正轉 清洗馬達反轉 DC24V DC24V 異常 極限指示 18 ...