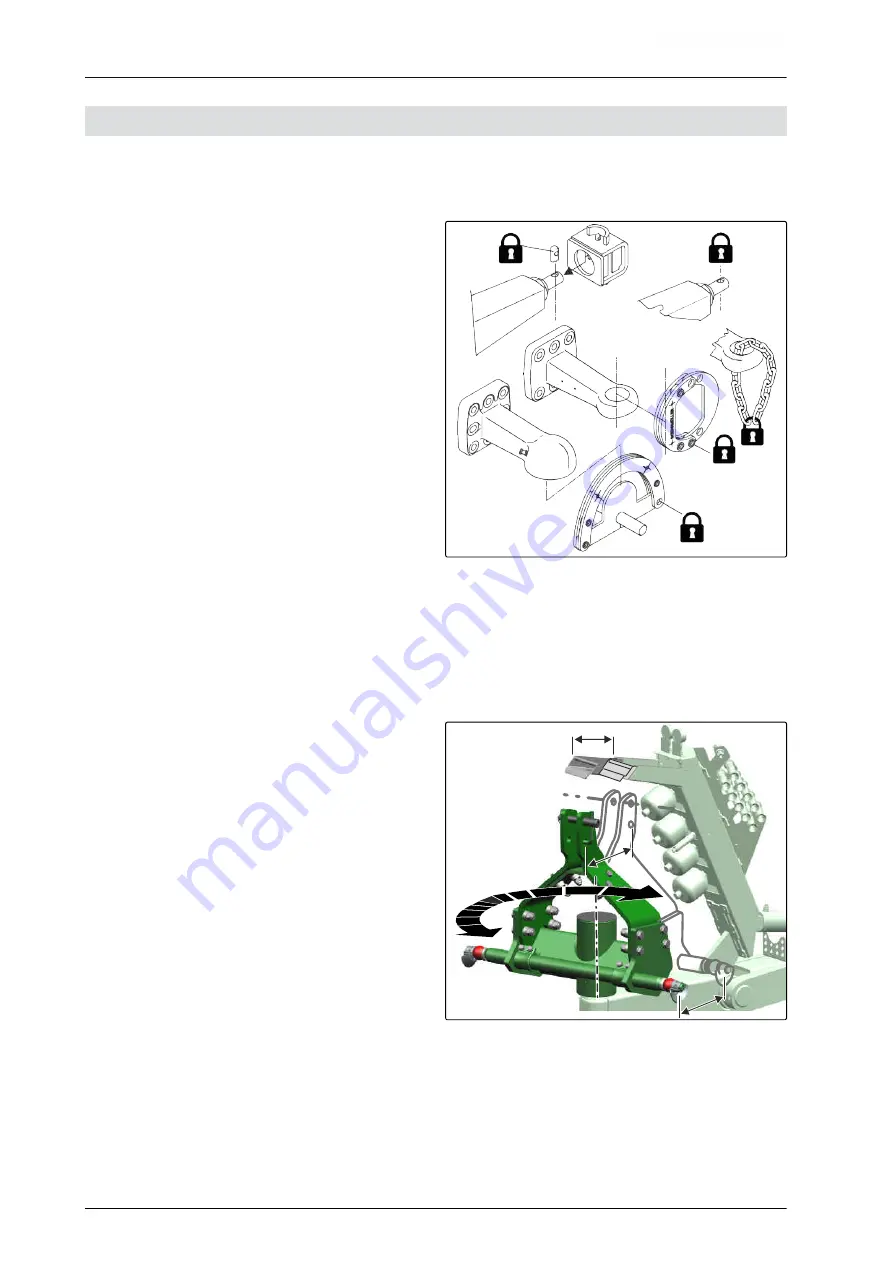
6.2 Coupling the implement
6.2.1 Removing the safety device against unauthorised use
1.
Unlock the padlock.
2.
Remove the safety device against unauthorised
use from the hitch device.
CMS-I-00003534
6.2.2 Couple the headstock
The machine can be coupled in two different
positions.
1.
For more manoeuvrability
turn headstock forward.
or
to improve the pull line and reduce lateral pull,
turn headstock to the rear.
2.
Adapt hose routing.
CMS-I-00005119
CMS-T-00006484-E.1
CMS-T-00005089-B.1
CMS-T-00007428-B.1
6 | Preparing the machine
Coupling the implement
MG7196-EN-GB | G.1 | 26.07.2022 | © AMAZONE
46
Содержание Tyrok 400
Страница 1: ...Original operating manual Trailed reversible plough Tyrok 400 Tyrok 400 V SmartLearning www amazone de...
Страница 6: ......
Страница 107: ......