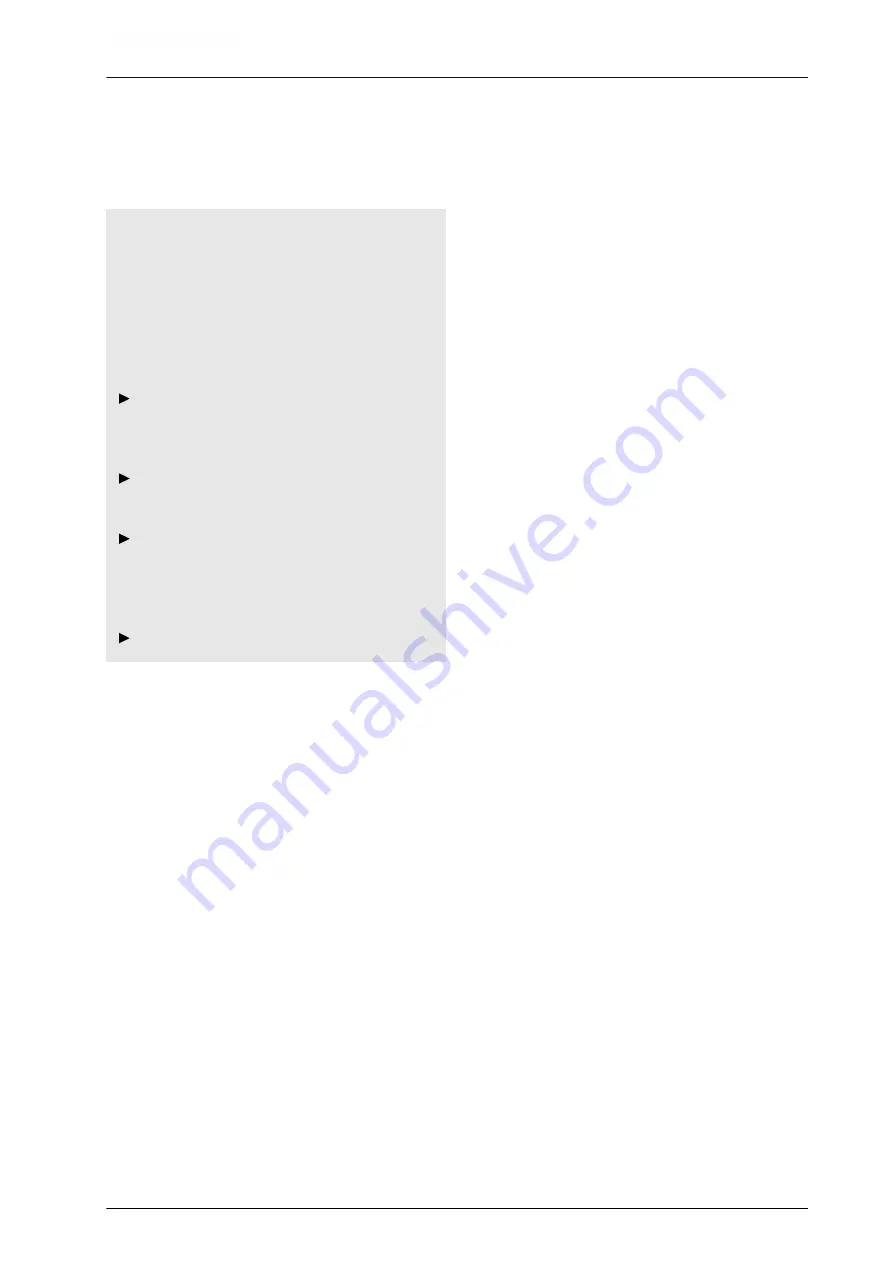
2.1.3 Safe operation and handling of the machine
2.1.3.1 Coupling implements
Coupling the implement to the tractor
Incorrectly coupling of the implement to the
tractor results in hazards that can cause serious
accidents.
There are crushing and shear points in the area
of the coupling points between the tractor and the
implement.
If you couple or uncouple the implement to
or from the tractor,
be very careful.
Use only suitable tractors for coupling and
transporting the implement.
If the implement is coupled to the 3-point
power lift of the tractor,
make sure that the mounting categories of
the tractor and implement are compatible.
Couple the implement properly to the tractor.
CMS-T-00002304-G.1
CMS-T-00002320-C.1
2 | Safety and responsibility
Basic safety instructions
MG6878-EN-II | D.1 | 18.05.2021
13
Содержание KE 3002
Страница 1: ...Original operating manual Rotary harrow KE 3002 KE 4002 SmartLearning www amazone de ...
Страница 6: ......
Страница 119: ......