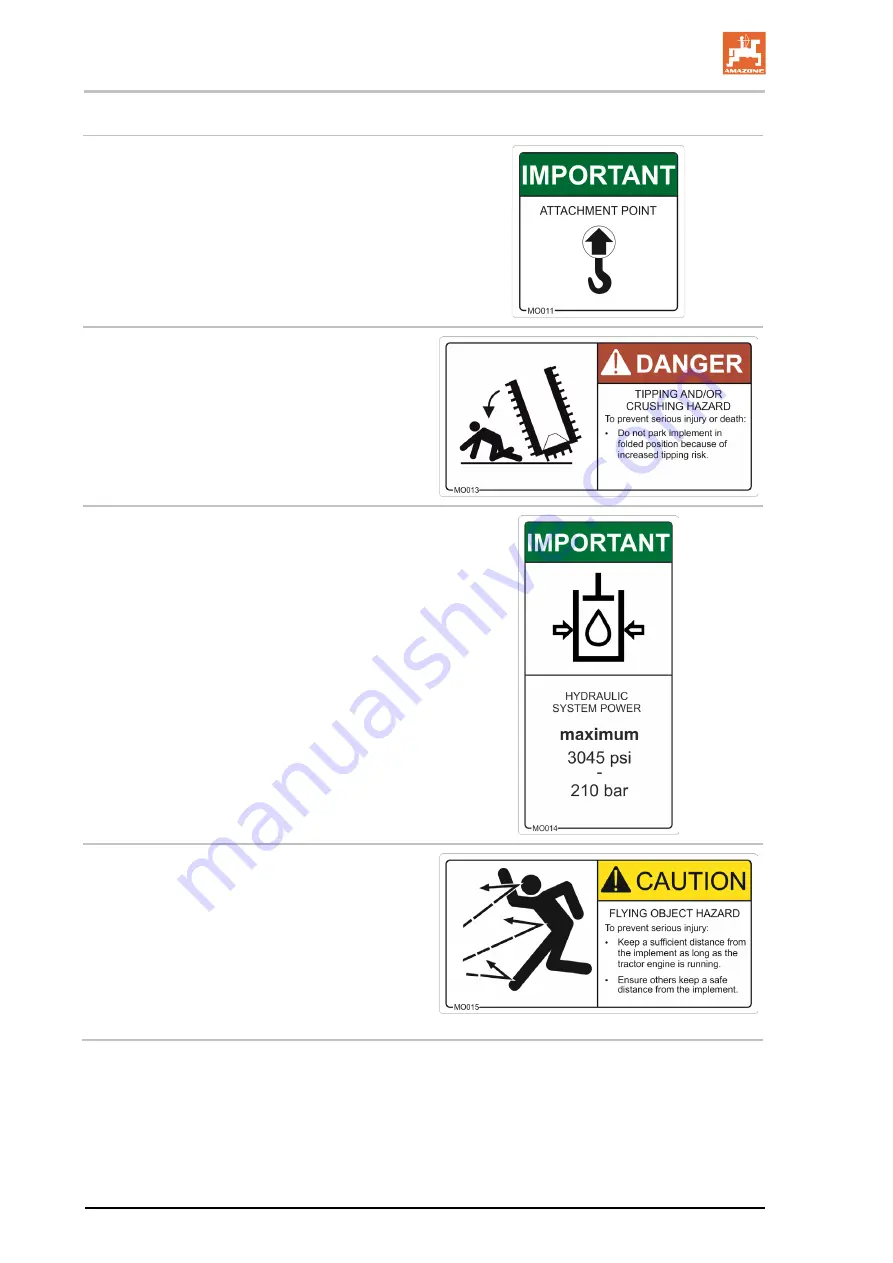
General Safety Instructions
20
Catros BAG0053.14 10.17
MO011
Attachment Point
This symbol indicates lifting points for fastening
slings when loading the implement.
MO013
Tipping and/or Crushing Hazard
To prevent serious injury or death:
•
Do not park implement in folded position
because of increased risk.
MO014
Hydraulic System Power
The maximum operating pressure of the hydrau-
lic system is 3045 psi [210 bar].
MO015
Flying Object Hazard
To prevent serious injury:
•
Keep a sufficient distance from the imple-
ment as long as the tractor engine is run-
ning.
•
Ensure that others keep a safe distance
from the implement.
Содержание Catros 3001
Страница 88: ...Cleaning maintenance and repairs 88 Catros BAG0053 14 10 17 Offset of the disc gangs Fig 74 ...
Страница 90: ......