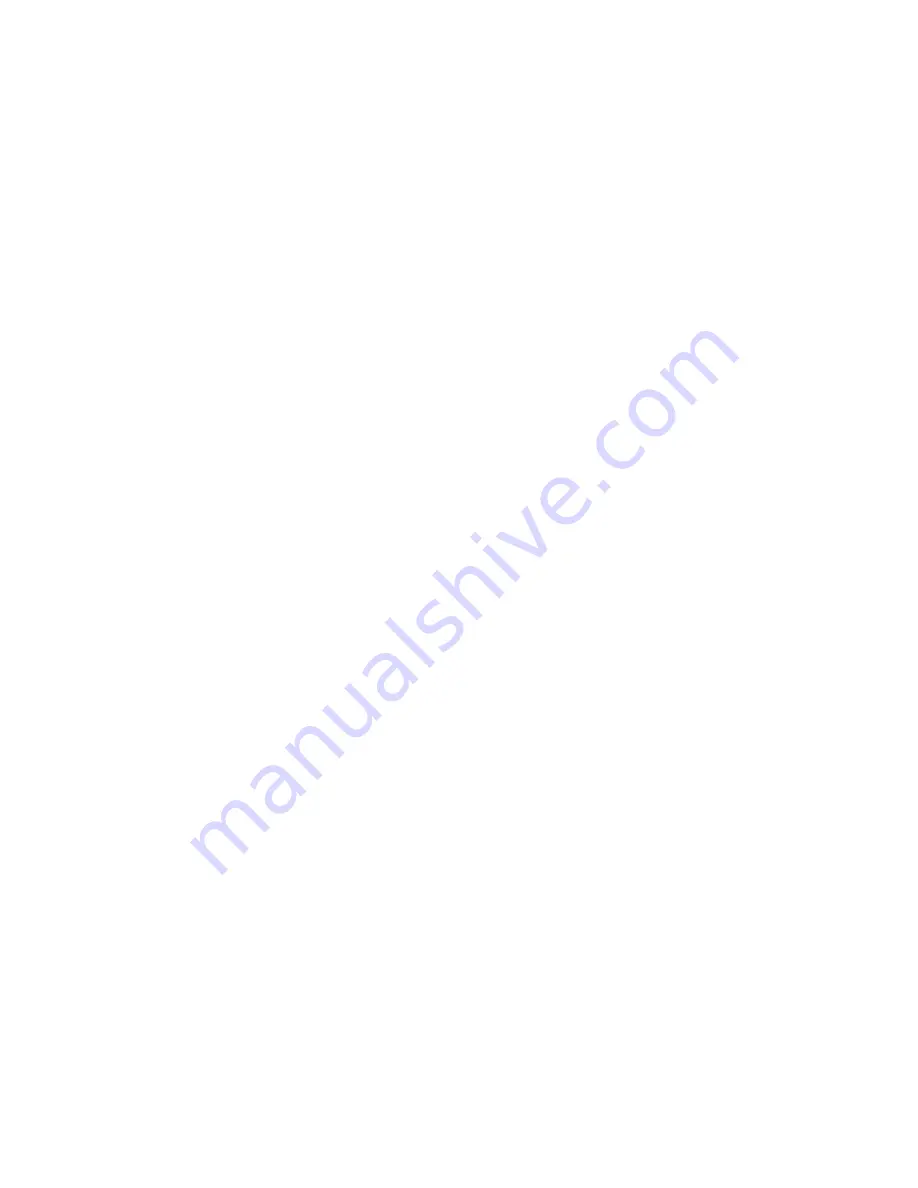
SERVICING
43
2. For best results, temporarily install a thermometer on the
liquid line at the liquid line service valve and 4-6" from the
compressor on the suction line. Ensure the thermometer
makes adequate contact and is insulated for best possible
readings. Use liquid line temperature to determine sub-
cooling and vapor temperature to determine superheat.
NOTE: A
N
OPTIONAL
METHOD
IS
TO
LOCATE
THE
THERMOMETER
AT
THE
SUCTION
LINE
SERVICE
VALVE
. E
NSURE
THE
THERMOMETER
MAKES
ADEQUATE
CONTACT
AND
IS
INSULATED
FOR
BEST
POSSIBLE
READINGS
.
3. Refer to the superheat table provided for proper system
superheat. Add charge to lower superheat or recover charge
to raise superheat.
Superheat Formula = Suct. Line Temp. - Sat. Suct. Temp.
EXAMPLE:
a. Suction Pressure = 143 psi
b. Corresponding Temp. = 50°F.
c. Thermometer on Suction Line = 58°F.
To obtain the degrees temperature of superheat, subtract 50.0
from 58.0°F.
The difference is 8° Superheat. The 8° Superheat would fall in the
± range of allowable superheat.
SUPERHEAT AND SUBCOOLING ADJUSTMENT ON TXV APPLICATIONS
NOTE:
Subcooling and superheat infomration is valid only while
the unit is operating at 100% capacity or 100% compressor speed
in CHARGE MODE.
Compressor speed is displayed under STATUS menu in the
thermostat.
1. Run system at least 10 minutes to allow pressure to
stabilize. During the adjustment of subcooling, ambient
temperature should be greater than 65°F and less than
105°F. If ambient temperature is out of range, don’t adjust
subcooling.
2. For best results, temporarily install a thermometer on the
liquid line at the liquid line service valve and 4-6" from the
compressor on the suction line. Ensure the thermometer
makes adequate contact and is insulated for best possible
readings. Use liquid line temperature to determine sub-
cooling and vapor temperature to determine superheat.
NOTE:
A
N
OPTIONAL
METHOD
IS
TO
LOCATE
THE
THERMOMETER
AT
THE
SUCTION
LINE
SERVICE
VALVE
. E
NSURE
THE
THERMOMETER
MAKES
ADEQUATE
CONTACT
AND
IS
INSULATED
FOR
BEST
POSSIBLE
READINGS
.
3. The system subcooling should be 7 to 9°F. If not in that range,
adjust subcooling and superheat according to the following
procedure.
a.
If subcooling and superheat are low, adjust TXV to 7 to
9°F superheat, then check subcooling.
NOTE:
To adjust superheat, turn the valve stem clock-
wise to increase and counter clockwise to decrease.
b.
If subcooling is low and superheat is 7 to 9°F, add
charge to rise subcooling to 7 to 9°F, then check super-
heat.
c.
If subcooling is low and superheat is high, add charge
to rise subcooling to 7 to 9°F, then check superheat.
d.
If subcooling is 7 to 9°F and superheat is high, adjust
the TXV valve to 7 to 9°F superheat, then check
subcooling.
e.
If subcooling and superheat are high, adjust the TXV
valve to 7 to 9°F superheat, then check subcooling.
f.
If subcooling is high and superheat is 7 to 9°F, remove
charge to lower the subcooling to 7 to 9°F, then check
superheat.
g.
If subcooling is high and superheat is low, adjust the
TXV valve to 7 to 9°F superheat and remove charge to
low the subcooling to 7 to 9°F.
h.
If subcooling is 7 to 9°F and superheat is low, adjust
the TXV valve to 7 to 9°F superheat and remove charge
to lower the subcooling 7 to 9°F, then check the super-
heat.
NOTE:
Not more than 0.5 lb. (8 Oz.) of refrigerant must
be added to the system in order to achieve the target
subcooling. It is recommended to add 4 oz. refrigerant
each time and try adjusting the TXV and let the system
stabilize.
4. Disconnect manifold set. Installation is complete.
S-110
CHECKING EXPANSION VALVE OPERATION
1. Remove the remote bulb of the expansion valve from the suc-
tion line.
2. Start the system and cool the bulb in a container of ice water,
closing the valve. As you cool the bulb, the suction pressure
should fall and the suction temperature will rise.
3. Next warm the bulb in your hand. As you warm the bulb, the
suction pressure should rise and the suction temperature will
fall.
4. If a temperature or pressure change is noticed, the expansion
valve is operating. If no change is noticed, the valve is re-
stricted, the power element is faulty, or the equalizer tube is
plugged.
5. Capture the charge, replace the valve and drier, evacuate and
recharge.