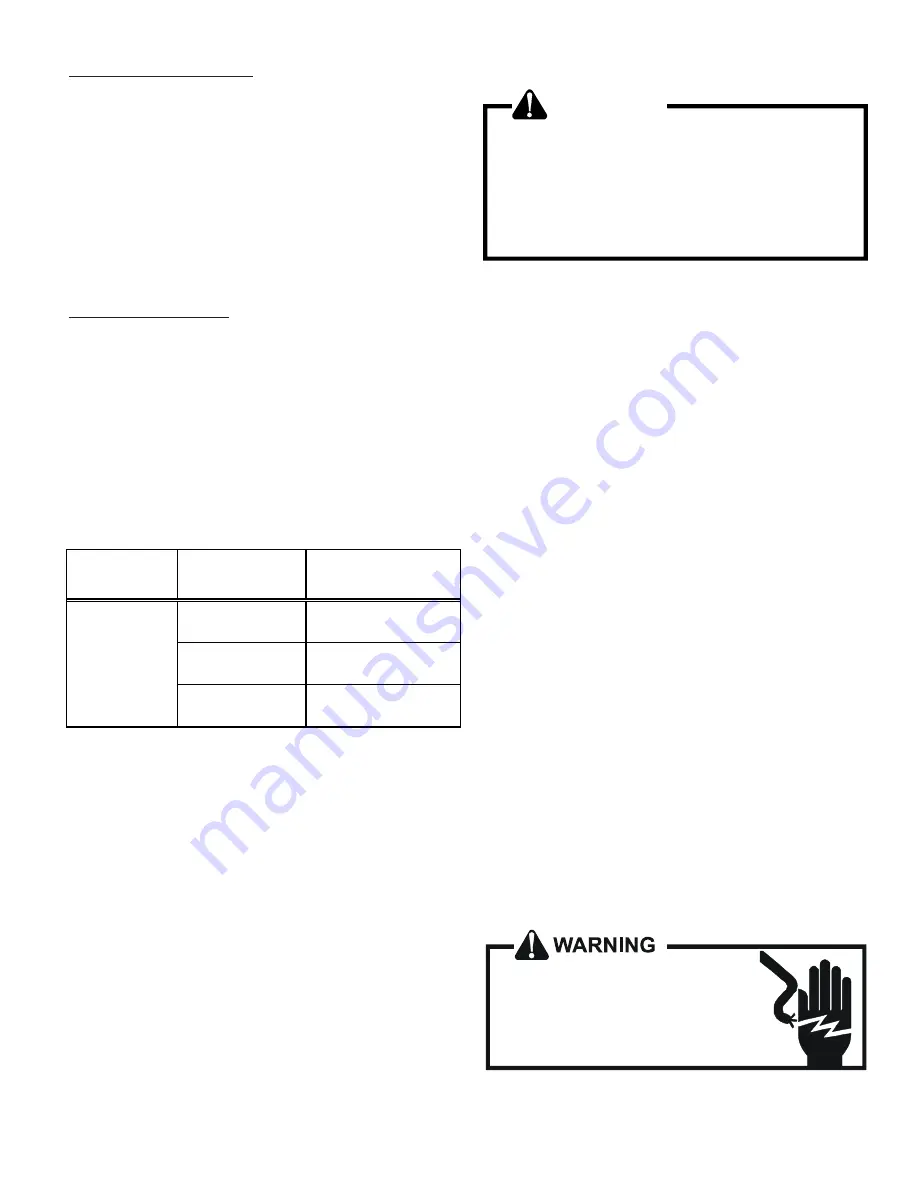
SERVICING
35
3.0 Continuous Fan Operation
2.1 With a demand for continuous fan operation, the CTK04
thermostat sends a fan request to the integrated air handler
control along with a fan demand. The control energizes
the variavble speed ECM motor at fan demand provided by
the thermostat. The fan demand provided by the thermostat
will be 30%, 50%,or 70% of the air handler's maximum
airflow capability. The continuous fan demand is set from
the thermostat as low, medium, or high.
2.2 If the thermostat demand for continuous fan is removed,
the CTK04 thermostat commands the integrated air handler
control to end continuous fan operation. The integrated
AH control immediately de-energizes the ECM blower motor.
3.0. Airflow Consideration
Airflow demands are managed differently in a fully communicat-
ing system than in a non-communicating wired system. The sys-
tem operating mode (as determined by the thermostat) deter-
mines which unit calculates the system airflow demand. If the
indoor unit is responsible for determining the airflow demand, it
calculates the demand and sends it to the ECM motor. If the out-
door unit or thermostat is responsible for determining the de-
mand, it calculates the demand and transmits the demand along
with a fan request to the indoor unit. The indoor unit then sends
the demand to the ECM motor. The table below lists the various
ComfortNet™ systems, the operating mode, and airflow demand
source.
System
System Operating
Mode
Airflow Demand
Source
Cooling
Air Conditioner
Heating
Air Handler
Continuous Fan
Thermostat
Air Condi
Air Handler
For example, assume the system is an air conditioner matched
with an air handler. With a call for cooling, the air conditioner
will calculate the system’s cooling airflow demand. The air condi-
tioner will then send a fan request along with the cooling airflow
demand to the air handler. Once received, the air handler will
send the cooling airflow demand to the ECM motor. The ECM
motor then delivers the cooling airflow. See the applicable
ComfortNet™ air conditioner installation manual for the airflow
delivered during cooling.
In continuous fan mode, the CTK04 thermostat provides the
airflow demand. The CTKO4 provides 4 continuous fan speeds
(25%, 50%, 75% and 100% of maximum airflow). During continuous
fan operation, the thermostat sends a fan request along with the
continuous fan demand to the air handler. The air handler, in turn,
sends the demand to the ECM motor. The ECM motor delivers the
requested continuous fan airflow.
S-17 CHECKING COMPRESSOR
WARNING
Hermetic compressor electrical terminal venting can
be dangerous. When insulating material which
supports a hermetic compressor or electrical terminal
suddenly disintegrates due to physical abuse or as a
result of an electrical short between the terminal and
the compressor housing, the terminal may be
expelled, venting the vapor and liquid contents of the
compressor housing and system.
If the compressor terminal PROTECTIVE COVER and gasket (if re-
quired) are not properly in place and secured, there is a remote
possibility if a terminal vents, that the vaporous and liquid dis-
charge can be ignited, spouting flames several feet, causing po-
tentially severe or fatal injury to anyone in its path.
This discharge can be ignited external to the compressor if the
terminal cover is not properly in place and if the discharge im-
pinges on a sufficient heat source.
Ignition of the discharge can also occur at the venting terminal or
inside the compressor, if there is sufficient contaminant air present
in the system and an electrical arc occurs as the terminal vents.
Ignition cannot occur at the venting terminal without the pres-
ence of contaminant air, and cannot occur externally from the
venting terminal without the presence of an external ignition
source.
Therefore, proper evacuation of a hermetic system is essential at
the time of manufacture and during servicing.
To reduce the possibility of external ignition, all open flame, elec-
trical power, and other heat sources should be extinguished or
turned off prior to servicing a system.
S-17A RESISTANCE TEST
Each compressor is equipped with an internal overload.
The line break internal overload senses both motor amperage
and winding temperature. High motor temperature or amperage
heats the disc causing it to open, breaking the common circuit
within the compressor on single phase units.
Heat generated within the compressor shell, usually due to recy-
cling of the motor, high amperage or insufficient gas to cool the
motor, is slow to dissipate. Allow at least three to four hours for
it to cool and reset, then retest.
Fuse, circuit breaker, ground fault protective device, etc. has not
tripped -
HIGH VOLTAGE!
Disconnect ALL power before servicing
or installing. Multiple power sources
may be present. Failure to do so may
cause property damage, personal injury
or death.