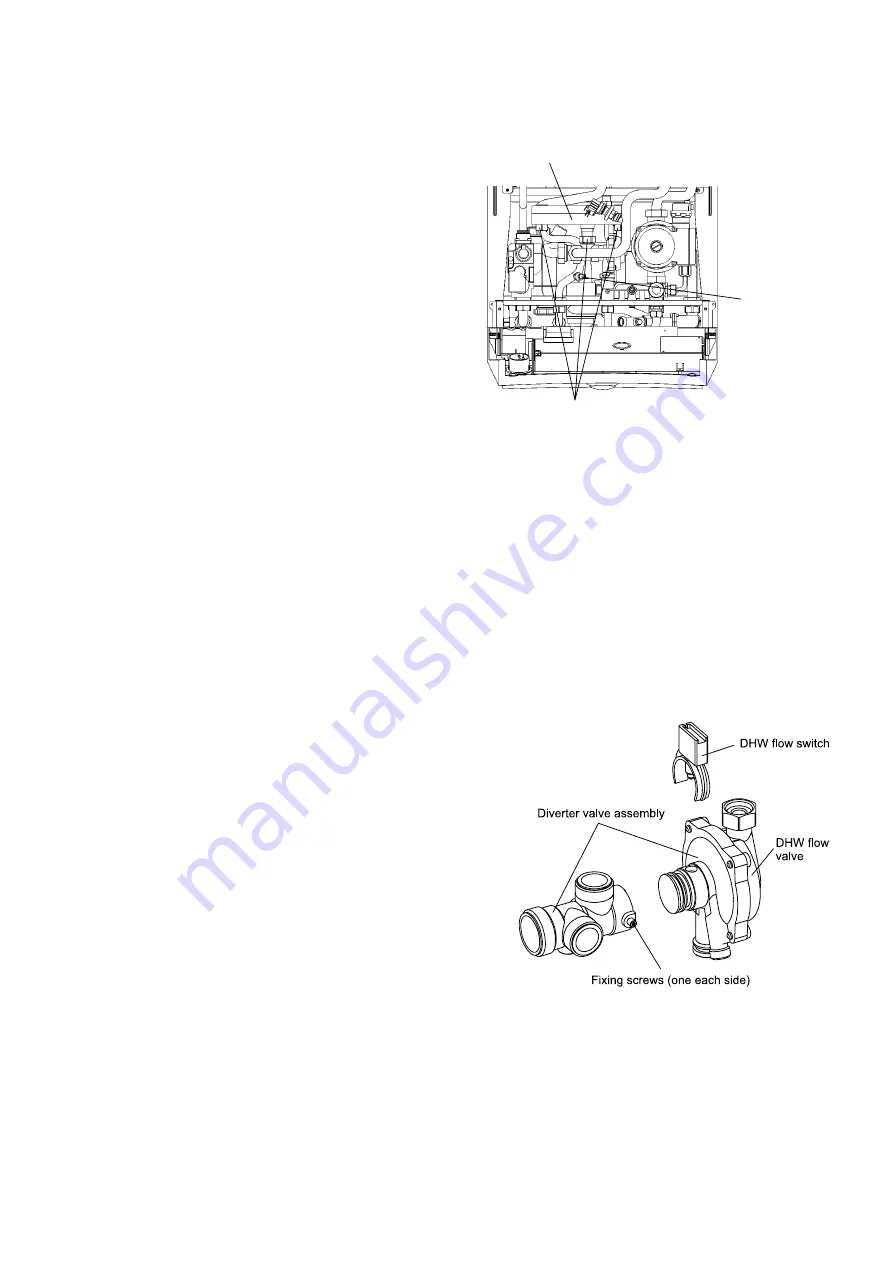
31
Fig. 35
Alpha CD24/32 - Component Replacement
Fig. 34 - CD24C/CD32C only
8.25 DHW HEAT EXCHANGER (CD24C and CD32C only) - Refer to Fig. 34
1.
Gain access behind the casing and drain the boiler heating
and hot water circuits as described in sections 8.1 and 8.2.
2.
Disconnect the three union nuts to the heat exchanger and
remove heat exchanger by lifting it upwards from the rear
right hand side 'O' ring seal connection.
Note: Be careful not to allow water to drip onto any
electrical components.
3.
Using the new washers supplied, re-assemble in reverse
order.
4.
Refill and pressurise the system. (Refer to Commissioning,
section 5.1).
8.26 MAINS WATER INLET FILTER (CD24C and
CD32C only) - Fig. 13
1.
Drain the boiler hot water circuit as described in section
8.2.
2.
Withdraw the filter after disconnecting the unions between
the inlet valve and boiler (item H in Fig. 13).
3.
Clean or replace and re-assemble in reverse order.
8.27 DIVERTER VALVE ASSEMBLY (CD24C and CD32C only) - Figs. 31 and 35
1.
Gain access behind the casing and drain the boiler heating and hot water circuits as described in sections 8.1 and 8.2.
2.
Remove the domestic hot water heat exchanger and flow switch assemblies from the diverter valve as described in
sections 8.23 and 8.15.
3.
Disconnect the union connections from the diverter valve.
4.
Release the screws shown in Fig. 31 and raise the valve slightly to disengage it from the manifold, then lift it out of the
boiler.
5.
Re-assemble in reverse order using the new seals supplied.
6.
Refill and pressurise the system. (Refer to Commissioning, section 5.1).
8.28 DHW FLOW VALVE (CD24C and CD32C only) - Fig. 35
1.
Remove the diverter valve as described in section 8.27.
2.
Unscrew (not necessary to remove) the two screws securing the
DHW flow valve to the diverter valve and withdraw the valve.
3.
When re-assembling, push the new valve into position, holding
it in, while tightening the fixing screws.
4.
Re-assemble in reverse order.
8.29 EXPANSION VESSEL - Fig. 12
Note: If there is less than 450 mm clearance above the boiler or a
rear exit flue is used, it is not possible to replace the vessel, in which
case an additional vessel should be fitted external to the boiler in
the central heating return pipe, as close to the boiler as possible
(see Fig. 5).
1.
Gain access behind the casing and drain the boiler heating
circuit as described in sections 8.1 and 8.2.
2.
Disconnect the pipe from the pump inlet manifold and
expansion vessel.
3.
Remove the four screws securing the top support plate.
4.
Lift the expansion vessel out of the boiler.
5.
When replacing the vessel, ensure that the connection is towards the front of the boiler and re-assemble in reverse order
using new seals as necessary.
6.
Refill and pressurise the system. (Refer to Commissioning, section 5.1).
DHW heat exchanger
DHW sensor
Union nuts
Содержание Alpha CD24
Страница 43: ...43...