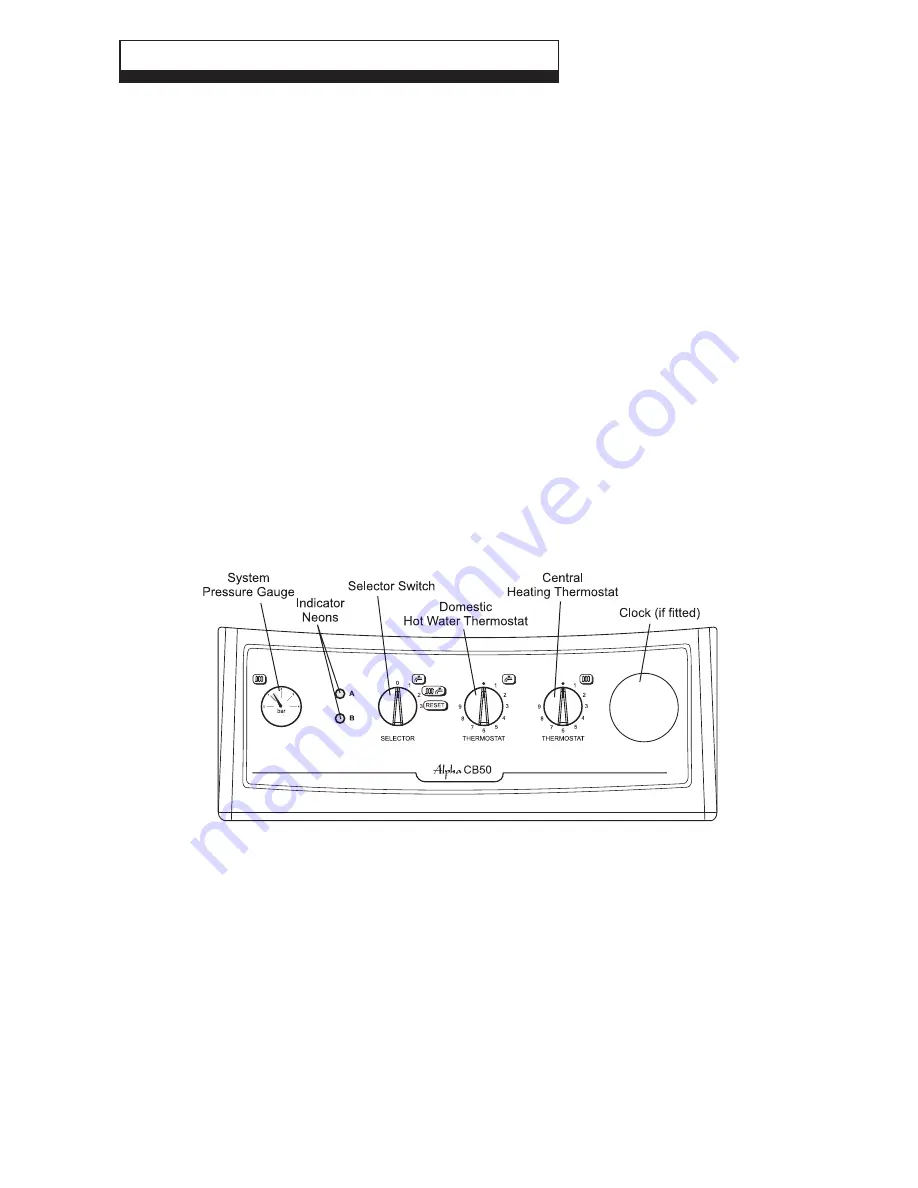
17
When commissioning the boiler, ensure the Benchmark Log Book is completed.
5.1
FILL THE SYSTEM
1.
The boiler is fitted with an automatic air vent positioned on the pump (see Fig. 2). The vent is always open and has no
sealing cap.
2.
Open the central heating flow and return valves (slot in-line with valve) (see Fig. 12).
3.
Open the fill point valve on the filling loop until water is heard to flow. To aid venting, the boiler drain point (see Fig. 2) may
be opened until water flows out. Close the drain point as soon as water appears.
4.
To remove the air - Vent each radiator in turn, starting with the lowest in the system.
5.
It is important that the pump is properly vented to avoid it running dry and damaging its bearings. Unscrew and remove the cap
from the centre of the pump. Using a suitable screwdriver rotate the exposed spindle about half a turn, then replace the cap.
6.
Check the operation of the pressure relief valve (see Fig. 2) by turning the head anti-clockwise until it clicks. The click is
the valve lifting off its seat allowing water to escape from the system - check that this is actually happening.
7.
Continue to fill the system until the pressure gauge indicates 1.0 bar. Close the fill point valve and check the system for
water soundness, rectifying where necessary. Disconnect the filling loop from the mains supply.
Water may be released from the system by manually operating the drain point (see Fig. 2) until the system design
pressure is obtained. The system design pressure (cold) should be between 0.75 and 1.25 bar.
Refer to sections 3.7 and 3.8. System volume and Filling the system.
8.
Open the mains water inlet valve (see Fig. 12). Thoroughly flush out the hot water system by turning on all hot water taps
and allow water to flow until no air is present, this will automatically vent the store of air. Turn off taps and close the mains
inlet vlave.
9.
Drain the store, using the drain point (I in Fig. 12), to flush any debris that may have collected in the store. Re-fill and vent
the system as described above.
Note: When draining the system ensure all electrical components are protected from water.
5.2
BOILER CONTROLS - Fig. 17
Alpha CB50 - Commissioning
5
COMMISSIONING
5.3
TEST FOR GAS SOUNDNESS AND PURGE THE SUPPLY
1.
With the boiler gas service cock closed (slot at right angles to valve). Pressure test the gas supply and inlet pipework
connection to the boiler gas service cock for soundness in accordance with BS 6891.
2.
Loosen the gas inlet pressure test point screw on the gas valve (see Fig. 18). Ensure the gas supply is on and open the
boiler service cock to purge in accordance with BS 6891.
3.
Retighten the test point screw and test for gas soundness. Close the boiler gas service cock.
Fig. 17
Содержание Alpha CB50 Boiler
Страница 29: ...29 9 WIRING DIAGRAMS 9 1 ILLUSTRATED WIRING DIAGRAM Alpha CB50 Wiring Diagrams ...
Страница 30: ...30 9 2 FUNCTIONAL FLOW WIRING DIAGRAM Alpha CB50 Wiring Diagrams ...
Страница 32: ...32 Alpha CB50 Fault Finding 10 3 DOMESTIC HOT WATER Follow operational sequence ...
Страница 33: ...33 Alpha CB50 Fault Finding 10 4 FAULT FINDING SOLUTIONS A to F ...
Страница 34: ...34 Alpha CB50 Fault Finding 10 5 FAULT FINDING SOLUTION SECTIONS G to L ...