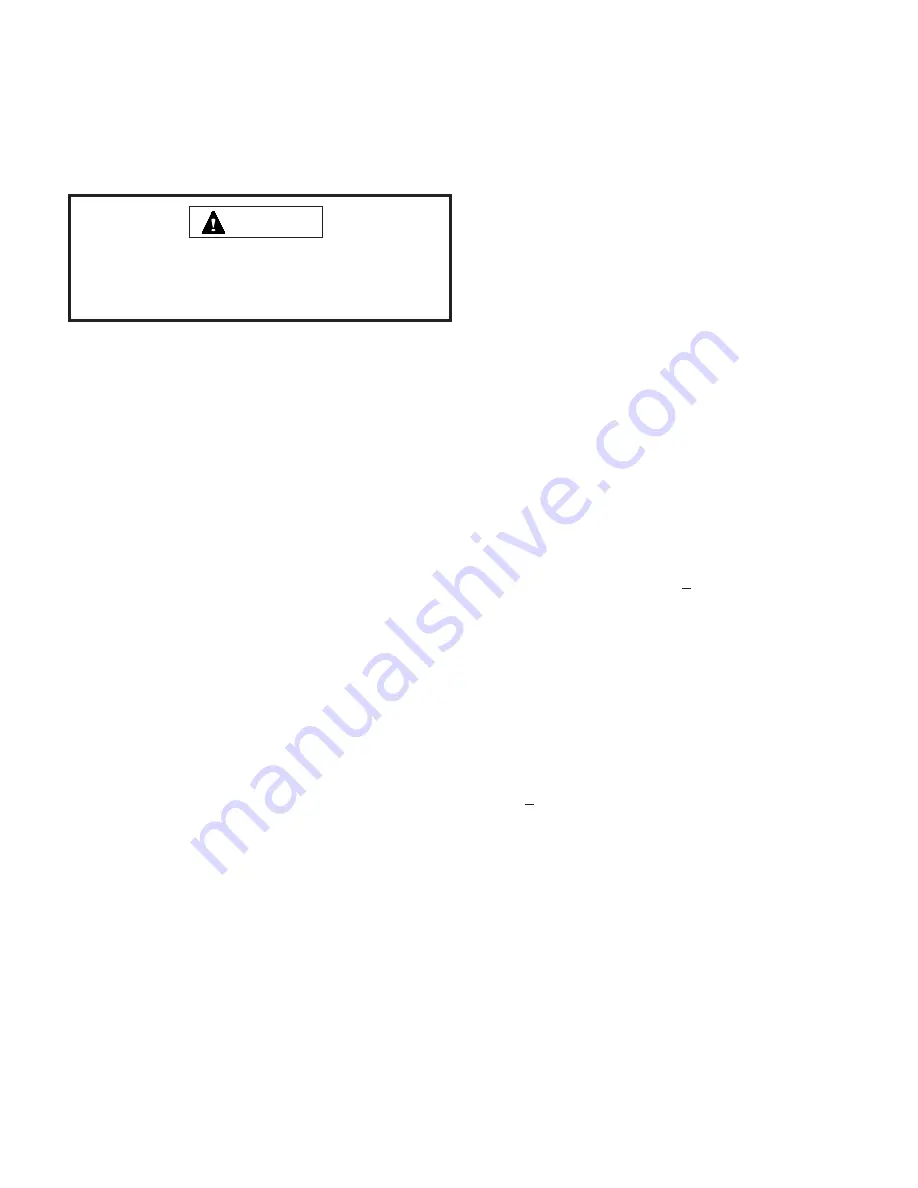
507404-02
Page 59 of 80
Issue 1448
On-Board Link W914 Dehum or Harmony (R to DS)
On-board link W914, is a clippable connection between
terminals R and DS on the integrated control. W914 must
be cut when the furnace is installed with a thermostat which
features humidity control. If the link is left intact the PMW
signal from the control will be blocked and also lead to
control damage. Refer to Table 19 for operation sequence
in applications including A80DS2V, a thermostat which
features humidity control and a single- speed outdoor Unit.
Table 20 gives the operation sequence in applications with
a two-speed outdoor unit.
On-Board Link W951 Heat Pump (R to O)
On-board link W951 is a clippable connection between
terminals R and O on the integrated control. W951 must
be cut when the furnace is installed in applications which
include a heat pump unit and a thermostat which features
dual fuel use. If the link is left intact, terminal “O” will remain
energized eliminating the HEAT MODE in the heat pump.
On-Board Links
NOTE:
In Comfort Sync™ systems with a conventional
outdoor unit (non-communicating), the on-board clippable
links must be set to properly configure the system.
On-Board Link W915 2 Stage Compr (Y1 to Y2)
On-board link W915 is a clippable connection between
terminals Y1 and Y2 on the integrated control. W915 must
be cut if two-stage cooling will be used. If the Y1 to Y2 link
is not cut, the outdoor unit will operate in second-stage
cooling only.
Diagnostic LED (Figure 26)
The seven-segment diagnostic LED displays operating
status, target airflow, error codes and other information. A
full listing of LED codes is provided in the Diagnostic Codes
Section.
Diagnostic Push Button (Figure 26)
The diagnostic push button is located adjacent to the seven-
segment diagnostic LED. This button is used to enable
the Error Code Recall “E” mode and the Flame Signal
“F” mode. Press the button and hold it to cycle through a
menu of options. Every five seconds a new menu item will
be displayed. When the button is released, the displayed
item will be selected. Once all items in the menu have been
displayed, the menu resumes from the beginning until the
button is released.
Error Code Recall Mode
Select “E” from the menu to access the most recent 10 error
codes. Select “c” from the Error Code Recall menu to clear
all error codes. Button must be pressed a second time
while “c” is flashing to confirm command to delete codes.
Press the button until a solid ”=” is displayed to exit the Error
Code Recall mode.
Flame Signal Mode
Select “F” from the menu to access the flame signal mode.
The integrated control will display the flame current on 7
segment LED in micro amps (uA).
Flame signal mode is exited after the following:
•
Power is reset
•
Pressing and holding push button until 3 horizontal lines
“=” are displayed
•
10 minutes of entering the flame sense mode.
Carefully review all configuration information provided.
Failure to properly set DIP switches, jumpers and on-
board links can result in improper operation!
WARNING
Содержание A96US2V
Страница 3: ...507404 02 Page 3 of 80 Issue 1448 EXPANDED VIEW Figure 1 ...
Страница 31: ...507404 02 Page 31 of 80 Issue 1448 Figure 38 ...
Страница 38: ...507404 02 Page 38 of 80 Issue 1448 Figure 56 TRAP DRAIN ASSEMBLY USING 1 2 PVC or 3 4 PVC ...
Страница 41: ...507404 02 Page 41 of 80 Issue 1448 Table 9 ...
Страница 45: ...507404 02 Page 45 of 80 Issue 1448 ...
Страница 47: ...507404 02 Page 47 of 80 Issue 1448 Integrated Control Figure 56 ...
Страница 78: ...507404 02 Page 78 of 80 Issue 1448 Start Up Performance Check List UNIT SET UP ...
Страница 79: ...507404 02 Page 79 of 80 Issue 1448 UNIT OPERATION Heating Mode Cooling Mode ...