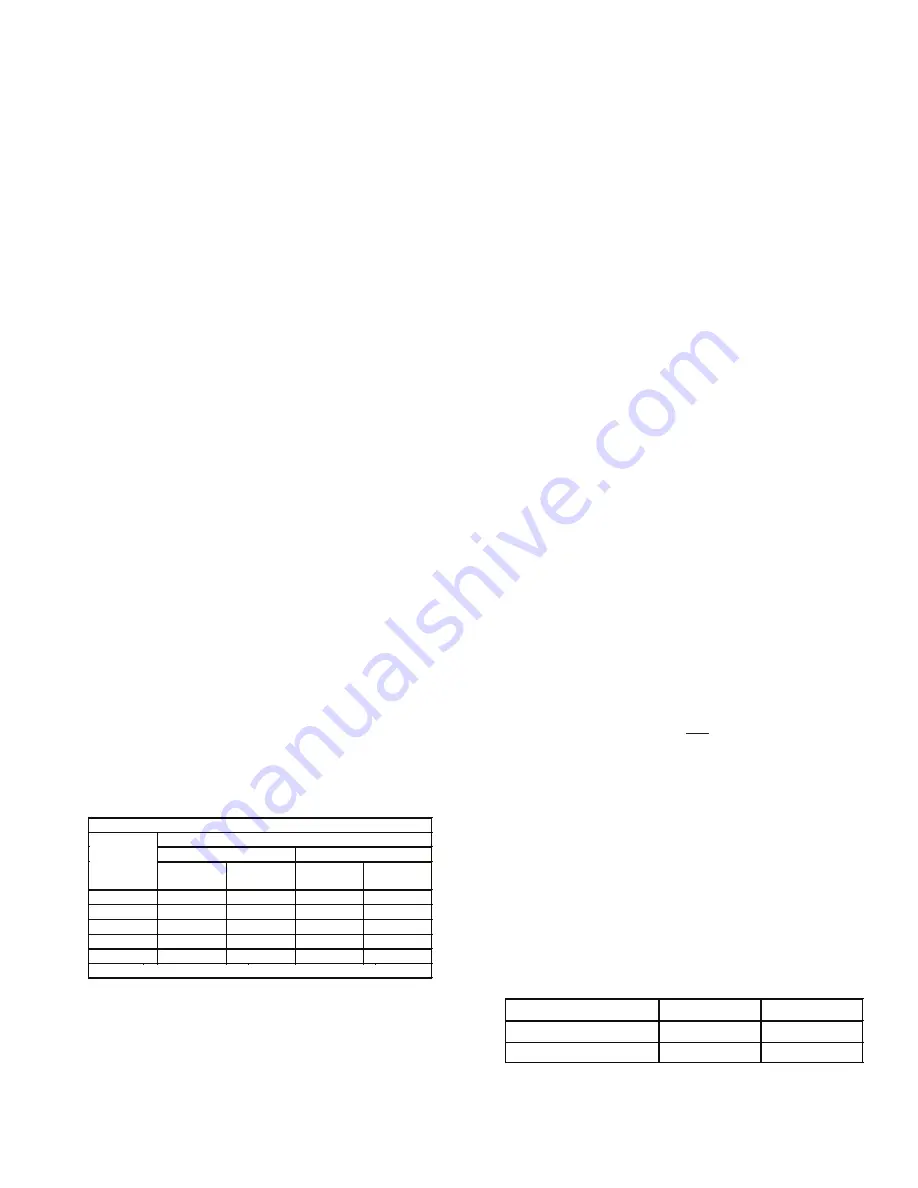
506892-01
Page 41 of 64
Issue 1251
Turning Off Gas to Unit
1.
Set the thermostat to the lowest setting.
2.
Turn
off
all electrical power to the unit if service is to be
performed.
3.
Remove the heating compartment access panel.
4.
Move gas valve switch to
OFF
position. Do
not
force.
See Figure 27 or 28.
5.
Replace the heating compartment access panel.
Failure To Operate
If the unit fails to operate, check the following:
1.
Is the thermostat calling for heat?
2.
Are access panels securely in place?
3.
Is the main disconnect switch closed?
4.
Is there a blown fuse or tripped circuit breaker?
5.
Is the filter dirty or plugged? Dirty or plugged filters will
cause the limit control to shut the unit off.
6.
Is gas turned on at the meter?
7.
Is the manual main shut-off valve open?
8.
Is the internal manual shut-off valve open?
9.
Is the unit ignition system in lock out? If the unit locks
out again, call the service technician to inspect the unit
for blockages.
10. Is pressure switch closed? Obstructed flue will cause
unit to shut off at pressure switch. Check flue and outlet
for blockages.
11. Are flame rollout switches tripped? If flame rollout
switches are tripped, call the service technician for
inspection.
Gas Flow (Approximate)
Furnace should operate at least 5 minutes before checking
gas flow. Determine time in seconds for two revolutions of
gas through the meter. (Two revolutions assures a more
accurate time.) Divide by two and compare to time in Table
20 below. If manifold pressure matches Table 22 and rate
is incorrect, check gas orifices for proper size and restriction.
Remove temporary gas meter if installed.
NOTE:
To obtain accurate reading, shut off all other gas
appliances connected to meter.
Supply Pressure Measurement
White Rodgers Valve:
An inlet post located on the gas valve provides access to
the supply pressure. See Figure 27. Back out the 3/32 hex
screw one turn, connect a piece of 5/16 tubing and connect
to a manometer to measure supply pressure. See Table 22
for supply line pressure. Tighten hex screw after
measurements have been taken.
Honeywell Valve:
A threaded plug on the inlet side of the gas valve provides
access to the supply pressure tap. Remove the threaded
plug, install a field-provided barbed fitting and connect a
manometer to measure supply pressure. See Table 22 for
supply line pressure. Replace the threaded plug after
measurements have been taken.
NOTE:
Shut unit off and remove manometer as soon as an
accurate reading has been obtained. Take care to replace
pressure tap plug.
Manifold Pressure Measurement
NOTE:
A pressure test adapter kit is available to facilitate
manifold pressure measurement.
1.
Connect test gauge to manifold pressure post tap (Figure
27) or tap (Figure 28) on gas valve.
2.
Ignite unit on high fire and let run for 5 minutes to allow
for steady state conditions.
3.
After allowing unit to stabilize for 5 minutes, record
manifold pressure and compare to value given in Table
22.
4.
If necessary, make adjustments. Figures 27 and 28
show location of high fire adjustment screw.
5.
If an adjustment is made on high fire, re-check manifold
pressure on low fire.
Do not adjust low fire manifold
pressure.
If low fire manifold pressure is more than
1/2" above or below value specified in Table 22, replace
valve.
NOTE:
Shut unit off and remove manometer as soon as an
accurate reading has been obtained. Take care to replace
pressure tap plug.
Proper Combustion
Furnace should operate minimum 15 minutes with correct
manifold pressure and gas flow rate before checking
combustion. Table 21 shows acceptable combustion for ALL
models. The maximum carbon monoxide reading should
not exceed 50 ppm.
Table 21
F iring R ate
C 02%
F o r N a t
C 02
%
F o r L
.
P .
H igh F ire
6.8 - 7
.
4
7
.
5 - 9.0
Low F ire
4
.
2 - 5.7
5
.
0 - 6.0
Table 20
G A S M E T E R C L O C K IN G C
H
A R T
S e c o n d s
f
o r O n e R e v o lu tio n
S L 2 8 0
N a tu ra l
L P
U n it
1 c u
ft
2 c u
ft
1 c u
ft
2 c u
ft
D ia l
D ia l
D ia l
D IA L
-0 4 5
8 0
1 6 0
2 0 0
4 0 0
-7 0
5 5
1 1 0
1 3 6
2 7 2
-9 0
4 1
8 2
1 0 2
2 0 4
-1 1 0
3 3
6 6
8 2
1 6 4
-1 3 5
2 7
5 4
6 8
1 3 6
N a tu ra l-1 0 0 0 b tu /c u
ft
L P -2 5 0 0 b tu /c u
ft
Содержание A80DS2V
Страница 3: ...506892 01 Page 3 of 64 Issue 1251 EXPANDED VIEW Figure 1...
Страница 24: ...506892 01 Page 24 of 64 Issue 1251 Figure 22...
Страница 25: ...506892 01 Page 25 of 64 Issue 1251 Figure 23 Optional Accessories for use with any Comfort SyncTM System...
Страница 28: ...506892 01 Page 28 of 64 Issue 1251 Table 13C Field Wiring Applications with Conventional Thermostat continued...
Страница 29: ...506892 01 Page 29 of 64 Issue 1251 Field Wiring Applications with Conventional Thermostat continued Table 13D...
Страница 30: ...506892 01 Page 30 of 64 Issue 1251 Figure 24 A80DS2V Schematic Wiring Diagram...
Страница 31: ...506892 01 Page 31 of 64 Issue 1251 Typical A80DS2V Field Wiring Diagram Figure 25...
Страница 32: ...506892 01 Page 32 of 64 Issue 1251 Integrated Control Figure 26...
Страница 50: ...506892 01 Page 50 of 64 Issue 1251 Integrated Control Diagnostic Codes...
Страница 51: ...506892 01 Page 51 of 64 Issue 1251 Integrated Control Diagnostic Codes continued...
Страница 52: ...506892 01 Page 52 of 64 Issue 1251 Integrated Control Diagnostic Codes continued...
Страница 53: ...506892 01 Page 53 of 64 Issue 1251 Integrated Control Diagnostic Codes continued...
Страница 54: ...506892 01 Page 54 of 64 Issue 1251 Integrated Control Diagnostic Codes continued...
Страница 55: ...506892 01 Page 55 of 64 Issue 1251 Program Unit Capacity Size Mode...
Страница 56: ...506892 01 Page 56 of 64 Issue 1251 Troubleshooting Heating Sequence of Operation...
Страница 57: ...506892 01 Page 57 of 64 Issue 1251 Troubleshooting Heat Sequence of Operation continued...
Страница 58: ...506892 01 Page 58 of 64 Issue 1251 Troubleshooting Heat Sequence of Operation continued...
Страница 59: ...506892 01 Page 59 of 64 Issue 1251 Troubleshooting Heat Sequence of Operation continued...
Страница 60: ...506892 01 Page 60 of 64 Issue 1251 Troubleshooting Continuous Fan Sequence of Operation...
Страница 61: ...506892 01 Page 61 of 64 Issue 1251 Start Up Performance Check List UNIT SET UP...
Страница 62: ...506892 01 Page 62 of 64 Issue 1251 Start Up Performance Check List continued...