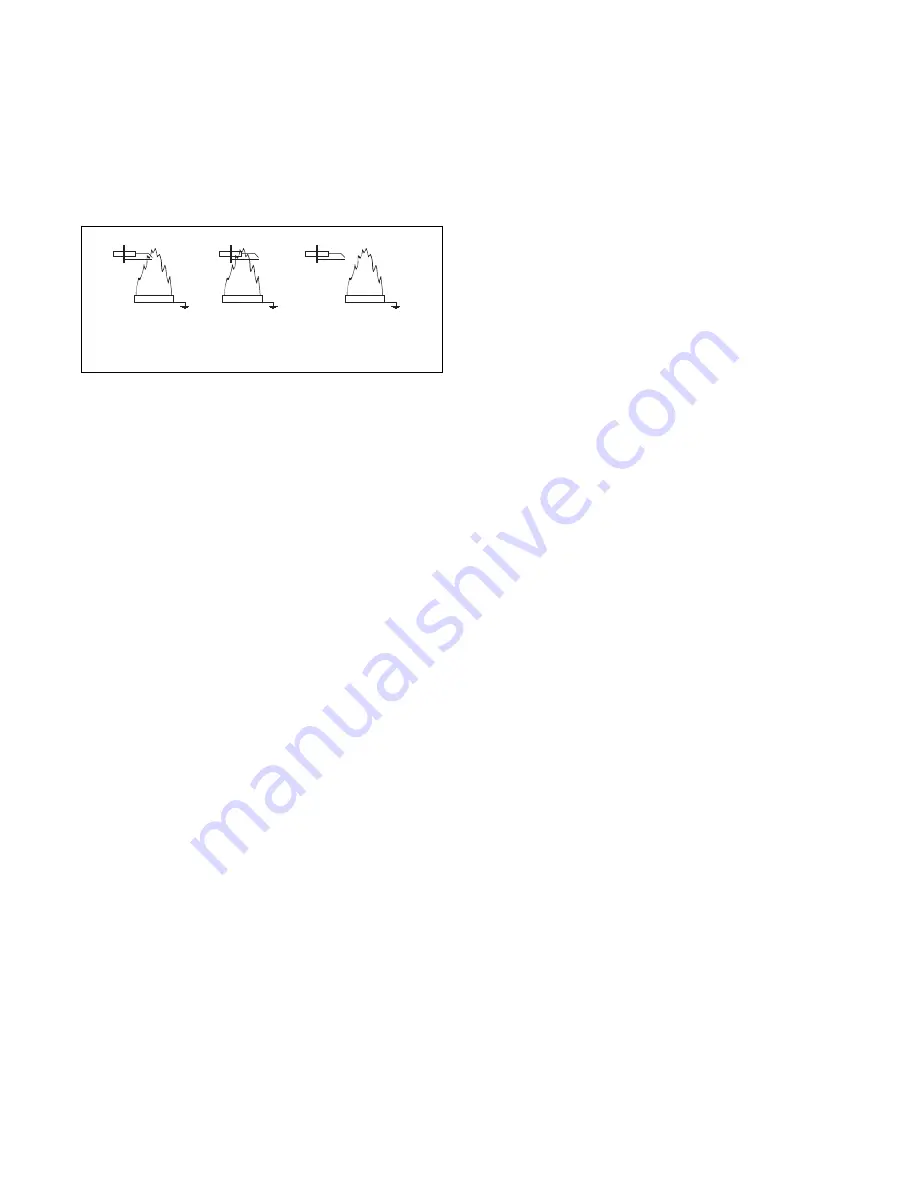
© Copyright, Alliance Laundry Systems LLC - DO NOT COPY or TRANSMIT
Operating Instructions
95
70458301ENR6
Proper Electrode Location
Proper location of the electrode assembly is important
for optimal system performance. The electrode
assembly should be located so that the tips are inside
the flame envelope and about 1/2 inch (1.2 cm) above
the base of the flame. Refer to
Figure 54
.
Flame Current Measurement
Flame current is the current that passes through the
flame from sensor to ground. To measure flame
current, connect a True RMS or analog DC micro-
ammeter to the FC+ and the FC- terminals. The
reading should be 1.0 micro-amps DC or higher. If the
meter reads negative or below “0” on the scale, the
meter leads are reversed. Re-connect leads with proper
polarity.
Alternately, a Digital Voltmeter may be used to
measure the DC voltage between the FC+ and FC-
terminals. Each micro-amp of flame current produces
1.0 VDC, so a reading of 2.6 VDC would equate to 2.6
micro-amps.
A good burner ground that matches the control ground
is critical for reliable flame sensing.
Figure 54
BURNER
YES
NO
NO
BURNER
BURNER
TMB 2317K