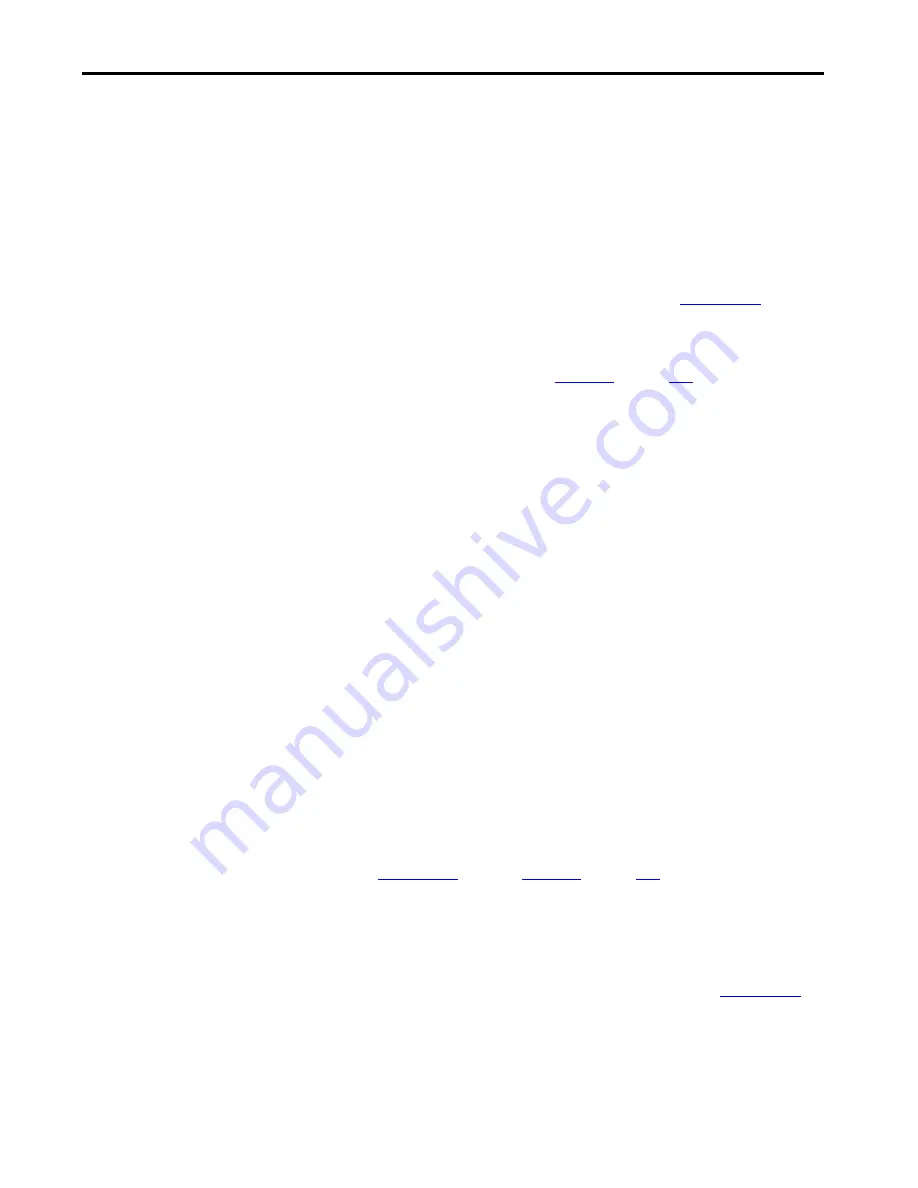
Rockwell Automation Publication 20P-TG001C-EN-P - February 2018
37
Component Test Procedures
Chapter 2
Speed Feedback Device Tests
Complete the appropriate test for the feedback device installed.
Check the Encoder
The encoder feedback device provides a dual-channel quadrature output
waveform and requires differential line-driver output at +5 or +12…15V signal
levels. DIP switch S21 on the control board controls the encoder power supply
voltage and input selection. See “DIP Switch and Jumper Settings” in the
PowerFlex Digital DC Drive User Manual, publication
). The
encoder power supply from the drive can be measured from +V (+) to
COM (-) with a digital multimeter. When S21 is set to ENC_5, the voltage
level range is +2.5…5.4V. When S21 is set to ENC_12, the voltage level range
is +5.4V…15.2V. For reference, see
on page
for a schematic
diagram.
The Channel A and Channel B are square wave type outputs that are 90° out of
phase. When rotating in the CCW direction, as viewed from the commutator
end, Channel A leads Channel B. Each differential channel has an inverted and
non–inverted signal.
Power for the encoder is provided internally. The power source provides up to
200 mA of current with a current foldback feature. If the current draw exceeds
200 mA, the current foldback feature protects the power supply. If different
power supply requirements exist for the chosen feedback device, the supply
must be provided external to the drive.
The frequency is proportional to speed and the pulse rate of the encoder,
referred to as the “Pulse/Rev” rating on the nameplate. You can calculate the
speed of the motor as:
Speed (RPM) = [Frequency (Hz) x 60]/[Pulses/Revolution].
Check the DC Tachometer
• Verify that DIP switch S4 on the control board is set to the correct input
voltage of the DC analog tachometer. See “DIP Switch and Jumper
Settings” in the PowerFlex Digital DC Drive User Manual, publication
. Also, see
on page
for a circuit diagram.
• The analog tachometer signal is fine scaled using parameter 562 [Anlg
Tach Gain].
• See “Drive Reference and Feedback Scaling” in Appendix C of the
PowerFlex Digital DC Drive User Manual, publication
for more information.