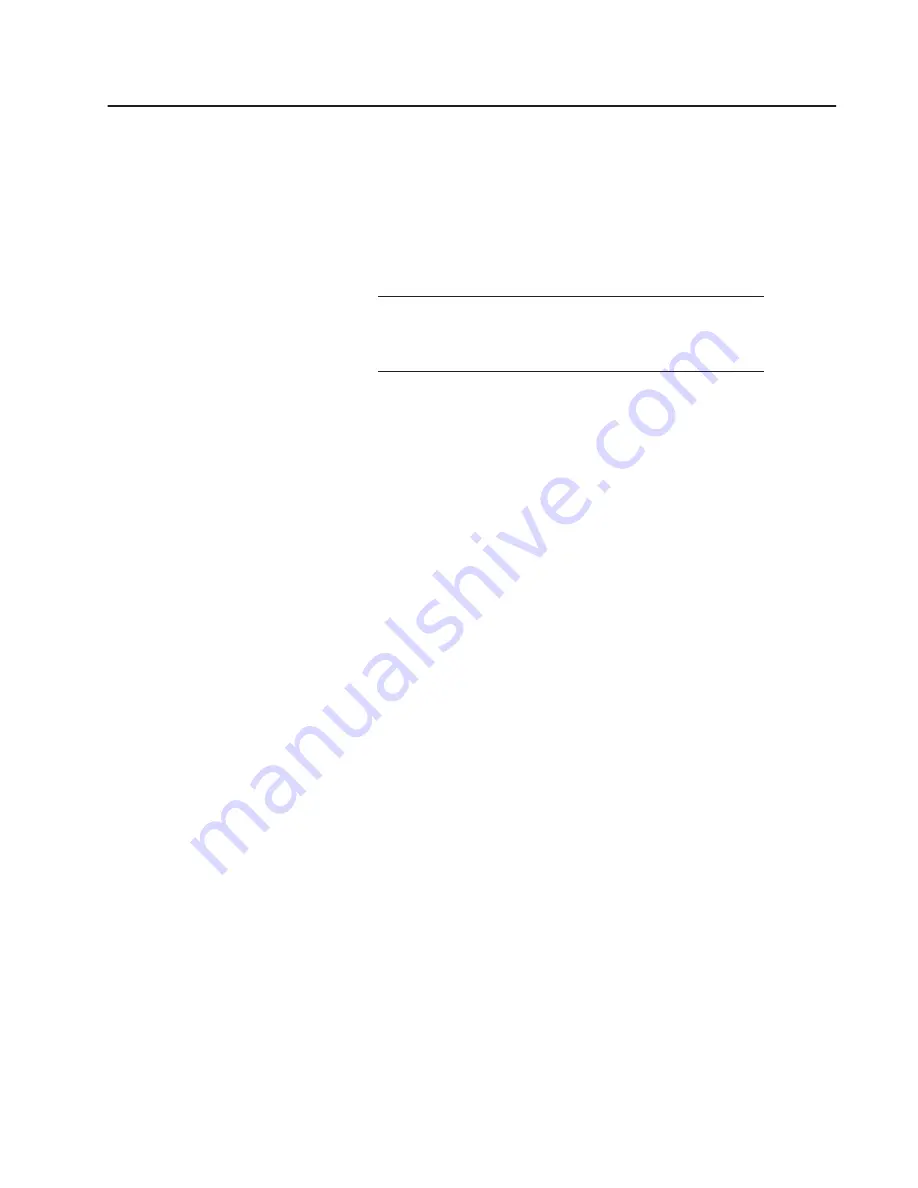
Chapter
1
Publication 1794-6.5.15 – December 1998
Read this chapter to familiarize yourself with the 1794–ID2 module.
For information on
See page
How You Use the incremental encoder Module . . . . . . . . . . . 1–1
What the incremental encoder Module Does . . . . . . . . . . . . . 1–2
Input Capabilities . . . . . . . . . . . . . . . . . . . . . . . . . . . . . . . . 1–3
How the incremental encoder Operates . . . . . . . . . . . . . . . . . 1–4
The 1794–ID2 module is an intelligent I/O module designed to
perform high speed pulse counting. The module provides:
•
2 pulse transmitter interfaces, each with 4 optocoupled inputs
Each input has + and – inputs for connection to transmitters with
complementary and noncomplementary signals.
The pulse inputs can accept frequencies up to 100KHz. The module
accepts and returns binary data.
The module’s primary use is accurate, high-speed counting of pulse
from pulse transmitters or incremental encoders with 1 or 2 pulse
trains. This includes quantity counting, positioning and speed
calculations.
The module has 2 up/down counters, each individually
programmable. The number of edges to be counted can be multiplied
by 1, 2 or 4 (x1, x2, x4). Pulse transmitters can be complementary or
noncomplementary.
What This Chapter
Contains
How You Use the
Incremental Encoder
Module
Содержание FLEX I/O 1794-ID2
Страница 6: ...Using This Manual P 4 Publication 1794 6 5 15 December 1998 ...
Страница 10: ...Table of Contents iv Publication 1794 6 5 15 December 1998 ...
Страница 20: ...1 10 Overview of the Incremental Encoder Module Publication 1794 6 5 15 December 1998 ...
Страница 74: ...7 4 Calibrating Your Incremental Encoder Module Publication 1794 6 5 15 December 1998 ...