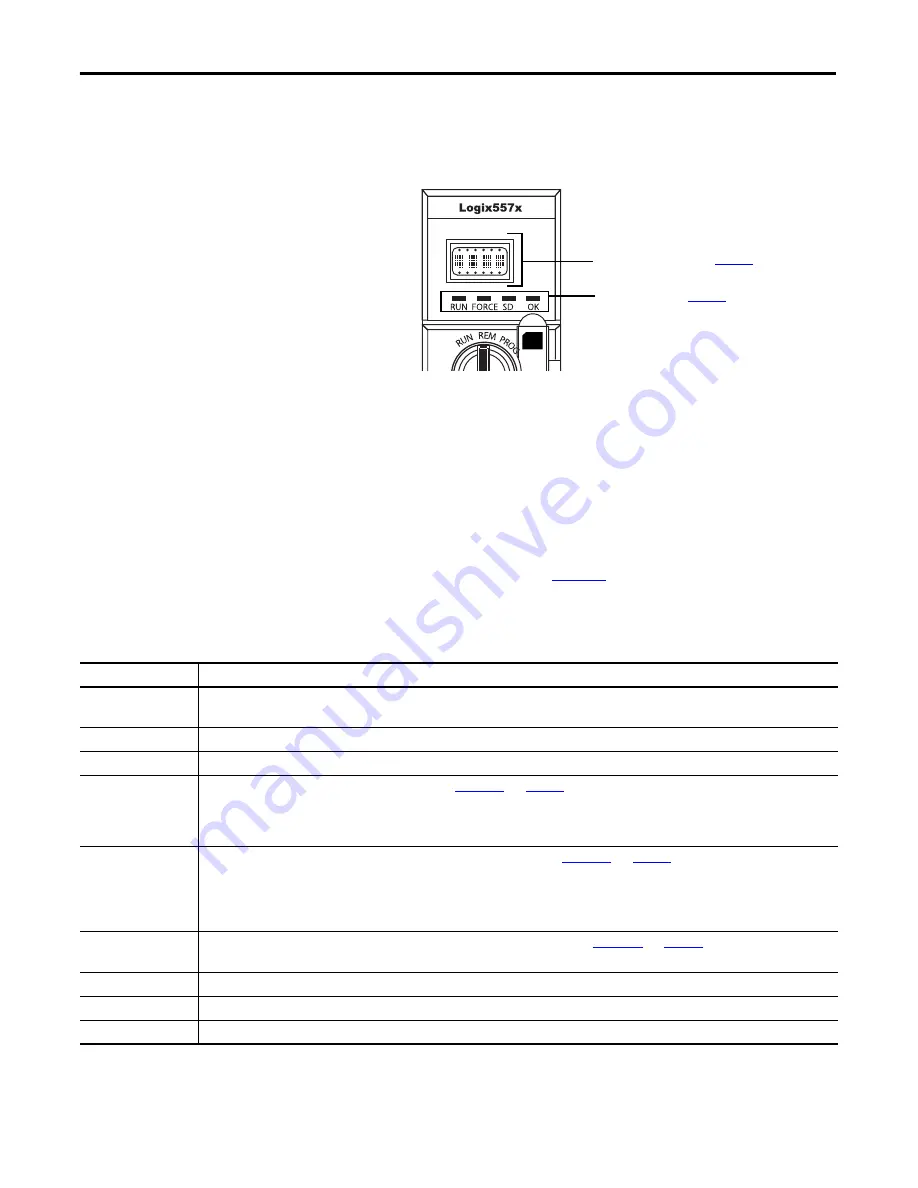
186
Rockwell Automation Publication 1756-UM001O-EN-P - October 2014
Appendix A
Troubleshoot the Module
1756-L7
x
Controller Status
Display and Indicators
The 1756-L7
x
controllers have four status indicators and one four-character
scrolling status display.
Figure 47 - 1756-L7
x
Status Display and Indicators
1756-L7
x
Controller
Status Display
The 1756-L7
x
controller status display scrolls messages that provide information
about the firmware revision, ESM status, project status, and major faults of the
controller.
General Status Messages
The messages that are described in
are typically indicated upon
powerup, powerdown, and while the controller is running to show the status of
the controller and the ESM.
Scrolling Status Display, see
Status Indicators, see
Table 48 - General Status Messages
Message
Interpretation
No message is indicated
The controller is Off.
Check the OK indicator to determine if the controller is powered and determine the state of the controller.
TEST
The controller is conducting power-up tests.
PASS
Power-up tests have been successfully completed.
SAVE
A project is being saved to the SD card. You can also view the
(see
) for more status information.
Allow the save to complete before:
•
removing the SD card.
•
disconnecting power.
LOAD
A project is being loaded from the SD card at controller powerup. You can also view the
(see
) for more status information.
Allow the load to complete before doing the following:
•
Removing the SD card
•
Disconnecting power
•
Removing the ESM module
UPDT
A firmware upgrade is being conducted from the SD card upon powerup. You can also view the
) for more status information.
If you do not want the firmware to update upon powerup, change the Load Image property of the controller.
CHRG
The capacitor-based ESM is being charged.
1756-L7
x
/
X
The controller catalog number and series.
Rev
XX
.
xxx
The major and minor revision of the firmware of the controller.
Содержание 1756-L63XT
Страница 4: ...4 Rockwell Automation Publication 1756 UM001O EN P October 2014 Summary of Changes Notes...
Страница 18: ...18 Rockwell Automation Publication 1756 UM001O EN P October 2014 Preface Notes...
Страница 78: ...78 Rockwell Automation Publication 1756 UM001O EN P October 2014 Chapter 3 Start Using the Controller Notes...
Страница 126: ...126 Rockwell Automation Publication 1756 UM001O EN P October 2014 Chapter 7 Manage Controller Communication Notes...
Страница 136: ...136 Rockwell Automation Publication 1756 UM001O EN P October 2014 Chapter 8 I O Modules...
Страница 168: ...168 Rockwell Automation Publication 1756 UM001O EN P October 2014 Chapter 10 Develop Applications Notes...
Страница 182: ...182 Rockwell Automation Publication 1756 UM001O EN P October 2014 Chapter 12 Redundant Systems Notes...
Страница 210: ...210 Rockwell Automation Publication 1756 UM001O EN P October 2014 Index Notes...
Страница 211: ......