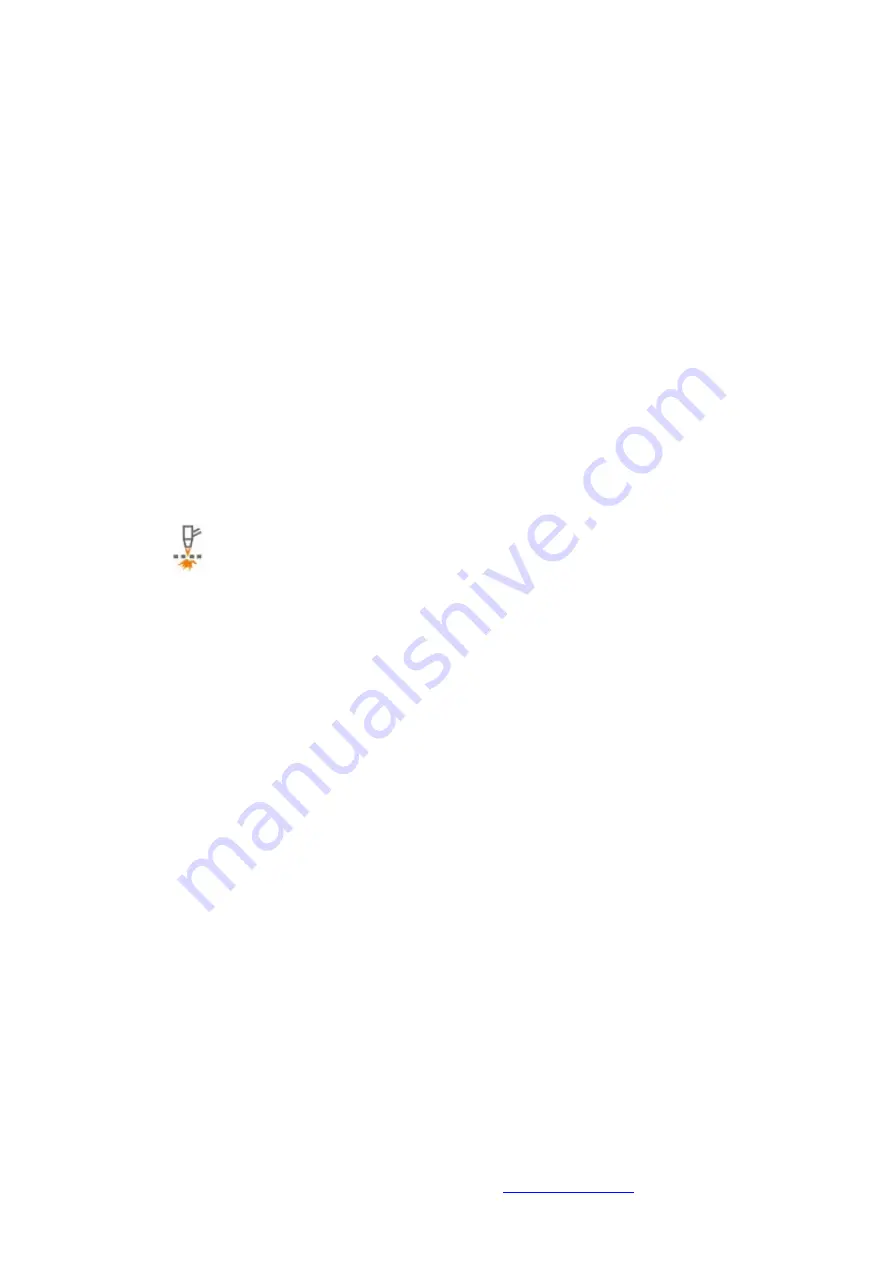
25/32
ALFA IN a.s ©
www.alfain.eu
5. Use the quick connectors to connect the compressed air to the
A6
connector on the back of the machine.
6. Set the pressure with encoder
V1
to 5.5 bar for cutting and 4.8 bar for
grooving.
7. When the
A8
main switch is turned on, the display lights up.
8. Connect the earth cable to the quick coupler
A1
and the cut material pliers.
9. Check the inlet air pressure and adjust if necessary. It must not be higher
than 8.5 bar and not lower than 6.5 bar.
10.
Set the potentiometer of the cutting current size control to the value
corresponding to the material to be cut.
11.
Depending on the selected cutting stream size, set the torch with the
appropriate cutting tip diameter.
12.
Press the button on the torch handle, the pre-blowing starts for 1 s.
13.
Pilot arc ignites.
14.
Move the torch to the material, the pilot arc turns into a cutting arc. If
you do not start cutting within two seconds, the arc will go out. If the torch
is moved away from the material while cutting, the arc will go out. If the
machine is in the gap material cutting mode - see the corresponding
V5
icon
on the control panel, the cutting arc will change to a pilot arc and
if you do not start cutting within 2 seconds, this arc will go out.
15.
Stop cutting by releasing the button on the torch handle.
9. HAND CUTTING
1. Pressing the torch button ignites the pilot arc. The torch must then be
immediately attached to the material to be cut. At this point, the main arc
between the torch and the material being cut starts to burn.
2. It is necessary to move the torch at a uniform speed by pulling the nozzle
directly over the material, its value depends on the thickness and type of
material to be cut and the size of the cutting current. We recommend to
test first.
3. Metal cutting can be carried out in all possible positions (horizontal,
horizontal, overhead, vertical ascending and descending and also across
in the above positions) if the appropriate parameters are selected,
however, if possible, a horizontal cut is preferred. In other positions, the
operator is at increased risk from flying droplets of molten material.
4. If possible, we recommend starting at the edge of the material. In case you
are cutting a hole or need to start from the centre of the material, tilt the
torch head slightly and gradually straighten it to a vertical position so that
the spraying material does not block the cutting tip, (see Fig. 11) This
working procedure must always be followed if the thickness of the material
to be cut exceeds 3 mm.
5. If the cut is made in a corner or angle (see Fig. 12), we recommend using
an extended electrode and cutting tip. However, the lower cutting power