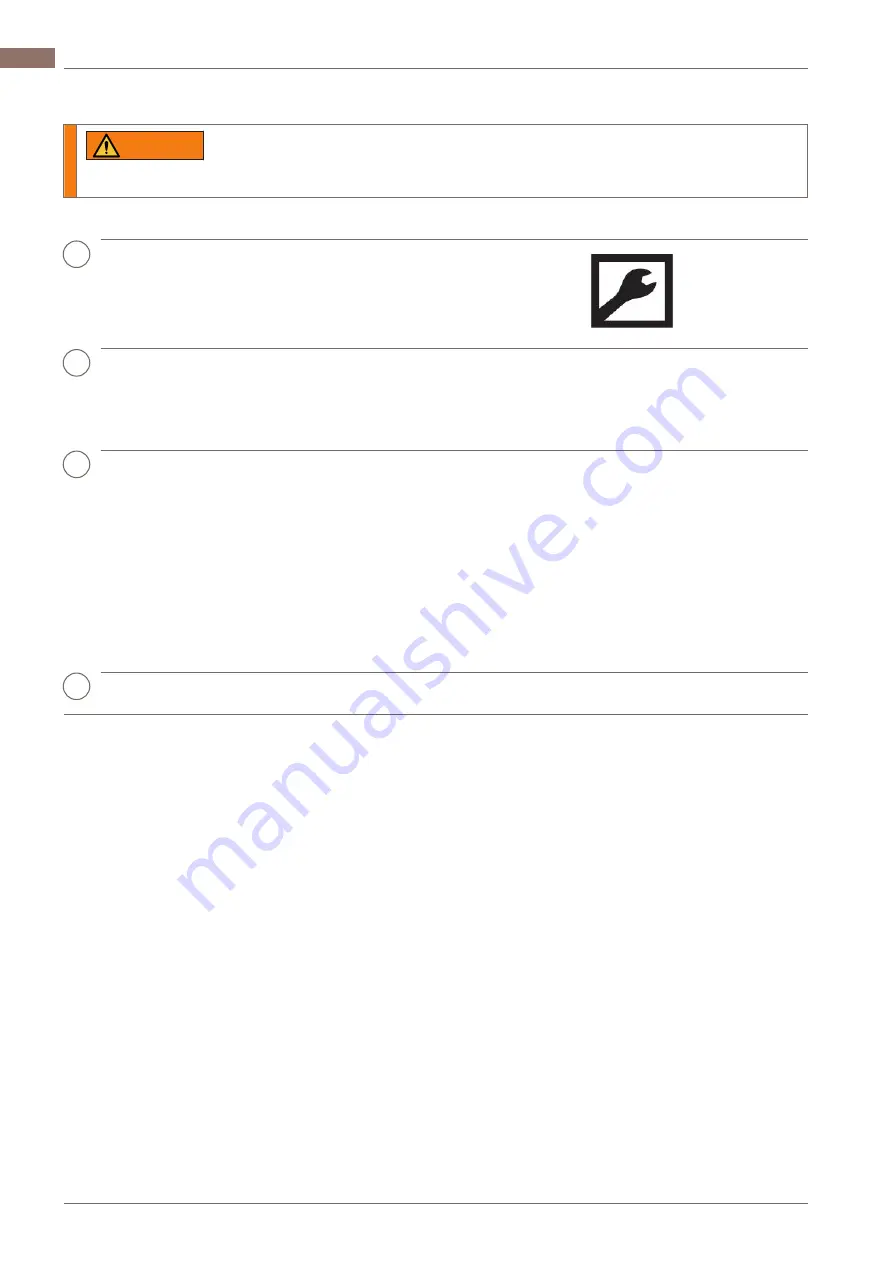
9.4 Filling the pump via the suction or pressure connection
WARNING
Danger of injury or poisoning through dangerous pumped liquids.
Collect the emitted pumped liquid safely and dispose of it in an environmentally compatible manner.
1
Open the vent hole
3
so that the air can
escape during the filling process.
2
Open the suction- or pressure-side shut-off
device and fill the pump via the suction or
pressure connection until pumped liquid is
emitted at the vent hole.
3
During the filling process turn the pump shaft
or the fan impeller of the motor by hand to
speed up the filling process:
• Filling via suction connection
1
: Turn the
pump shaft in the direction of rotation of
the motor.
• Filling via pressure connection
2
: Turn the
pump shaft against the direction of rotation
of the motor.
4
Close the vent hole.
200007725-1-EN-GB
42
9 Operation
EN
Содержание ALP 100
Страница 6: ......
Страница 8: ...200007725 1 EN GB 8 1 Warning signs in text EN Safety...
Страница 10: ...200007725 1 EN GB 10 2 About this document EN...
Страница 14: ...200007725 1 EN GB 14 3 Safety EN Safety...
Страница 21: ...200007725 1 EN GB 21 Technical data 5 EN...
Страница 24: ...200007725 1 EN GB 24 5 Technical data EN...
Страница 32: ...200007725 1 EN GB 32 7 Transportation Storage and Disposal EN...
Страница 38: ...200007725 1 EN GB 38 8 Installation removal and connection EN...
Страница 66: ...200007725 1 EN GB 66 11 Troubleshooting EN...
Страница 72: ...200007725 1 EN GB 72 12 Spare Parts EN...
Страница 77: ...14 EC Declaration of conformity 200007725 1 EN GB 77 EN...