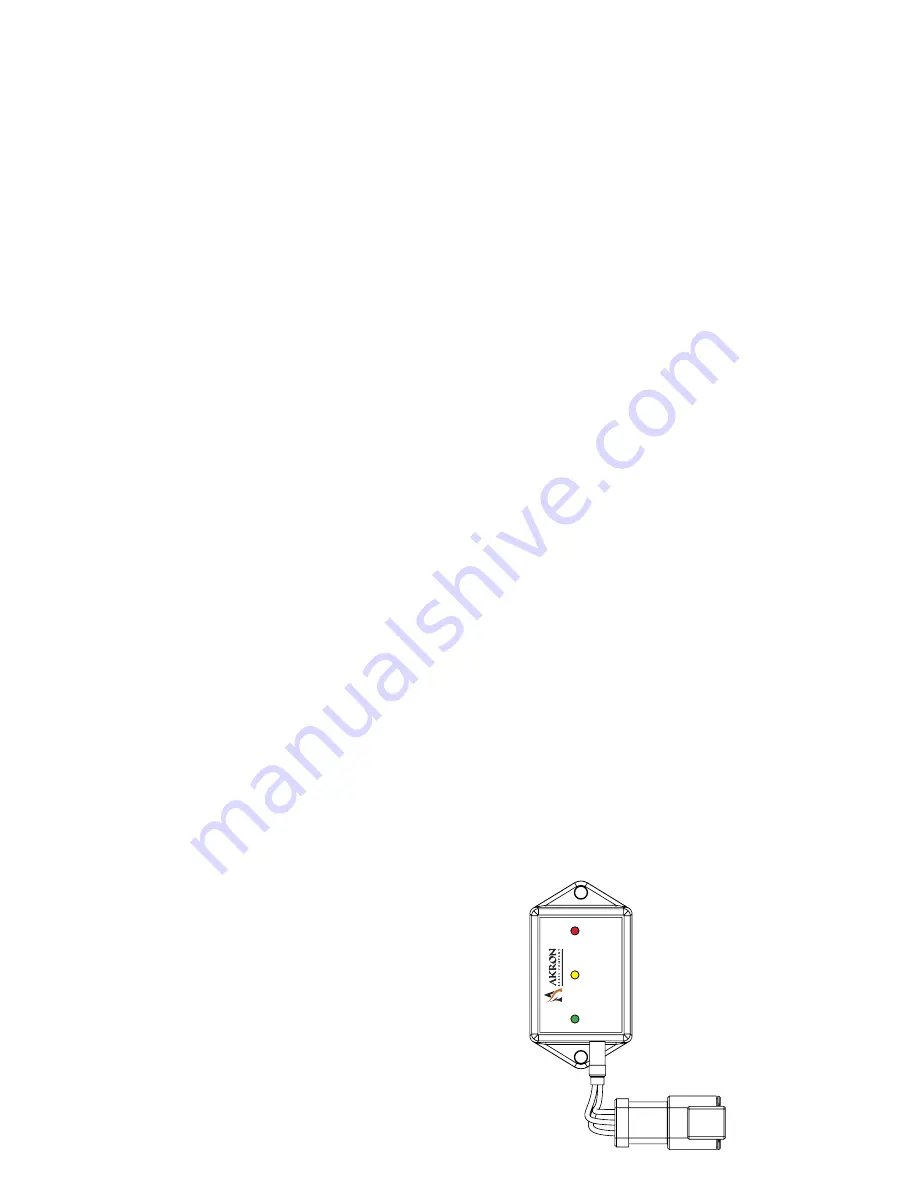
Page 11
(Setup Continued)
1. If further programming is needed, turn system power off, press and hold the “Stream” switch and turn system
power back on. Within a few seconds, the LED on the control panel will begin to blink once approximately
every three seconds.
2. To program a new deploy position, momentarily press the “Deploy” switch. The monitor will proceed to the
default deploy position and stop. The LED on the control panel will be blinking a code of 1-6 meaning you are
in deploy setup mode. After the monitor stops, use right/left/raise/lower controls to position the monitor nozzle
to the desired deploy position.
3. When the nozzle is in the desired position, you can save it by pressing either the “Stream” or “Fog” switches.
If you use the “Stream switch” the nozzle will go to the stream position during deploy. If you use the “Fog”
switch, the nozzle will go to the fog position during deploy.
4. Once the position has been saved, the LED on the control panel will go back to blinking once every three
seconds. From this point, you can reset the UII logic box by momentarily pressing the fog switch and it will
reboot into normal operation mode or continue to step 5 to program the stow position.
5. To program a new stow position, momentarily press the “Stow” switch. The monitor will proceed to the default
stow position and stop. The LED on the control panel will be blinking a code of 1-5 meaning you are in stow
setup mode. Only the nozzle elevation can be set for the stow function. Use the “Raise” or “Lower” controls to
move the nozzle to the desired position.
6. When the nozzle is in the desired position, you can save it by pressing either the “Stream” or “Fog” switches.
If you use the “Stream switch” the nozzle will go to the stream position during stow. If you use the “Fog”
switch, the nozzle will go to the fog position during stow.
7. Once the position has been saved, the LED on the control panel will go back to blinking once every three
seconds. From this point, you can reset the UII logic box by momentarily pressing the fog switch and it will
reboot into normal operation mode or continue to step 2 below to program the Home position.
POSITION SENSORS
The DeckMaster monitor has been provided with two potentiometers and a Swing Arm Sensor. The two potentiometers
measure the position of the elevation and rotation. The “Home” position is set at the factory for the middle of the
rotation range and coincides with the monitor facing the forward physical position (in line with the vertical groove on
the outside diameter of the mounting flange). The home position can be adjusted to allow the monitor to stow at any
rotational position between the rotational stops. The Swing Arm Sensor determines which position the Swing Arm
(center elbows) are in, Stowed, Deployed or somewhere in between. It puts out a different signal for each of the three
positions that the logic box uses for proper sequencing and error reporting. These signals are also visible as different
colored LED’s on the face of the sensor. See figure below.
To Adjust the Home Position:
1. Enter the setup mode. See instructions above for entering the setup mode.
2. Using the “Stream switch, advance to setup code 2-7.
3. Operate unit left or right to desired Home position.
4. Press the “Fog” switch to store the Home position.
5. Cycle power on to the Universal II Controller. The monitor will now stow at the new Home position.
RAISED
LOWERED
(Red)
(Yellow)
(Green)
Swing Arm
Senser