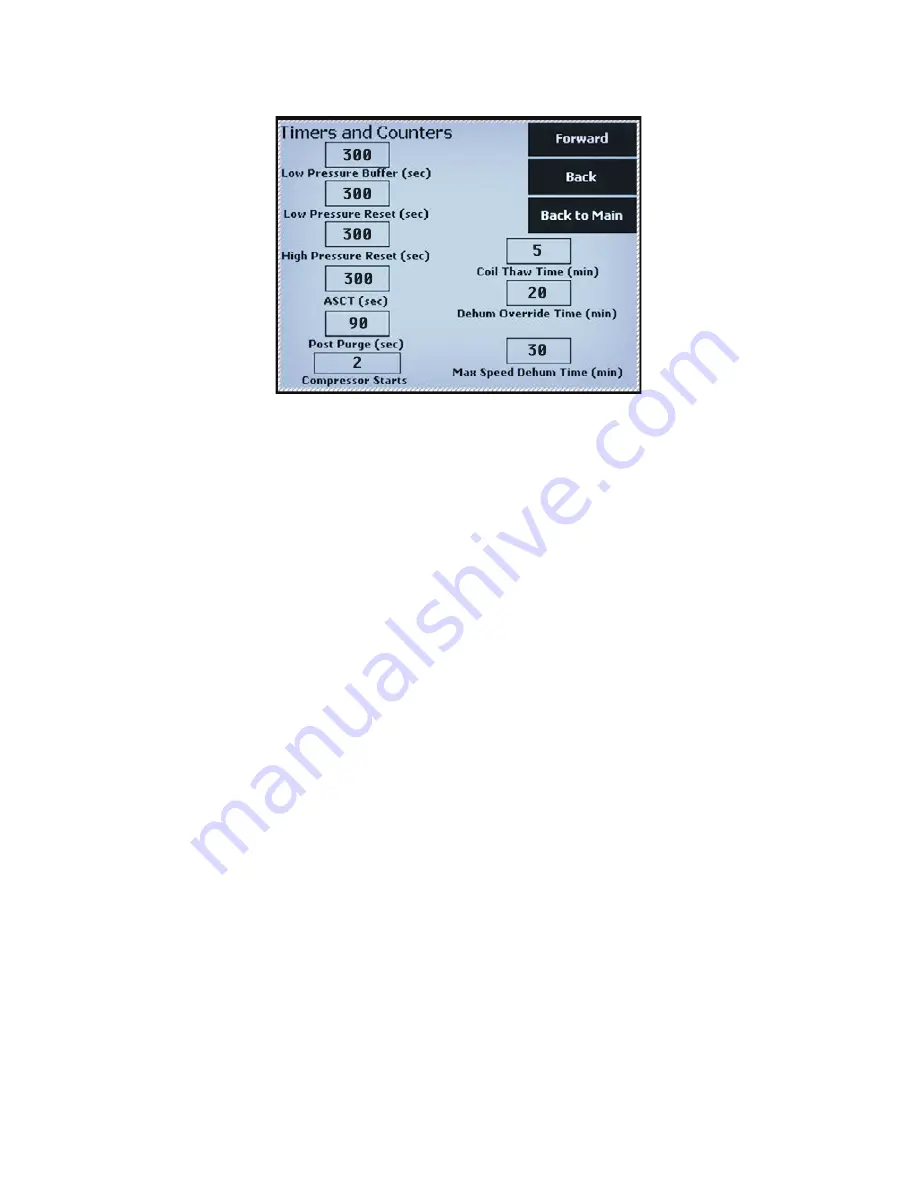
63
Scholar V VAIVA Maintenance & Service Manual 10/2017 Rev.2
7. SCREEN 7: Timers and Counters
(Changes require username/password)
a. Low Pressure Buffer (sec)
: This is the time in seconds between when the low
refrigerant switch opens due to a low pressure fault and when the PLC shuts off
the compressor.
b. Low Pressure Reset (sec)
: This is the time in seconds until the low refrigerant
lockout resets automatically. The lockout will automatically reset two times. A third
lockout will require a manual reset by pushing the Fault Reset button shown on
Screen 1 (Main Screen).
c. High Pressure Reset (sec)
: This is the time in seconds until the high refrigerant
lockout resets automatically. The lockout will automatically reset two times. A third
lockout will require a manual reset by pushing the Fault Reset button shown on
Screen 1 (Main Screen).
d. ASCT (sec)
: ASCT stands for Anti Short Cycle Timer. This timer starts timing when
the compressor turns off and prohibits it from running again until the time period
elapses.
e. Post Purge (sec)
: This is a timer which runs the indoor blower a specific time after
the compressor shuts off. The purpose is to allow the room air flow to extract any
cooling or heating benefit from the refrigerant stored in the indoor coil. This is only
active if the Blower Auto mode is chosen on Screen 1 (Main Screen).
f. Coil Thaw Time (min)
: A freeze stat is located in contact with the fins of the indoor
coil. This device is set for about 30°F and stops the compressor operation for the
stated time period if the coil begins to ice up. This is not a normal condition and
should only happen infrequently, if ever. During this compressor off period, the
blower remains on in an effort to thaw any ice accumulation on the coil. There are
two auto reset attempts before a lock out that requires a manual reset.
g. Dehumid Override Time (minutes)
: During normal cooling, if the humidity set-
point has not been achieved in this time setting, the compressor speed is driven to
maximum cooling allowed. If this action should drive the room temperature below
the cooling control band (See Shutoff Diff, Screen 4, Differentials and Deadbands),
the dehumidification mode becomes active with hot gas reheat heating the supply
air to the set-point to keep from overcooling the room.
h. Max. Speed Dehum.
Time:
This is the time that the compressor will run at
maximum speed in an attempt to de-humidify. When the time expires, the Dehum
Override timer is reset and the system resumes normal operation.
i. Compressor Starts Since Reset:
This is the number of times the compressor has
started since the Fault Reset button was last pressed on Screen 1 (Main Screen).