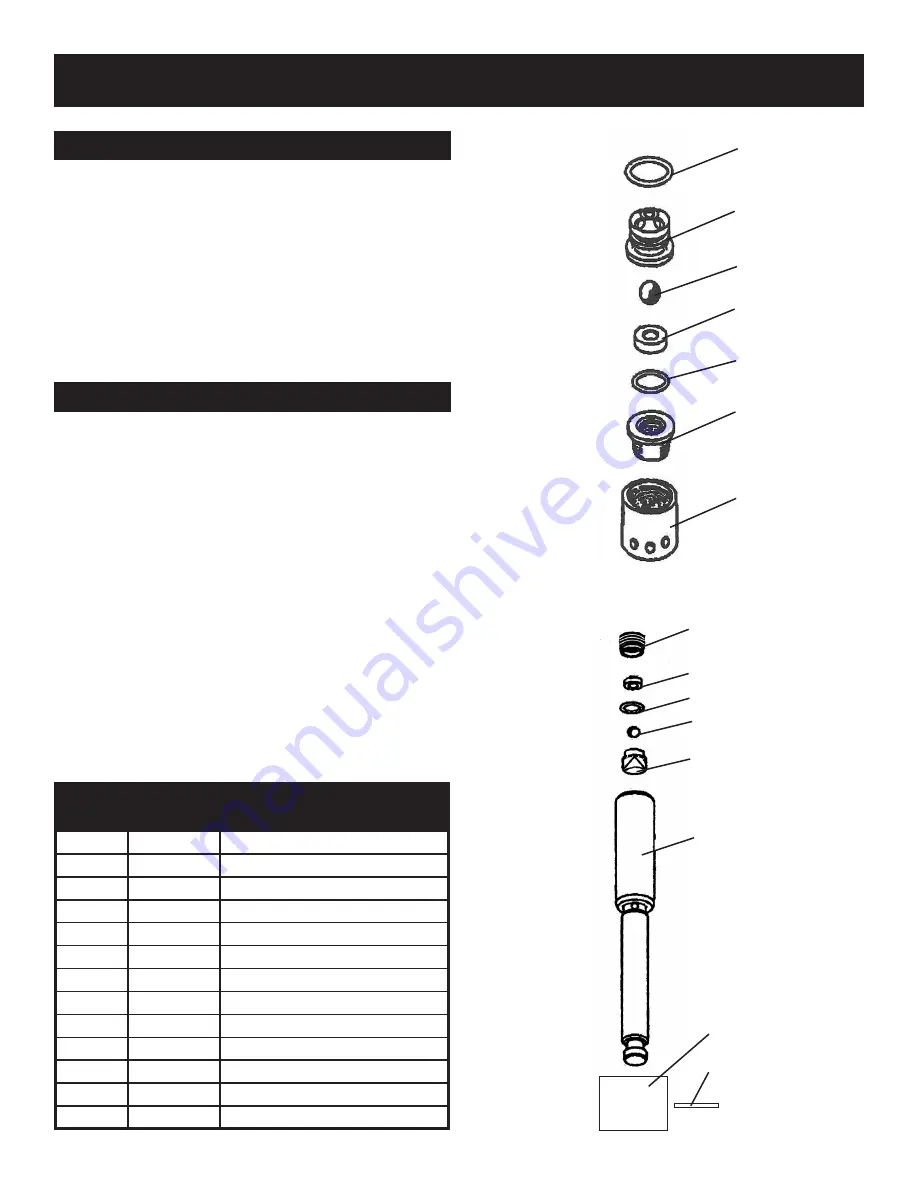
16
17
DISASSEMBLY OF THE OUTLET VALVE
FIG. 19
FIG. 20
2
5
4
1
3
6
7
187-248
187-250
13
10
12
8
9
11
SERVICING INLET & OUTLET VALVES
1. Using the rod collar tool (189-211) , screw the suction
nut, containing intake seat support, off of the fluid body.
See Fig. 19.
2. Remove the inlet seat, O-ring, inlet
ball and inlet retainer with O-ring. See Fig. 19.
3. Clean all parts and inspect them for wear or damage,
replacing parts as needed. Old O-rings should be
replaced with new ones.
NOTE: INLET SEAT (187-065) IS REVERSIBLE.
4. Clean inside of fluid body.
5. Reassemble the valve and screw it onto the fluid body if
no further service is needed.
1. Complete all steps of the Fluid Pump Disconnect
procedure on page 16.
2. Screw the suction nut off the pump and remove inlet
valve assembly.
3. Using the rod collar tool, loosen the packing nut and
push the piston down and out of the fluid body.
4. Place piston holder (187-248) in a vise. Slide piston
into holder and lock in place with a 1/4" pin (187-250).
5. Clean all parts and inspect them carefully for wear or
damage. Inspect the outside of the piston rod for scoring
or wear. Replace these parts if needed. A worn piston
rod will cause premature wear of packings.
6. Using 3/8" allen wrench to unscrew retainer from piston.
7. Remove outlet seat, O-ring, outlet ball and outlet retainer.
8. Inspect outlet ball and seat for wear. Replace as
required.
NOTE: OUTLET SEAT (187-061) IS REVERSIBLE.
9. Install parts back into piston rod as per Fig. 20. Place
two drops of loctite No. 242 (blue) on threads of the
retainer before assembling and torque to 20 ft-lbs.
SERVICING THE OUTLET VALVE
PARTS LIST FIGURE 19 & 20
Item No.
Part No.
Description
1
106-014
Black O-Ring
2
187-016
Inlet Retainer
3
187-020
Inlet Ball
4
187-065
Inlet Seat
5
106-017
White O-Ring
6
187-001
Suction Fitting
7
187-002
Suction Nut
8
187-051
Retainer
9
187-061
Outlet Seat
10
106-021
White O-Ring
11
115-022
Outlet Ball
12
187-062
Outlet Retainer
13
187-330-99 Piston