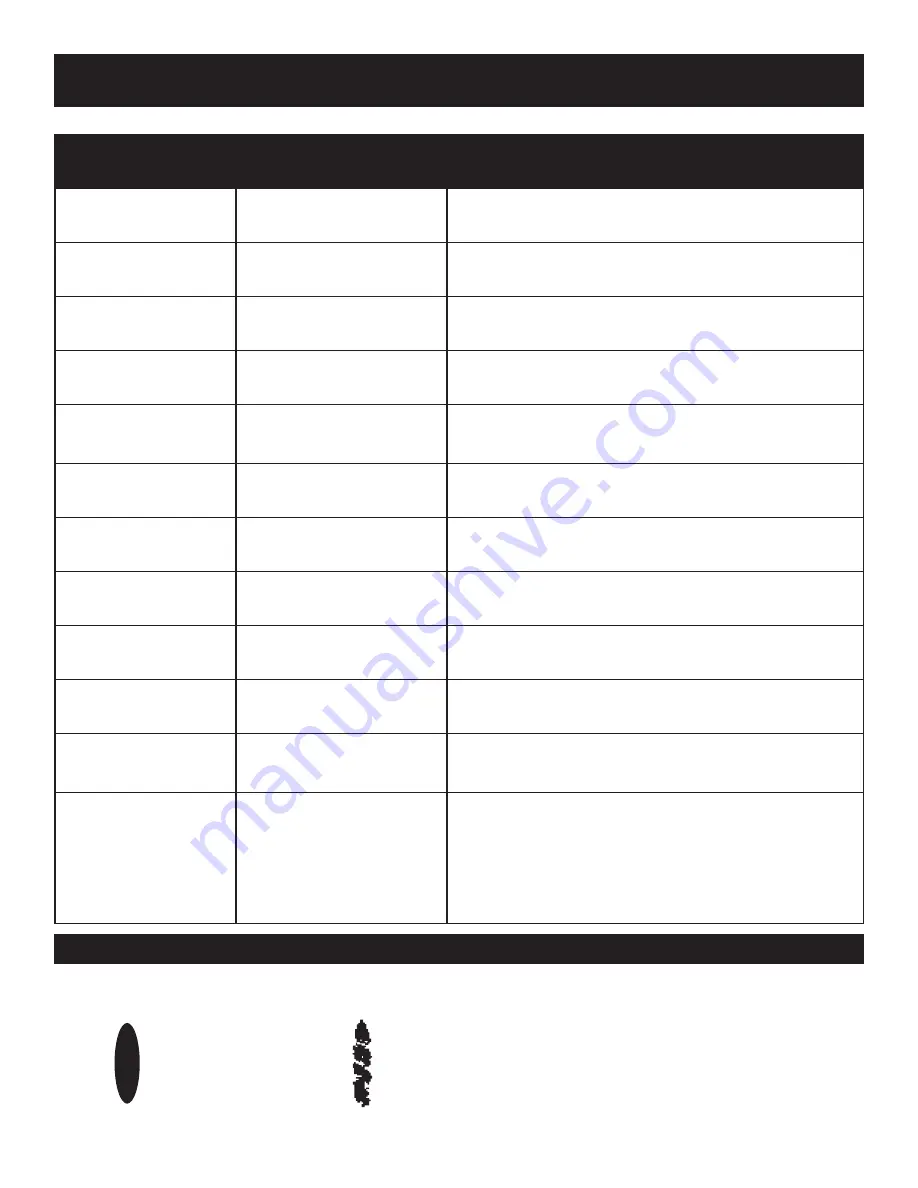
12
13
AIRLESS SPRAY TROUBLESHOOTING
DEFECTS
CAUSE
CORRECTION
Coarse spray
Low pressure
Increase the pressure
Excessive fogging
(overspray)
High pressure
Material too thin
Reduce the pressure to satisfactory pattern distrabution
Use less thinner
Patten too wide
Spray angle too large
Use smaller spray angle tip
Pattern too narrow
Spray angle too small
use larger spray angle tip ( if coverage is OK, try tip in same
nozzle group)
Too much material
Nozzle too large
Material too thin
Pressure too high
use smaller nozzle
reduce pressure
Too little material
Nozzle too small
use next larger nozzle
material too thick
Thin distribution in center
of pattern “horns”
Worn tip
Wrong tip
change to new tip
use nozzle with narrow spray angle
Thick skin on work
Material too viscous
Application too heavy
thin cautiously
reduce pressure and/or use tip in next smaller nozzle group
Coating fails to close &
smooth over
Material too viscous
thin cautiously
Spray pattern irregular,
deflected
Orifice clogged
Tip damaged
clean carefully
replace with new tip
Craters or pock marks,
bubbles on work
Solvent balance
use 1 to 3% “short solvents remainder “long” solvents
(this is most likely to happen with material of low viscosity,
lacquers, etc.)
Clogged screens
Extraneous material in paint
Course pigments
Poorly milled pigments
(paint pigments glocculate)
Clean screen
Use coarse screen if orifice size allows.
Use courser screen, larger orifice tips. Obtain ball milled
paint. If thinner has been added, test to see if a cover
screen. Incompatible drop placed on top of paint mixes or
flattens out on the paint mixture & thinners on the surface. If
not, try different thinner in fresh batch of paint.
TEST THE PATTERN
SPOTTY PATTERN, INCREASE PRESSURE
GOOD, FULL