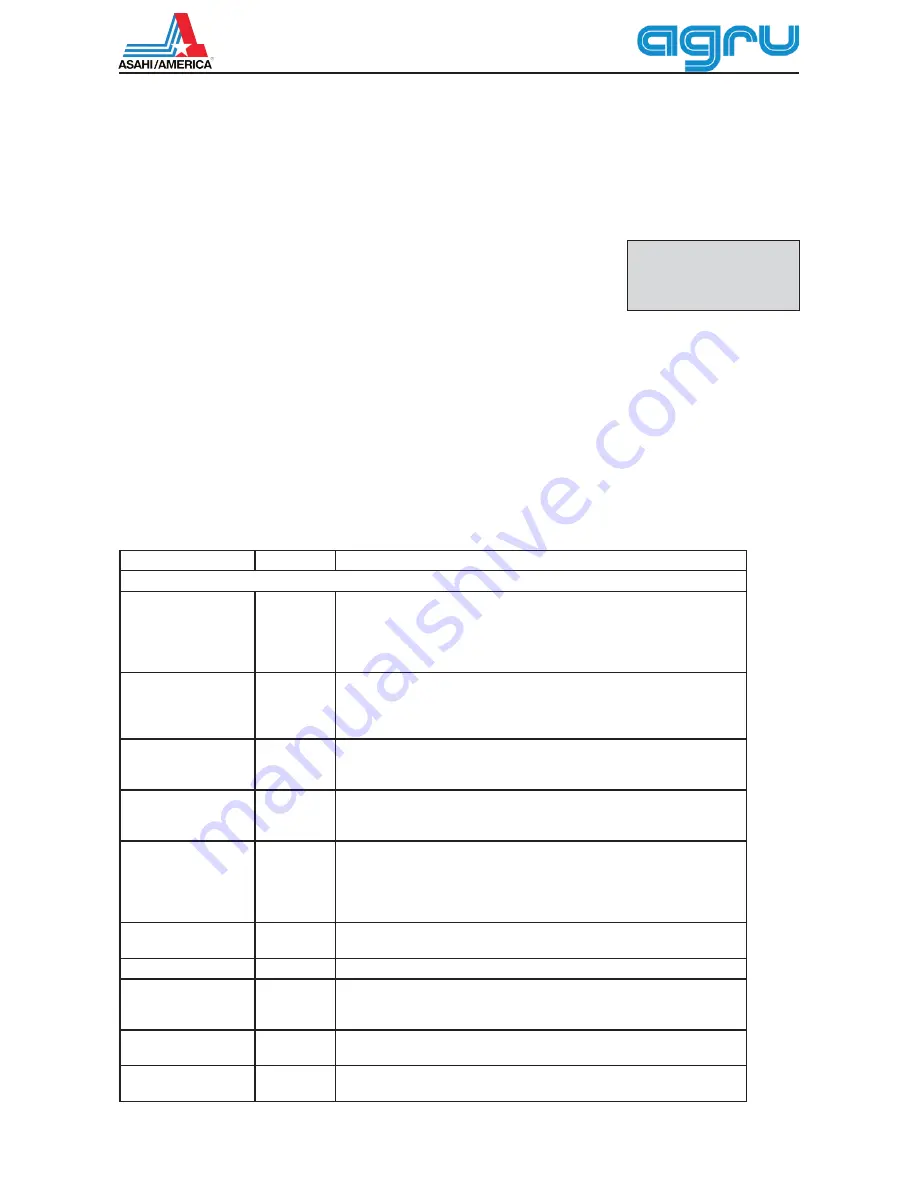
Version October 2015
EN
15
agru EF 110-B User’s Manual
the report. To say that the joint number is related to the job, or commis-
sion, number means that the system checks, when a commission number
was entered, whether it exists already in the internal memory. If so, it
takes the highest existing joint number for that commission, increments
it by 1, and applies this new joint number to the next welding operation
in that commission.
4.4 Configuring the Welding System
In Display 3, the welder has the possibility to:
•
read the welding parameters from a bar code or a RFID card and
start a welding process (move on to Section 4.6);
•
enter the welding parameters for the next welding manually and
start the welding process (move on to Section 4.5);
•
change the sytems settings in the configuration menu (press the
MENU key).
Accessing the menu requires an access code (see Display 6). The menu
is structured according to three submenus, the third of which, “Sensor
Parameters,” does not contain any parameters important for welding, but
only for set-up and maintenance work. They are therefore protected by a
second access code that is disclosed only to authorized personnel. The
configuration menu has the items listed in the following table.
To toggle from « On » to « Off » or vice versa for an option, press the
Ö
cursor key, to open a submenu or go to an additional screen for an
option, which is indicated by the letter – M –, press the MENU key.
Designation
Setting
Description / Data to be entered
—— “Settings” submenu ————————
AutoWeld
ON / OFF
"on” means that for two subsequent welding with identical welding/
fitting parameters, the parameters of the preceding one are applied
automatically to the following one (see Sect. 4.6.4), “off,” that the
parameters have to be read or entered again for every new wleding
operation.
Check Code Expiry
ON / OFF
"on” means that the welder identification code has to be current and
not expired (default period of validity 2 years from code issuance),
or the welding operation cannot be started, “off,” that the validity of
the code is not checked at all.
Memory Control
ON / OFF
if ON: Machine stops when the memory is full;
if OFF: Machine overwrites the oldest report when the memory is
full.
Manual Input
On / Off
"on” means that the manual input of welding parameters or
computed parameters is possible, “off,” that the manual input is not
allowed.
Welder Code Options
Menu
In a sub-menu, it can be determined when the welder code, if it is
enabled at “Recording,” has to be entered: always, i. e. before evey
single welding operation, only before the first welding operation after
switching the unit on or only after the first welding operation of a
new day/date..
Language
Menu
In a sub-menu, the language in which display texts and reports are
edited can be selected.
Date/Time
Menu
In a sub-menu, date and time can be set.
Buzzer Volume
Menu
In a sub-menu, the volume of the audible signal that the machine
emits to validate the execution of a given step in the process can be
set.
Temperature Unit
(°C / °F)
Menu
In a sub-menu, the temperature unit used for displaying and saving
welding data can be selected.
Unit of Pressure
(bar / psi)
Menu
In a sub-menu, the unit of pressure used for displaying and saving
welding data can be selected.
Display 6
Enter Menu Code
******