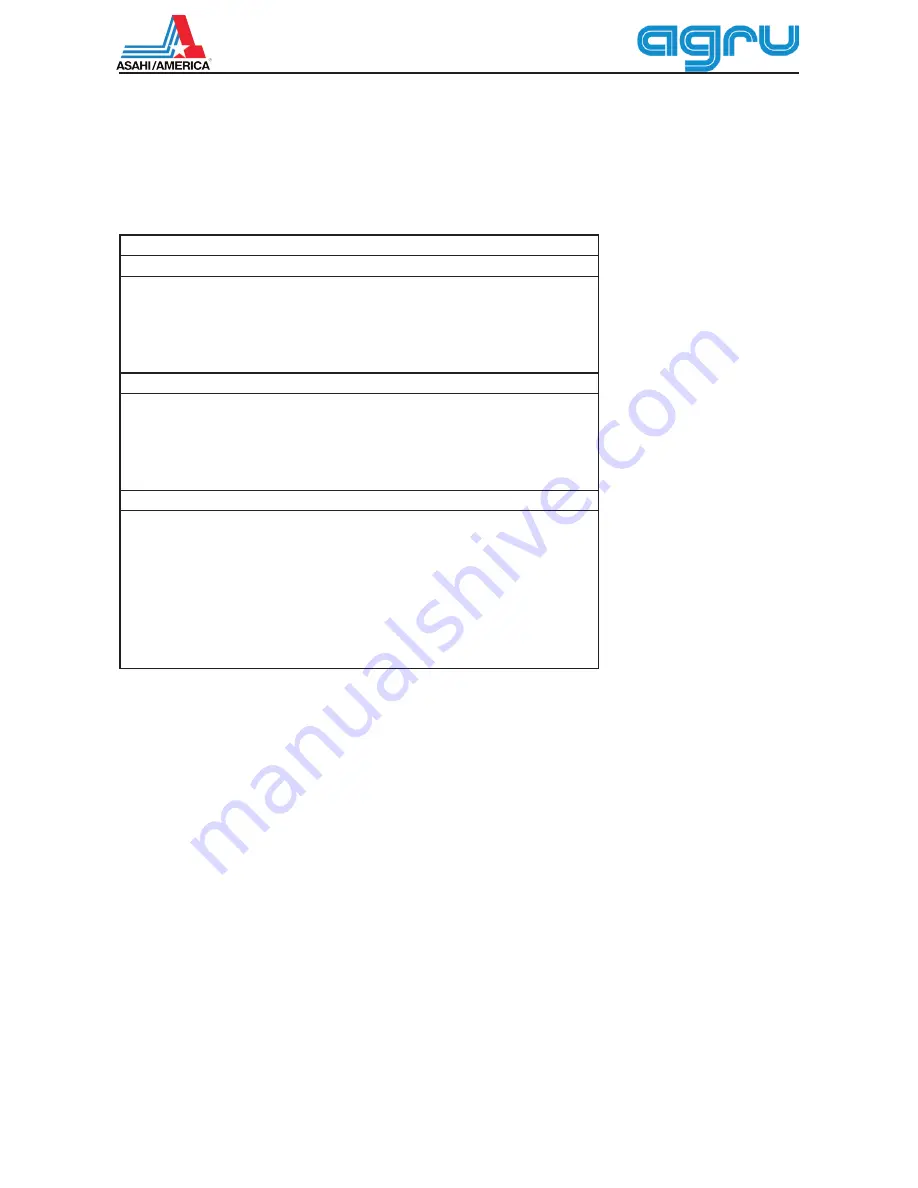
Version October 2015
EN
11
agru EF 110-B User’s Manual
The welding process in monitored in its entirety and saved to a welding
report. All welding reports can then be downloaded to a USB stick as
an abstract or extended report in the PDF format or in the DataWork
database management format.
Using the menus, the machine can be customized to the application at
hand (see Sect. 4.3, Configuring the Machine).
3.2.4 Specifications
agru EF 110-B
Power Supply Characteristics
Voltage
Frequency
Rated Power
Input Current
Max. Output Current
Output Voltag
230 V AC
50 / 60 Hz
2000 VA, 80% duty cy.
approx. 10 A
approx. 40 A
8 V - 48 V
Welding Operation Specs
Ambient Temperature (operation)
Ambient Temperature (storage)
Operating Range
Ingress Protection
Welding Report Memory Capacity
USB Communication Interface
– 10°C to + 45°C (+ 14°F to 113°F)
– 25°C to + 65°C (– 13°F to 149°F)
max. component size 110 mm
IP 54
10,000 reports
USB v 2.0 (480 mbit/s)
Dimensions and Weight
Dimensions (W x D x H)
Mechanical Structure
Control Unit
Transport Box
Weight
Mechanical Structure
Control Unit
Facing Tool
Transport Box with All Elements
Empty Transport Box
675 x 200 x 190 mm
420 x 320 x 240 mm
800 x 600 x 608 mm
approx. 6 kg
approx. 15 kg
approx. 4 kg
approx. 83 kg
approx. 42 kg
3.3 Welding Process Overview
The welding system allows welding electrofusion fittings that feature a
bar code. Every e-fitting is provided with a tag with one or two bar codes
on it. The structure of this code is internationally standardized. The first
code, encoding the data on proper welding, complies with ISO 13950,
the second code, if present, encoding the component traceability data,
complies with ISO 12176. The welding parameters can also be entered
manually.
When using an inside balloon in the pipe, beadless welding is possible.
To automate a beadless welding process, a special code with 34 digits,
which builds on the abovementioned 24-digit code^s, has to be read from
a RFID transponder card or entered manually. The parameters related
to balloon pressure can also be entered manually.
The welding system is microprocessor-controlled and:-
•
controls and monitors the welding process in a fully automated way,
when the welder starts it after component preparation,
•
determines welding duration depending on ambient temperature,
•
shows all information on the display in plain text.
The welding process is performed as follows:
•
All welding parameters and traceability data for the components
are read from a RFID transponder card or a bar code or entered