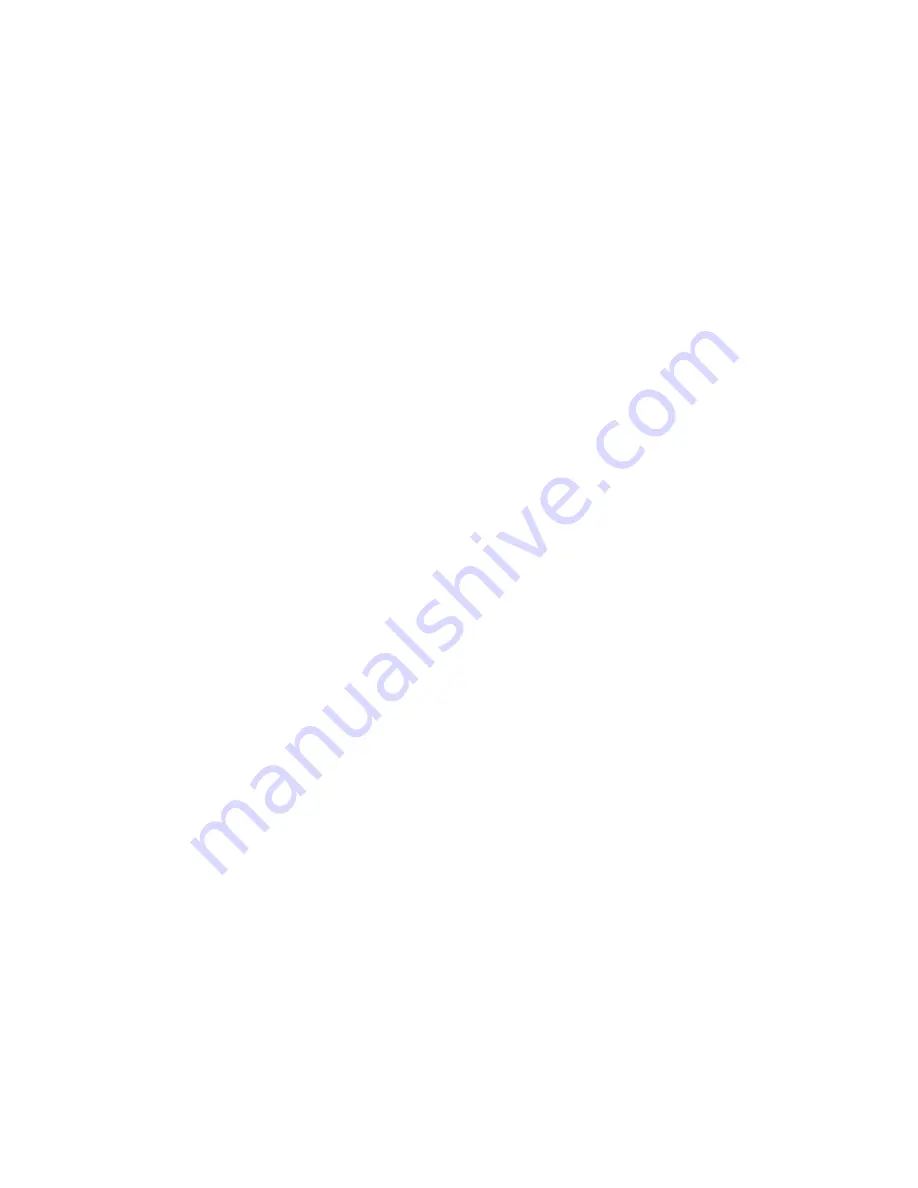
138
Installation and User’s Guide
F
Understanding the Bias Networks
Features
Using the Agilent 11612V K11 and K21 bias networks, you can
simultaneously supply DC bias and RF energy to the device under test
(without the need to use patch cables or adapters) to make convenient
and accurate DC and S- parameter measurements.
Each bias network provides:
•
floating triaxial FORCE connection to
input
current or voltage
•
floating triaxial SENSE connection to
monitor
voltage or current
•
floating triaxial GNDU connection to implement an active ground
•
2.4 mm coaxial RF input
•
2.4 mm coaxial combined RF/DC output
•
device bias oscillation suppression
Содержание 85225F
Страница 1: ...Agilent Technologies Agilent 85225F PerformanceModelingSystem Installation and User s Guide ...
Страница 90: ...90 Installation and User s Guide 2 Installing the System ...
Страница 102: ...102 Installation and User s Guide 3 Verifying System Functionality ...
Страница 110: ...110 Installation and User s Guide 4 Servicing the System ...
Страница 118: ...118 Installation and User s Guide A Enhancing Measurement Accuracy ...
Страница 128: ...128 Installation and User s Guide C RF Subsystem Functional Verification Test ...
Страница 144: ...144 Installation and User s Guide G Network Analyzer Performance Specification Summary Transmission Measurements ...
Страница 148: ...148 Installation and User s Guide Index ...