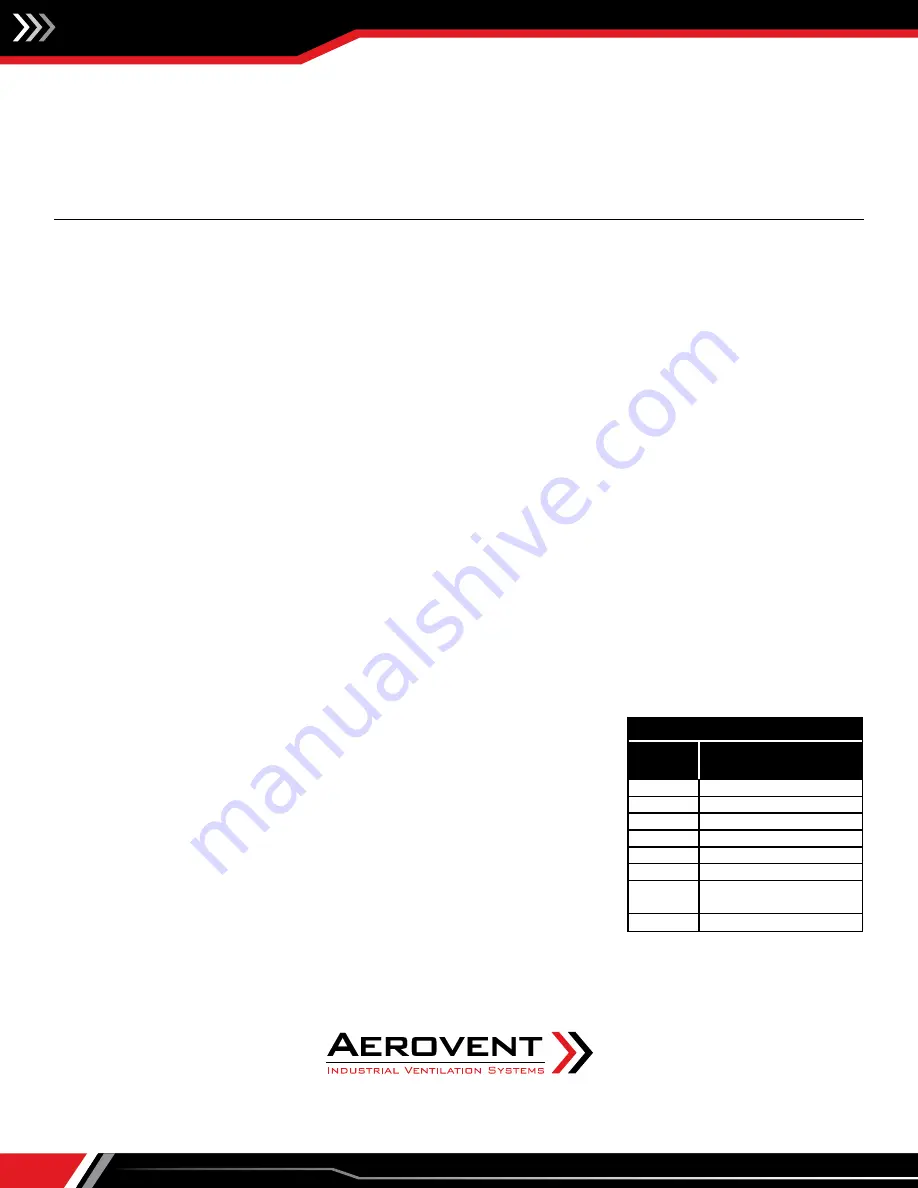
Installation, Operation & Maintenance Manual
IM-225
14
Maintenance
These motors use brushless technology with sealed bearings so no maintenance is required other than keeping the motors dry
and free of dirt, dust and debris. Always keep records of the maintenance that is performed.
Troubleshooting
Remote Dial does not vary the motor speed (all motor types, except OP)
• Verify that correct connections are made (refer to pages 9-10).
• Make sure that the connections are solid.
• Check control input voltage at connection (inside transformer box).
• Make sure that the dial on the motor is opened CW.
Speed control does not vary the motor speed
• Check voltage to ensure the motor is receiving the correct input voltage.
• Check voltage at the remote dial. 12V AC should be present across the 12V and COM terminals and 0-10V DC should be present
between the 0-10V and COM terminals.
• Verify that the potentiometer or 0-10V DC lead is properly wired to the control board according to the diagram.
• Verify that all of the connections inside of the fan and motor are secure.
GridPoint controller does not connect to motor
• Check that cable connections are secure between the motor and the GridPoint controller.
Motor does not operate (TEFC motors:
67002107, 67002205
)
• Check that the motor is wired for the correct supply voltage.
• Verify the Status LED is solid red.
• Verify that the jumper wire is present between terminals 9 and 10 on the low voltage terminal board because this is required
for the motor to operate.
• Verify that the yellow wires are present on terminals 5 and 6 on the low voltage terminal board.
Fault indication (TEFC motors:
67002107, 67002205
)
A red LED is located either on the control board or on the side of the conduit box to
provide diagnostic assistance of motor faults. When a fault occurs, the LED will blink
a specific number of times to identify the fault that has occurred. See the table to the
right for fault indications.
When a fault occurs, the LED will blink the number of times corresponding to the fault,
pause and then repeat blinking. Count the number of blinks multiple times to ensure
that the proper fault has been identified. With most of the faults, the motor will restart
automatically. If the motor experiences an overload fault over 10 times within an hour,
the motor will shut down to protect itself and the power will need to be reset.
TEFC Motors (67002107 and 67002205)
No. of
Blinks
Indicated Fault
2
Overcurrent
3
Overvoltage
4
Undervoltage
5
Communication Error
6
Sync Loss
7
Spin Fault
8
3 Sec/60 Sec
Motor Overload
9
Motor Over-Temperature