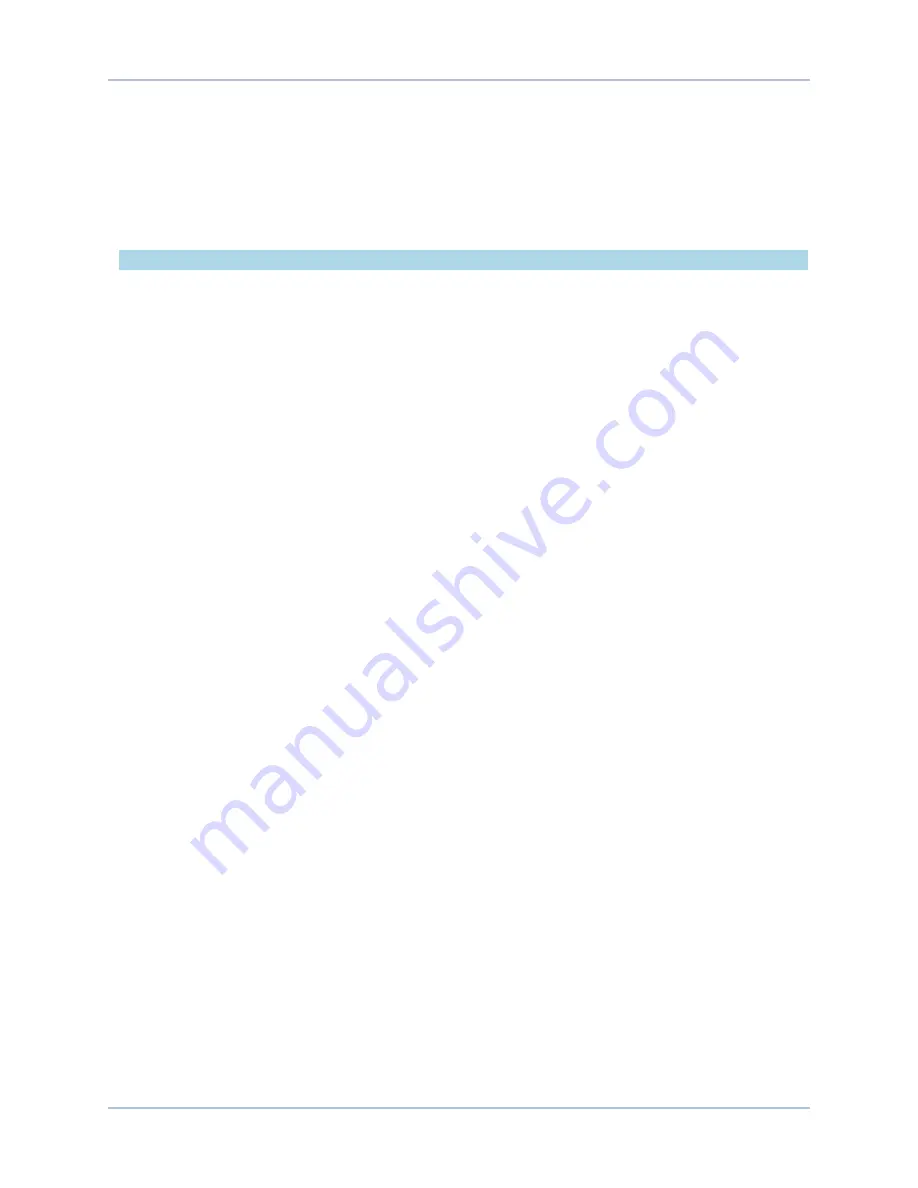
Introduction
Ensemble HLe
1.2.1. System Power Requirements
The following equations can be used to determine total system power requirements. The actual power
required from the mains supply will be the combination of actual motor power (work), motor resistance
losses, and efficiency losses in the power electronics or power transformer. An EfficiencyFactor of
approximately 50% should be used in the following equations.
Linear Motor
Pdiss[W] = MotorCurrentPeak[A] * TotalBusVoltage[V] * 3 / 2
Pin = SUM ( Pdiss ) / EfficiencyFactor
www.aerotech.com
Chapter 1
21
Содержание Ensemble HLe
Страница 1: ...Revision 4 09 00 Ensemble HLe Hardware Manual ...
Страница 14: ...Ensemble HLe Quick Installation Guide 14 www aerotech com This page intentionally left blank ...
Страница 56: ...56 Chapter 2 www aerotech com Figure 2 27 PSO Interface Ensemble HLe Installation and Configuration ...
Страница 80: ...80 Chapter 3 www aerotech com Figure 3 9 Digital Inputs TB305 shown Ensemble HLe IO Expansion Board ...
Страница 84: ...84 Chapter 3 www aerotech com Figure 3 12 Digital Outputs IO Board Ensemble HLe IO Expansion Board ...
Страница 87: ... IO Expansion Board Ensemble HLe Figure 3 15 J302 J303 www aerotech com Chapter 3 87 ...
Страница 88: ...Ensemble HLe IO Expansion Board 88 Chapter 3 www aerotech com This page intentionally left blank ...
Страница 98: ...98 Chapter 5 www aerotech com Ensemble HLe Accessories This page intentionally left blank ...
Страница 108: ...Ensemble HLe Revision History 108 Appendix B www aerotech com This page intentionally left blank ...