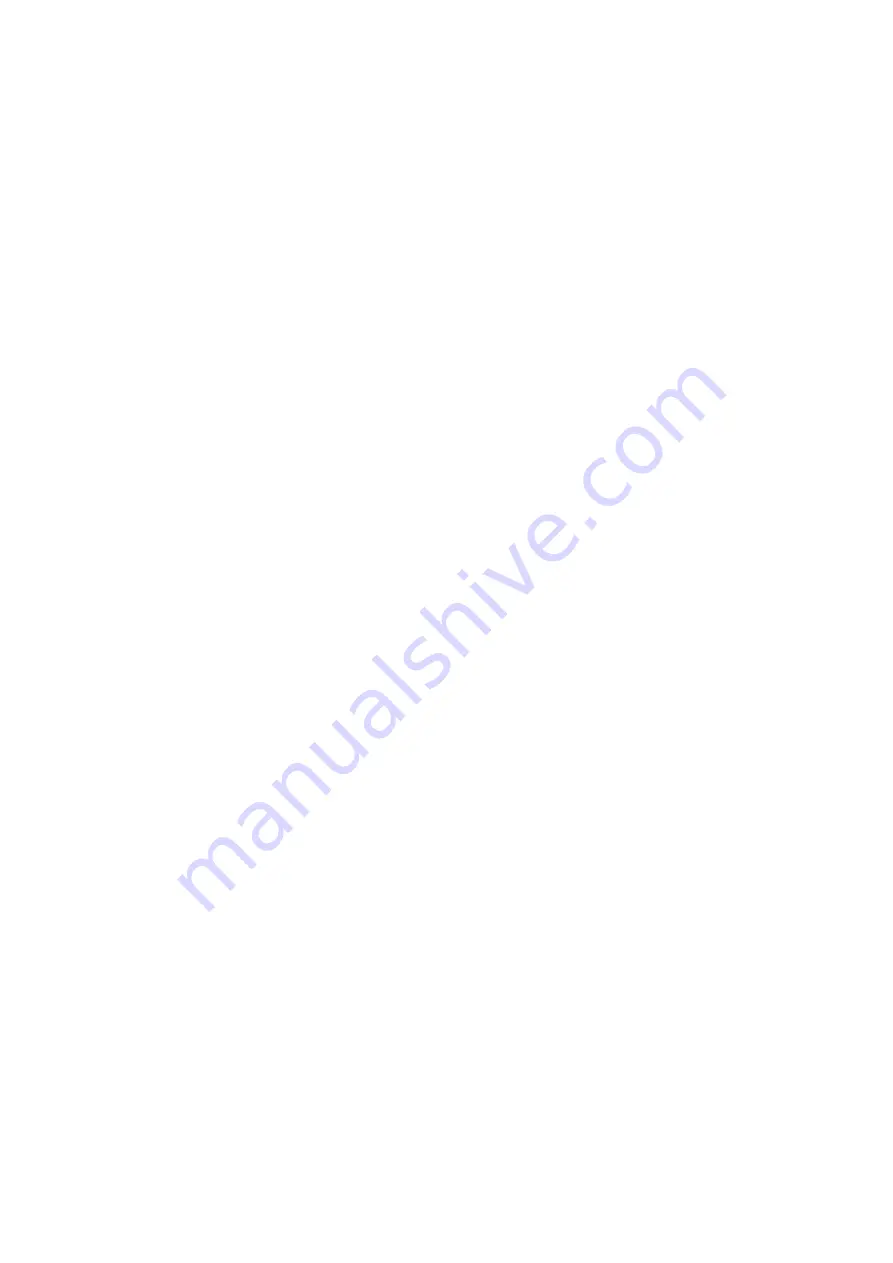
20
wit
disassembled, including the removal
of all sleeves and bushings, flushed liberally with fresh water, dried completely.
. A wet glider must be dried before storing. Do not leave your glider wet for more than one day, because corrosion
4. Ta
intertime.
5. If
Hose do
6. Cleaning y
generally
labeled f
PROCE
ROS HANG GLIDERS
SPECIAL CIRCUMSTANCES
1. Any time you suffer a crash or extremely hard landing you should have an “annual” inspection done on your glider
to insure that you find all damaged parts. Following any hard landing, be sure to inspect the apex hardware, the control
bar legs and basetube, and all control bar fittings for damage. Any time you replace a control bar leg or basetube, you
must carefully inspect all related fittings and replace any that are bent or damaged.
Hard landings may also impose very high loads on the sprog assemblies and transverse battens, and bridle lines.
Inspect accordingly.
. If your glider is ever exposed to salt water you will need to have the glider completely disassembled in accordance
2
h the recommended annual inspection procedure. All frame parts will need to be
3
may result.
ke special care to avoid ice covering of the glider, particularly the leading edge in w
you fly regularly at the coast in windy conditions, be aware that the sea mist spray can have the same effect.
wn your glider after such flights, and keep a special lookout for corrosion.
our sail - keeping your sail clean will extend the life of the cloth. When cleaning the entire sail you should
use only water and a soft brush. You may clean small spots or stains with any commercial spot remover that is
or use on polyester.
DURE FOR CHECKING CARBON FIBER CROSSBEAMS APPLIED IN AE
The present procedure is applicable for composite crossbeams (hereinafter -crossbeams") used in the frame of the
hang glid
Combat-15,Combat L12,Combat L-13, Combat L-14, Combat
ers KPL-13, KPL-14. Combat-13 and Combat-1
4,
L-15, Co
onsists of visual inspection.
mbat L 07 12,Combat L07 13, Combat L07 14, Combat L07 15
and
c
1. General inspection. T
alls
he crossbeam should be free of visible defects/damage of the bearing structure of its w
and ban
m.
ds. Delaminating of decorative coating is possible and it doesn't influence strength of the crossbea
2. Root junction of the crossbeam attachment. Bushings should not be biased; this is determined using glue marks
around their flange. The slack of the bushings in relation to the crossbeam is not allowed.
3. Tip attachment junction. The tip of the crossbeam should have no disintegration and visible damage.
In a
be determined by a
ny case when damage is discovered, the repairiability of the crossbeam should
representative of Aeros Ltd or by the manufacture of the crossbeam.
Conclusion about further possibility to use the crossbeam can be made only after loading the crossbeam
and can be done by a representative of Aeros Lt
d or by the manufacture of the crossbeam only.
A NOTE ABOUT CABLES AND CABLE MAINTENANCE
The cables which support the glider’s airframe are critical components of the glider’s structure, and must be
maintain
ctice in the design of aircraft structures to design to an ultimate
strength of 1.5 times the highest expected load in normal service.
Hang glider cables, like other structural components on the glider, are typically designed with a structural safety factor
of only a
loss in cable strength can be tolerated.
A cable with even a single broken strand must be replaced before the glider is flown again. A cable which has been
bent sharply enough to have taken a permanent set must also be replaced immediately.
Some degree of fatigue due to repeated bending of cables is almost unavoidable in an aircraft that is assembled and
disassembled with every flight. Side wires are subject to the highest loads in flight, and are therefore the most critical.
This is why we recommend that these wires be replaced annually, even if there is no known damage.
ed in an air worthy condition. It is a general pra
bout 50% above the expected maximum load. No significant
Содержание COMBAT-09
Страница 2: ...1...
Страница 27: ...26...
Страница 28: ......
Страница 29: ......
Страница 30: ......
Страница 31: ......
Страница 32: ......
Страница 33: ......
Страница 34: ......
Страница 36: ......
Страница 38: ......
Страница 42: ......
Страница 43: ......
Страница 44: ......
Страница 45: ......
Страница 46: ......
Страница 47: ......
Страница 48: ......