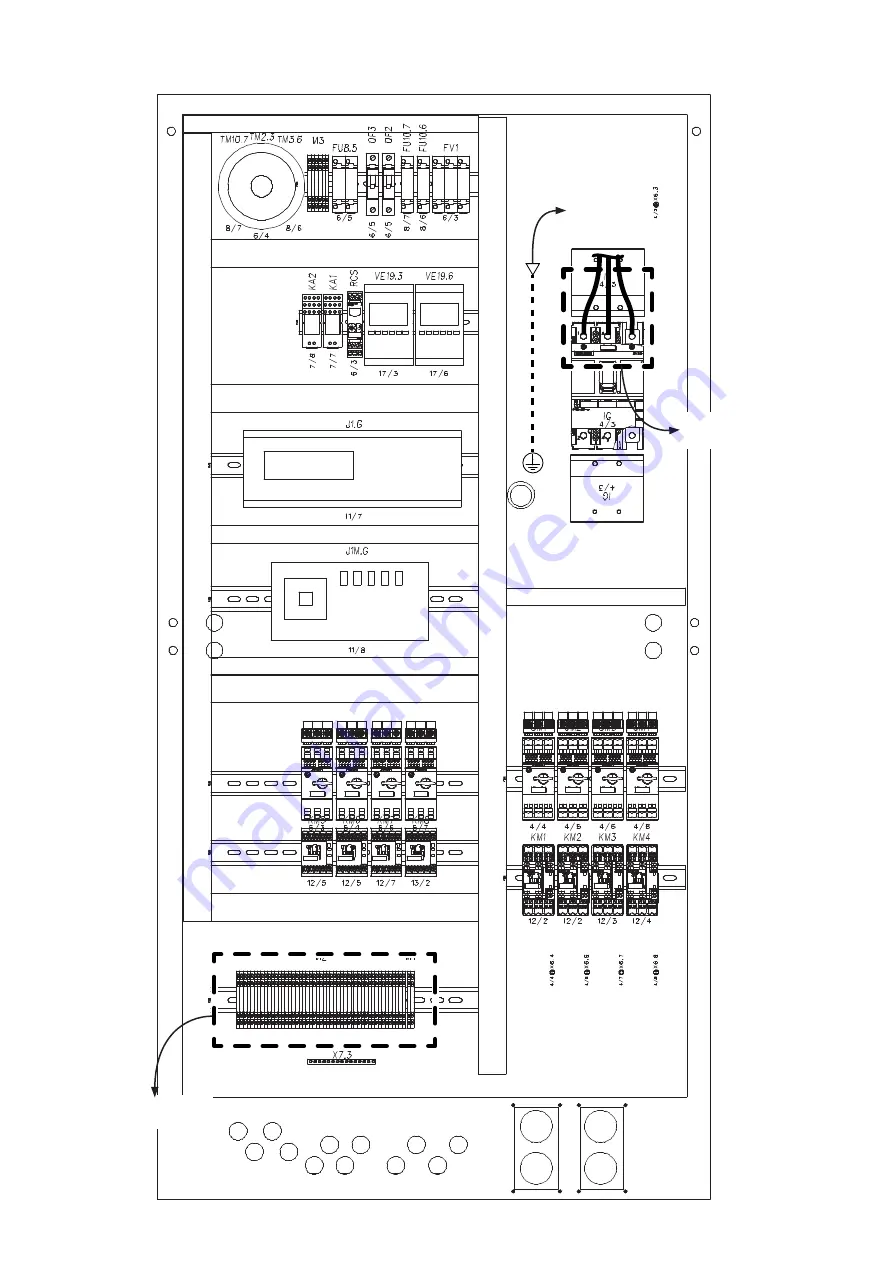
30
INDICATIVE LAYOUT MODEL WRK 700
Power lines input
L1-L2-L3
Earthing
PE
auxiliary terminal
board position
COMMISSIONING - WARNINGS
Please note that, on request by the Aermec customer or the legitimate
owner of the machine, the units in this series can be started up by
the AERMEC After-Sales Service in your area
(valid only on ITALIAN
territory).
The start of operation must be scheduled in advance based
on the time frame for the completion of works for the system. Prior to the
intervention, all other works (electrical and hydraulic hook-ups, priming
and bleeding of air from the system) must have been completed.
START-UP
OPERATIONS TO BE PERFORMED WITH NO VOLTAGE PRESENT
ATTENTION
the unit is not working:
Check:
- All safety conditions have been respected
- The unit is correctly fixed to the support surface
- The minimum technical spaces have been respected
- That the main power supply cables have appropriate cross-section,
which can support the total consumption of the unit. (see electric
data sections) and that the unit has been duly connected to the
ground.
- That all the electrical connections have been made correctly and all
the terminals adequately tightened.
- Check for refrigerant gas leaks, especially near the pressure points
of pressure gauges, pressure transducers and pressure switches.
(vibrations during transport may have loosened the connections).
OPERATIONS TO BE PERFORMED WITH THE UNIT LIVE
ATTENTION
the unit is still not working:
- Supply power to the unit by turning the master switch to the ON
position.
- Use a tester to verify that the value of the power supply voltage to
the phases is equal to 400V ± 10%; also verify that the unbalance
between phases is no greater than 3%.
- Check that the connections made by the installer are in compliance
with the documentation.
- Verify that the resistor of the compressor sump is working by
measuring the increase in temperature of the oil pan. The resistance/s
must function for at least 12 hours before start-up of the compressor
and in any event, the temperature of the oil pan must be 10-15°C
higher than room temperature.
HYDRAULIC CIRCUIT CONTROLS
- Check that all hydraulic connections are made correctly, that the
plate indications are complied with and that a mechanical filter has
been installed in each inlet heat exchanger.
(Mandatory component
for warranty to be valid).
- Make sure that the circulation pump/s is operating and that the
water flow rate is sufficient to close the contact of the flow switch, if
installed.
- Check the water flow rate, measuring the pressure difference
between inlet and outlet of the evaporator and calculate the flow rate
using the evaporator pressure drop tables present in this manual.
- Check the correct functioning of the flow meters if installed. Closing
the cut-off valve at the output of the heat exchanger; the unit control
panel must show the block. Finally re-open the valve and rearm the
block
COMMISSIONING
- Once all the aforementioned checks have been carried out, the unit
can be commissioned
- Close the door of the electrical panel.
- Set the unit main switch to ON, the unit will start after a few minutes
OPERATIONS TO BE PERFORMED WITH MACHINE ON
ATTENTION
the unit is working:
Check:
- That the compressor input current is lower than the maximum
indicated in the electrical data table.
- Before starting the unit, check that the compressor rotates in the
correct direction through a three-phase protection. The spiral
compressors compress in one direction of rotation only. Therefore,
it is essential for the phase of the three-phase spiral compressors
to be correctly connected (the correct direction of rotation can be
controlled when the pressure on the intake side decreases and that
on the flow side increases with the compressor in operation). If the
connection is incorrect, the direction of rotation is reversed: this
causes a loud noise and the reduction of current consumption. In this
case, the protection system inside the compressor activated turning
off the unit. To solve the problem, disconnect and swap the wires
between two of the phases, then connect the three-phases again.
- That the voltage value lies within the pre-fixed limits and that
unbalance between the three phases (three-phase power supply) is
not above 3%.
If having to take measurements and perform checks that require the
machine to run, you must:
- make sure that any remote control systems are disconnected;
however, keep in mind that the PLC on the machine controls its
functions and can enable and disable the components creating
hazardous situations (e.g. power and rotate the fans and their
mechanical drive systems).
- Operate with the electrical board open the shortest time possible
- Close the electrical board as soon as the single measurement or
control is performed
ATTENTION
The anti-freeze set temperature can only be varied by an authorised
after-sales centre and only after having checked that there is a suitable
% of anti-freeze solution in the water circuit.
Whenever this alarm intervenes, call the nearest authorised after-sales
service immediately
- Control of the water flow rate alarm, the unit provides for the
management of a flow rate alarm controlled by a differential pressure
switch or flow switch if provided. This type of safety device intervenes
after the first 30 seconds of pump functioning, if the water flow rate is
not sufficient. The intervention stops the compressor and the pump
itself.
Содержание WRK0300H
Страница 2: ......
Страница 5: ...5 CERTIFICATIONS COMPANY CERTIFICATIONS SAFETY CERTIFICATIONS ...
Страница 12: ...12 Xg Yg Xg Yg CENTER OF GRAVITY POSITION TOP VIEW MODELS 0500 0700 TOP VIEW MODELS 0300 0350 ...
Страница 30: ...30 INDICATIVE LAYOUT MODEL WRK 700 Power lines input L1 L2 L3 Earthing PE auxiliary terminal board position ...
Страница 39: ......