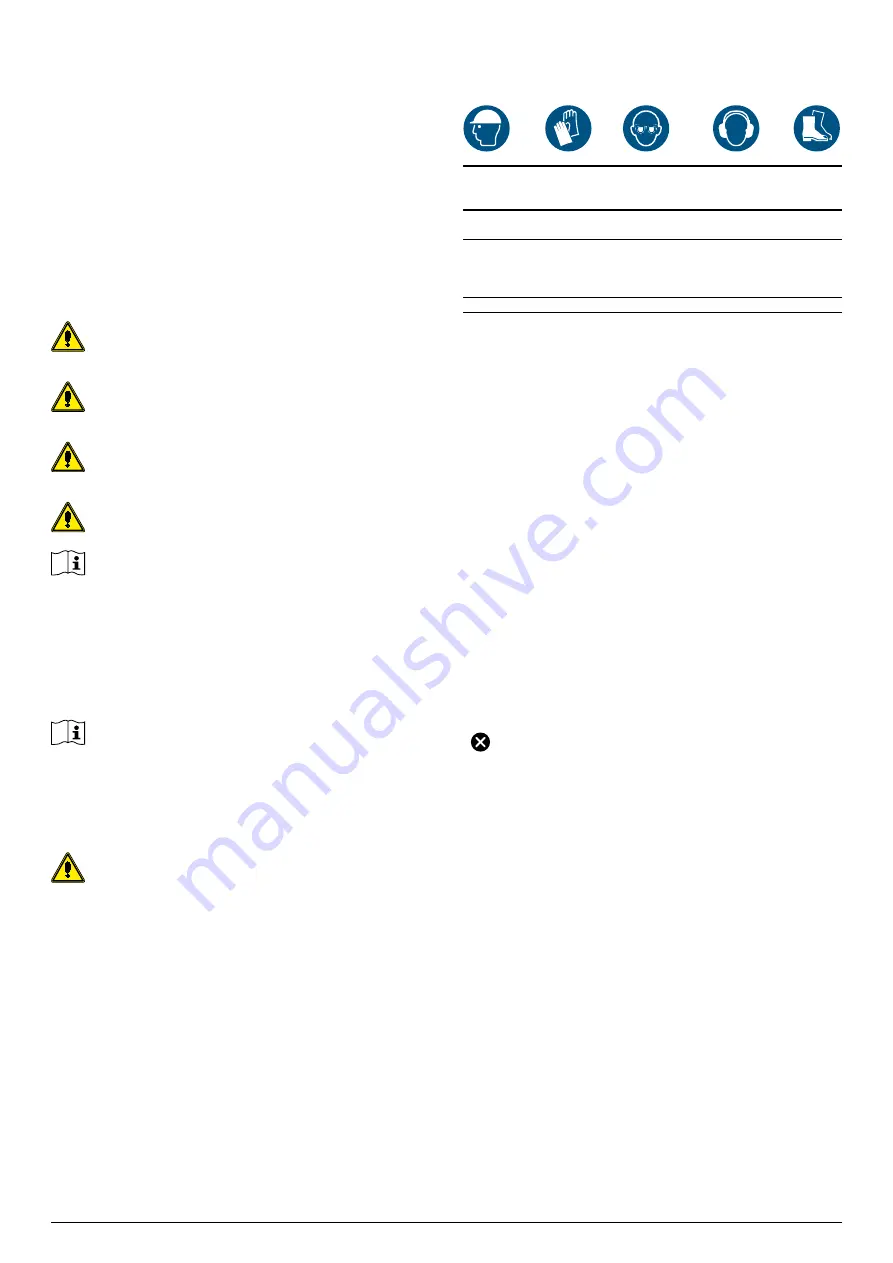
23.05 – 6755517_09
23
16 GENERAL WARNINGS
INTRODUCTION
The unit you have purchased is a complex machine. During installation, operation,
maintenance and repair, people and property can be exposed to risks caused by
certain conditions or components such as, but not limited to, refrigerant gas, oils,
moving parts, pressures, sources of heat, electrical voltage.
This manual provides information about the standard functions and procedures of
all units in the series and is an important support document for qualified personnel,
but does not replace them.
Before proceeding with the installation and start-up of the unit, careful-
ly read this manual and all of its notes marked with the following sym-
bols, which indicate the various levels of hazard or situations that are
potentially hazardous to prevent malfunctioning or physical damage to
property or personal injury:
HAZARD indicates a situation of imminent danger:
if it is not observed,
it can cause death or serious injuries, it is mandatory to carefully follow the
listed measures.
WARNINGS indicate a potentially dangerous situation:
which if not
avoided could cause serious or fatal injuries. Pay close attention while
working
WARNING indicates a potentially dangerous situation that, if not
avoided, could lead to slight or moderate injuries or damage to prop-
erty
INFORMATION this points out that a potentially harmful situation
could occur that, if not avoided, could cause property damage
IMPORTANT additional information on how to use the product
The manual contains important indications for commissioning the unit as well as
fundamental instructions in order to prevent personal injuries or damage to the
machine during its operation. Finally, to also guarantee that it will operate perfectly,
maintenance instructions are provided.
The unit must be installed by specialised technicians in compliance with current
laws in the country of installation. The unit must also be started up by authorised
and trained personnel, and all activities must be carried out in compliance with and
in observance of all the local standards and laws, and all work on the system must
be performed in a workmanlike manner.
Even though our unit is equipped with numerous safety and protec-
tion devices and has been tested in the factory, maximum attention
must be paid when working on it, observing the precautions against
residual risks.
GENERAL WARNINGS
ATTENTION:
— The machine must be transported in compliance with the laws in force in the
country of destination, considering the characteristics of the fluids it contains
and their characterisation. Incorrect transport could cause machine damage,
which would also generate refrigerant leaks. Before the first start-up, it is neces-
sary to search for any leaks using suitable personal protective equipment;
— When the product is received, check the condition and completeness of the
supply and, if it does not match what was ordered, contact the agency that sold
the equipment;
— The product is intended to be used for the purpose indicated by Aermec and for
which it was expressly designed. Aermec shall not be contractually or non-con-
tractually liable for any damage to people, animals or objects, installation, ad-
justment and maintenance errors or incorrect use;
— During installation and/or maintenance operations, remember that they must
be performed by qualified and prepared personnel and it is require to wear
protective devices (gloves, eye protection, helmet, …) that are suitable for the
operations to be performed: do not wear clothing or accessories that can get
caught or be sucked in by the air flows; collect and tie up hair before accessing
the inside of the unit, Aermec shall not be held liable for the failure to observe
the safety and accident prevention regulations in force;
Personal protective
equipment (PPE)
(1)
Operations
Handling
Installation and/or
maintenance
Welding or brazing
Safety gloves,
helmet, goggles,
safety footwear,
protective garments.
•
•
•
Earmuffs
•
•
(1) It is recommended to follow the instructions in EN 378-3.
— Observe the laws in force in the country of unit installation that concern use and
disposal of the packaging, the products used for cleaning and maintenance,
and for managing the end of the unit's service life;
— Repair and maintenance work must be performed by Aermec Technical Service.
Do not modify or tamper with the unit as dangerous situations may be created
and the equipment manufacturer will not be liable for any damage caused;
— In the case of abnormal operation, or if liquids leak, move the main switch for
the system to "off" and close the interception taps. Call the local AermecTechni-
cal Service and do not work on the equipment personally;
— The unit must be installed in structures that are protected against atmospheric
discharges, as required by applicable laws and technical standards;
— The equipment contain refrigerant gas: proceed carefully to prevent damaging
the gas circuit or the finned coil;
— Based on EU regulation 517/2014 concerning certain fluorinated greenhouse
gases, it is mandatory to indicate the total quantity of refrigerant contained in
the installed system. This value is indicated on the rating plate on the unit;
— This unit contains fluorinated greenhouse gases covered by the Kyoto Proto-
col. Maintenance and disposal operations must be only carried out by qualified
personnel;
— This manual is an integral part of the unit and as a result it must be stored care-
fully and must always accompany it, even if transferred to another owner or
user, or if transferred to another plant. If damaged or lost, a copy can be down-
loaded from our website www.aermec.com
— The overall fire risk assessment at the place of installation (i.e. fire load calcula-
tion) is the responsibility of the user.
— Perform the plant connections following the indications provided in this man-
ual.
IT IS FORBIDDEN TO:
— It is not permitted to walk on the machine or to place other items on it: no part
of the unit may be used as a walkway or support for goods or people. Periodical-
ly check and repair or, if necessary, replace any component or pipe that shows
signs of damage. Use a platform, or suitable scaffolding to work at higher levels;
— Remove the protections from mobile elements while the unit is running;
— Touch the moving parts, stand between them or insert pointed objects through
the grids.
— Any technical intervention or cleaning operation before having disconnected
the appliance from the mains electric power supply: by positioning the system
master switch and the main device switch at "OFF".
— Modify the safety or regulation devices. The devices must be replaced by the
After-sales Technical Service Aermec, using only original components.
— Pull, detach or twist the electrical cables coming out of the unit even if it is dis-
connected from the mains electric power supply;
— To dispose of the packaging material in the environment or leave it within reach
of children: as it may be a potential source of danger. Therefore it must be dis-
posed of according to what is defined by current laws.
ESSENTIAL SAFETY RULES
Any technical intervention must be performed by qualified and author-
ised personnel. The personnel performing the work must have been
trained and be familiar with this type of product and its installation.
The machine must only be employed for the use for which it was made; any other
use can be dangerous and void the warranty;
It is not permitted to walk on the machine or to place other items on it. No part
of the unit may be used as a walkway or support for goods or people. Periodically
Содержание ANL 100-HP
Страница 2: ......