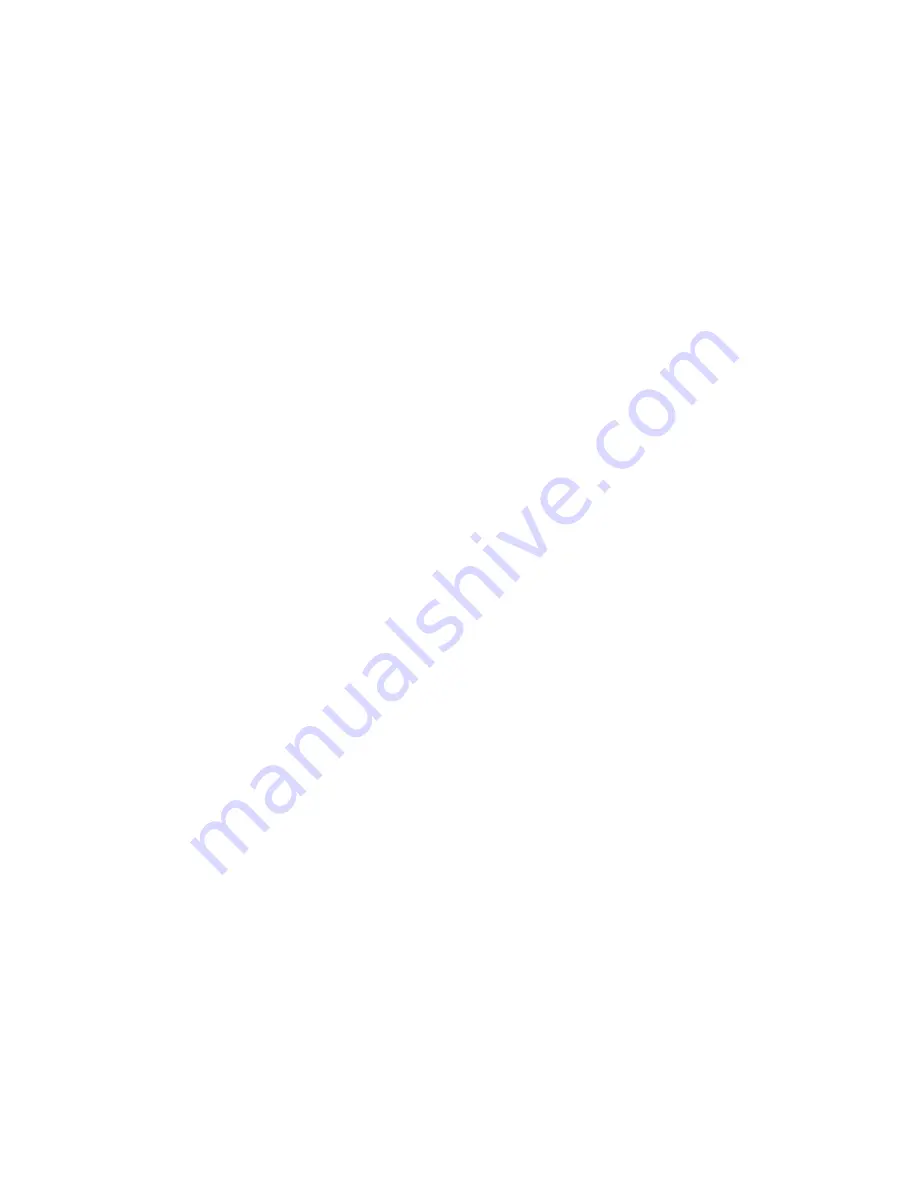
16
Seal Temperature: When the power is ON, the heater bar element receives electrical current. The PLC
pulses electrical current to the element until the temperature setting is reached. An amber indicator lamp
illuminates on the Bag Setup Screen while the element is receiving current. The longer the light is
illuminating, the longer the "pulse" of current and the further away from the temperature setting. If the
temperature of the heater bar is not within a set range around the set point, “Waiting” will be flashed on
the top left screen.
Note on Seal Quality: Quality seals are achieved by making adjustments to SEAL TIME, SEAL TEMP.,
SEAL POINT and by having the proper seal pressure.
3.11 Options Available Menu
Options that can be added to the T-300 at the factory will be accessed from an Options Screen. If options
were not installed at the factory, then N/A (Not available) will be displayed to the left of each options
button. Otherwise, the button will display ON or OFF. Contact APPI Sales Support for additional
options, programming, or operations for automatic infeed operations. See Fig. 3-7.
Note: If options are added in the field, a pass code is required to Enable use of the option. Contact
APPI for a pass code. Options which have been purchased separately must be installed by APPI or by
qualified maintenance personnel.
The following sections describe how to setup optional equipment. If your T-300/T-375 is not equipped
with these options, please disregard these sections.
3.15 CF-10 Counting Funnel
A Photo optic and preset Counting option not included in the standard T-300/T-375 package and must be
purchased separately. This option is useful and will automatically cycle the bagger when a preset number
of parts have fallen through the funnel.
Photo optic eyes may vary depending on your product, so parts should be sent to APPI for testing to
determine the correct components. Parts must be separated to be counted accurately through the eye. If
two parts fall at the same time, they may be counted as one. If loading automatically with minimal
distance between parts, an accumulating funnel or method of diverting may be required for separation
between the last part in the batch count and first part in the next batch. Contact APPI Sales Support for
additional options, programming, or operations for automatic infeed operations.
To turn ON the option, press the Mode toggle button. Press the <Reset> button to reset the count to the
preset value.
Parts length test: With the option ON, go to the Parts Length Test Screen, press the <Reset> button.
Toggle the T-300/T-375 to the Stop mode using the Toggle button located at the top left side of the
screen. Then, drop parts individually through the photo sensor / funnel. You will notice that the Min and
Max values will change as you drop parts through the eye. If the parts will be fed automatically, parts
should pass through the eye as they would if feeding automatically.
Min Setting: The Minimum Setting is used to filter scrap. If through testing the min value detected was
.2, setting the value to .1 would cause parts that are .1 or less not to be counted. If you set the Min.
Setting too close to the actual minimum test value however, these parts may not be counted causing over
counts. Setting the Minimum Setting to Zero will cause all parts to be counted.
Maximum Setting: The Max Setting is used to count parts connected or parts falling through the eye
together (overlapped) as two parts. If when testing the parts length, the Max value was determined to be
.5, you could set the Max Setting to .8. Then, if two parts overlapped go through the eye with a setting a
.9, they would be counted as two parts. However, if you set the Max Setting too close to the Max Value,
Содержание T-300
Страница 1: ...T 300 Table Top Bagger Operation Guide Ver 1 Installation Setup and Operation Guide ...
Страница 20: ...19 factory code so that the current pass codes can be displayed This page intentionally left blank ...
Страница 35: ...34 6 3 Preventive Maintenance PM Chart Continued ITEM DESCRIPTION 1 2 3 4 5 6 7 8 9 10 Inspected by Initials ...
Страница 36: ...35 Chapter 7 ______________________________________________________________________________ Trouble Shooting ...
Страница 41: ...40 7 12 Troubleshooting Notes Technical Support Information Date Notes ...