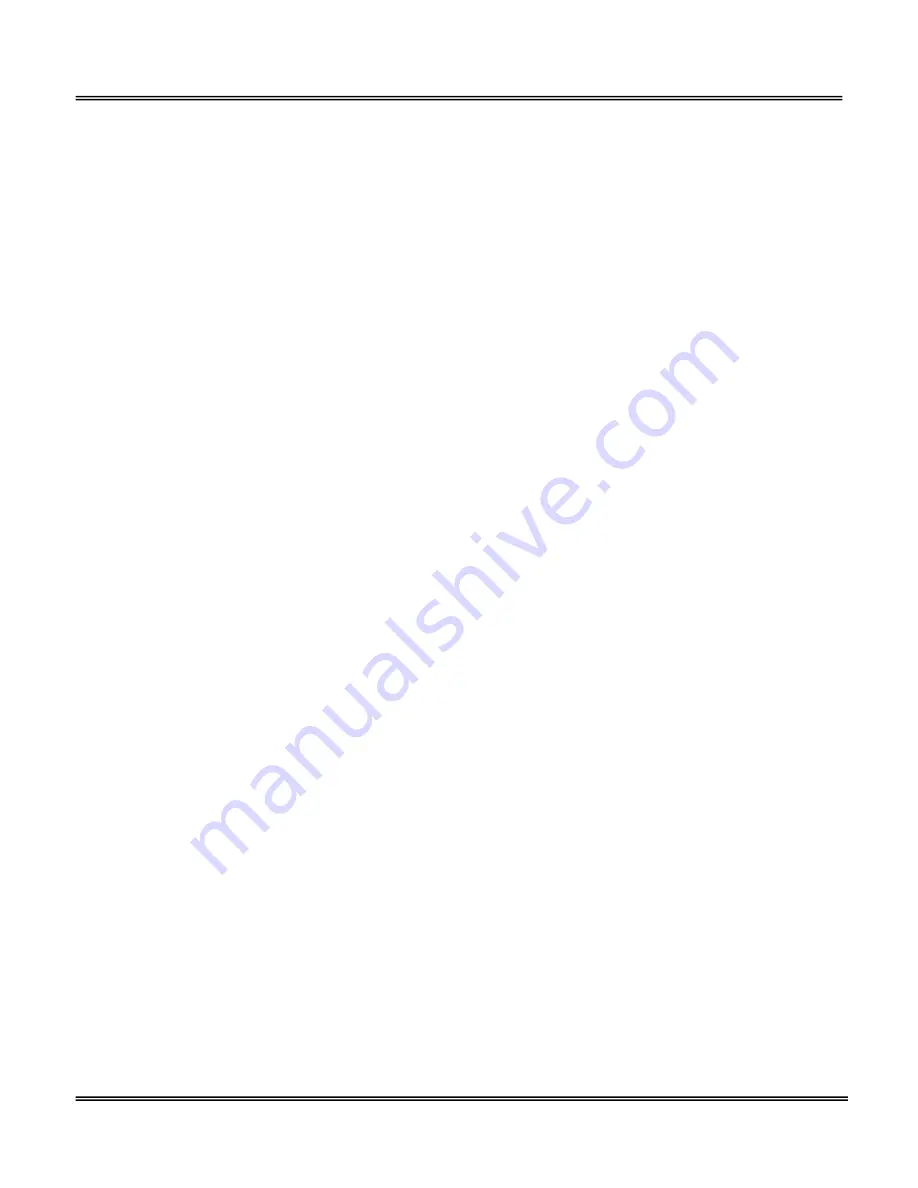
Advanced Instruments Inc.
Installation
The analyzers must be used in accordance with the guidelines delineated in this instruction manual.
Gas Sample Stream: Ensure the gas stream composition of the application is consistent with the specifications and if
in doubt, review the application and consult the factory before initiating the installation.
Note: In natural gas applications such as extraction and transmission, a low voltage current is applied to the pipeline
itself to inhibit corrosion of the pipeline. As a result, electronic devices connected to the pipeline can be affected unless
they are adequately grounded.
Contaminant Gases: A gas scrubber and flow indicator with integral metering valve are required upstream of the
analyzer to remove any interfering gases such as oxides of sulfur and/or hydrogen sulfide that can interfere with
measurement and cause reduction in the expected life of the sensor. Consult factory for recommendations concerning
the proper selection and installation of components.
Expected Sensor Life: With reference to the published specification, the expected life of all oxygen sensors is
predicated on the basis of average oxygen concentration (<10,000 PPM for a PPM sensor or air for a % sensor),
sample temperature of 77°F/25°C and sample pressure of 1 atmosphere in “normal” applications. Deviations from
standard conditions will affect the life of the sensor. As a rule of thumb sensor life is inversely proportional to changes
in oxygen concentration, sample pressure and temperature.
Accuracy & Calibration: Refer to section 5 Operation.
Materials: Assemble the necessary zero, sample and span gases and optional components such as valves, coalescing
or particulate filters, and pumps as dictated by the application. Stainless steel tubing is essential for maintaining the
integrity of the gas stream for very low % or PPM O
2
level analysis.
Operating Temperature: The sample must be sufficiently cooled before it enters the analyzer and any optional
components. A coiled 10 foot length of ¼” stainless steel tubing is sufficient to cool sample gases as high as 1,800 ºF
to ambient temperature. The recommended operating temperature is below 35 ºC. However, the analyzer may be
operated at temperature up to 45 ºC on an intermittent basis but the user is expected to accept a reduction in
expected sensor life –as a rule of thumb, for every degree ºC increase in temperature (above 25 ºC), the sensor life is
reduced by approximately 2.5%.
Heat: Situate and store the analyzer away from direct sources of heat.
Liquid and Object Entry: The analyzer should not be immersed in any liquid. Care should be taken so that liquids
are not spilled into and objects do not fall into the inside of the analyzer.
Handling: Do not use force when using the switches, knobs or any other mechanical components. Before moving your
analyzer be sure to disconnect the wiring/power cord and any cables connected to the output terminals of the
analyzer.
Sample Pressure and Flow
All electrochemical oxygen sensors respond to partial pressure changes in oxygen. The sensors are equally capable of
analyzing the oxygen content of a flowing sample gas stream or monitoring the oxygen concentration in ambient air
(such as a confined space in a control room or an open area around a landfill or bio-pond). The following is applicable
to analyzers equipped with fuel cell type oxygen sensors.
Inlet Pressure
: For the analyzers designed to measure oxygen in a flowing gas stream, the inlet sample
pressure must be regulated between 5-30 psig. Although the rating of the SS tubing and tube fittings/valves itself is
considerably higher (more than 100 psig), a sample pressure of 5-30 psig is recommended for ease of control of
sample flow.
The analyzer equipped with a sample system has designated SAMPLE and VENT ports. Connect SAMPLE gas to
SAMPLE and the vent to the VENT ports only.
6