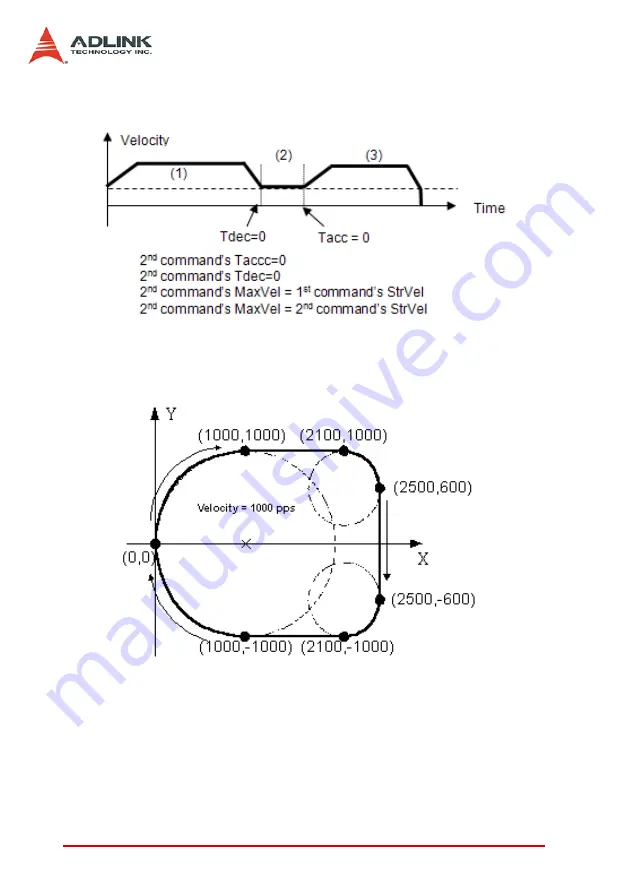
54
Operation Theory
If the 2nd command’s speed value is lower than the others, the
settings would be like as following diagram:
For 4-axis continuous arc interpolation is the same concept. You
can set the speed matched between two command speed set-
tings.
If the INP checking is enabled, the motion will have some delayed
between each command in buffers. INP check enabled make the
desired point be reached but reduce the smoothing between each
command. If users don’t need this delay and need the smoothing,
please turn INP checking off.
Содержание PCI-8154
Страница 4: ......
Страница 28: ...18 Installation ...
Страница 47: ...Signal Connections 37 and stop signals to STA and STP pins on the K1 connector of the first PCI 8154 card ...
Страница 48: ...38 Signal Connections ...
Страница 98: ...88 Operation Theory ...
Страница 102: ...92 MotionCreatorPro 5 3 2 Select Menu The select menu appears after running MotionCreatorPro It is used to ...
Страница 103: ...MotionCreatorPro 93 5 3 3 Card Information Menu In this menu it shows some Information about this card ...
Страница 104: ...94 MotionCreatorPro 5 3 4 Configuration Menu In the IO_Config_1 menu users can configure ALM INP ERC EL ORG and EZ ...
Страница 106: ...96 MotionCreatorPro In the IO_Config_2 menu users can configure LTC SD PCS and Select_Input ...
Страница 108: ...98 MotionCreatorPro In the Pulse INT_Config menu users can configure pulse input output and move ratio and INT factor ...
Страница 129: ...MotionCreatorPro 119 5 3 8 Help Menu In this menu users can Click Mouse Right Key to show Help Infor mation ...
Страница 130: ...120 MotionCreatorPro ...
Страница 206: ...196 Function Library Pos Latch data Position ...
Страница 224: ...214 Function Library ...
Страница 226: ...214 Connection Example ...