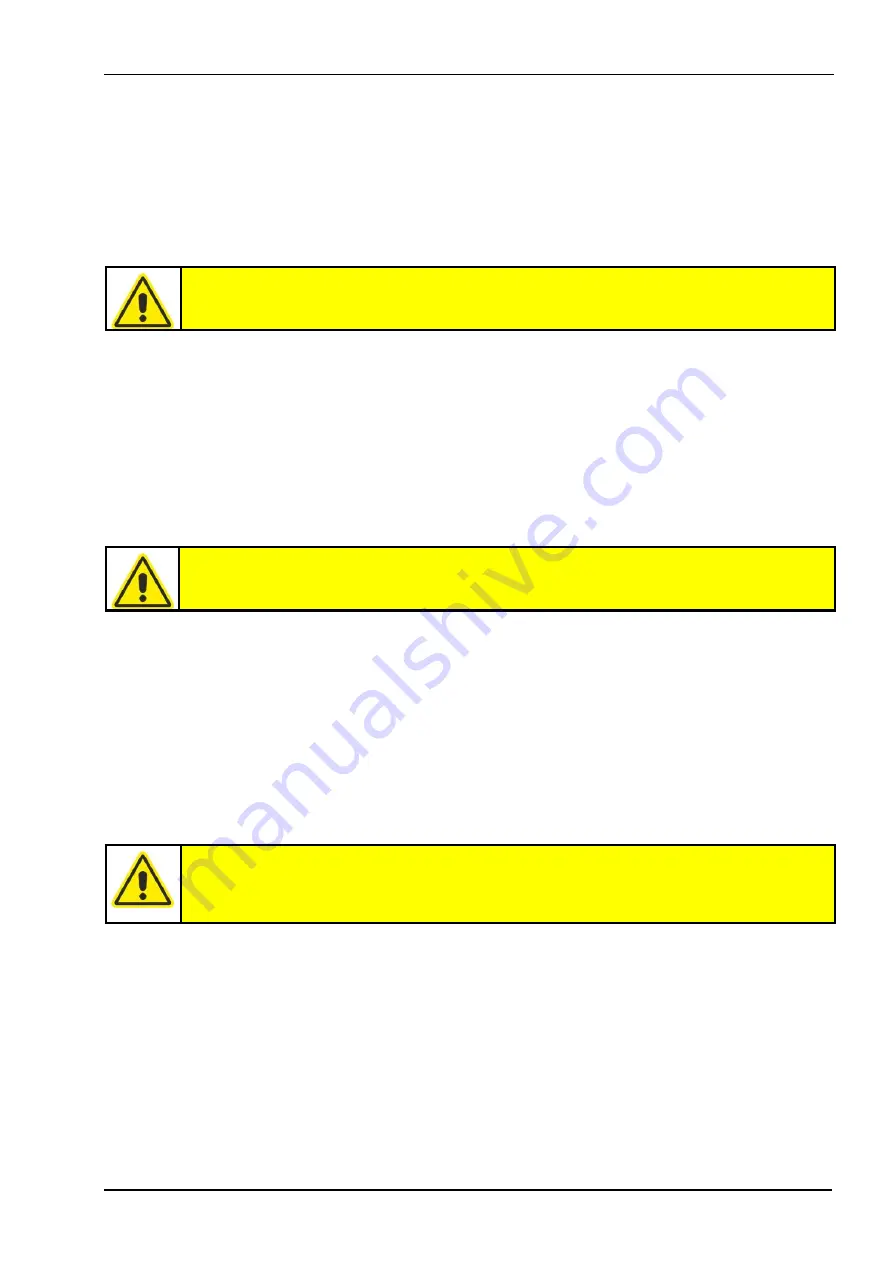
USER’S MANUAL V-line 899x.xxx/LPG
19
inspection, calibration and official certification of the LPG dispensing module are carried out
according to the regulation in force of the metrological office of the appropriate country
all identified defects are remedied after the inspection
Repairs of the filling station mechanical equipment are carried out after the identification of the faulty
condition symptoms and according to the conditions specified by the manufacturer of its individual parts.
The functional test and tightness test of the gas equipment are carried out after the completion of the
repair.
ATTENTION!
Service is performed by a service company authorised by the manufacturer!
13.
TRANSPORT
The customer shall agree to the method of dispenser transport from the manufacturer in the contract. In
case Adast Systems, a.s. provides the transport for the customer, the product will be delivered to the
agreed destination. The manufacturer possesses the necessary knowledge of handling and transportation
methods. In case the customer is responsible for another method of transport, the manufacturer shall
ensure professional loading of the product but is not responsible for the transport itself. It is generally
accepted that the dispenser shall be shipped properly boxed and always fixed to the wood pallete. The
dispenser should be protected against damage (of covering and painting), displacement and rolling over on
the means of transport. All manipulation and transport have to be carried out only in vertical position -
the dispenser must not be put on its covering.
ATTENTION!
Only forklifts are allowed to be used for manipulation. If other handling devices are used,
Adast Systems, a.s. does not guarantee any prospective damage!
14.
DISPENSER INSTALLATION
The dispenser can be joined only to process equipment (tanks, piping) of perfect tightness and cleanness.
The supplier of the process equipment is responsible for its tightness and cleanness.
The dispenser installation is carried out by the organisation authorised by the manufacturer.
Prior to
the installation the organisation shall perform the inspection of used power and communication cables.
When the dispenser is installed, they shall check the tightness, function of hydraulic equipment of the
dispenser, supply piping and fittings. They also check power and communication cables including their
lines and fixing. At least 100 dm
3
of LPG has to be discharged from each dispensing nozzle with Q
max
.
Prior to official metrological testing the dispenser (every dispensing nozzle) has to operate for min. 5
minutes in max. flow rate.
ATTENTION!
The process and service equipment of filling stations can be operated only when they have
been built up according to the approved design and on the basis of positive result of
licence regime.
14.1.
Hydraulic section
Seat and set in concrete the levelled steel base frame – delivered on special request by dispensers’
manufacturer – on the shaft with the supply pipeline and return piping from the storage tank.
In case the customer makes use of his own base frame, the frame must meet the requirements of the
sufficient rigidity, flatness and proper positions of fixing holes.
It is recommended to fasten the frame to a pedestal approximately 200 mm over the terrain for the
reason of easier assembly and handling or servicing purposes. The shaft, after having connected the piping
and the electric conductors to the dispenser, should be filled at least to the terrain level in order to
prevent the propane-butane gas from accumulating in the well and caverns for being heavier than air.
Attach the dispenser to the embedded frame.
Содержание MINOR LPG
Страница 2: ......
Страница 3: ......
Страница 4: ......
Страница 30: ......
Страница 31: ...USER S MANUAL V line 899x xxx LPG Enclosure No 1 Main dimensions of dispensers V line popular 899x xxx LPG ...
Страница 37: ...USER S MANUAL V line 899x xxx LPG Enclosure No 7 Installation dimensions of V line 8991 6x3 LPG ...